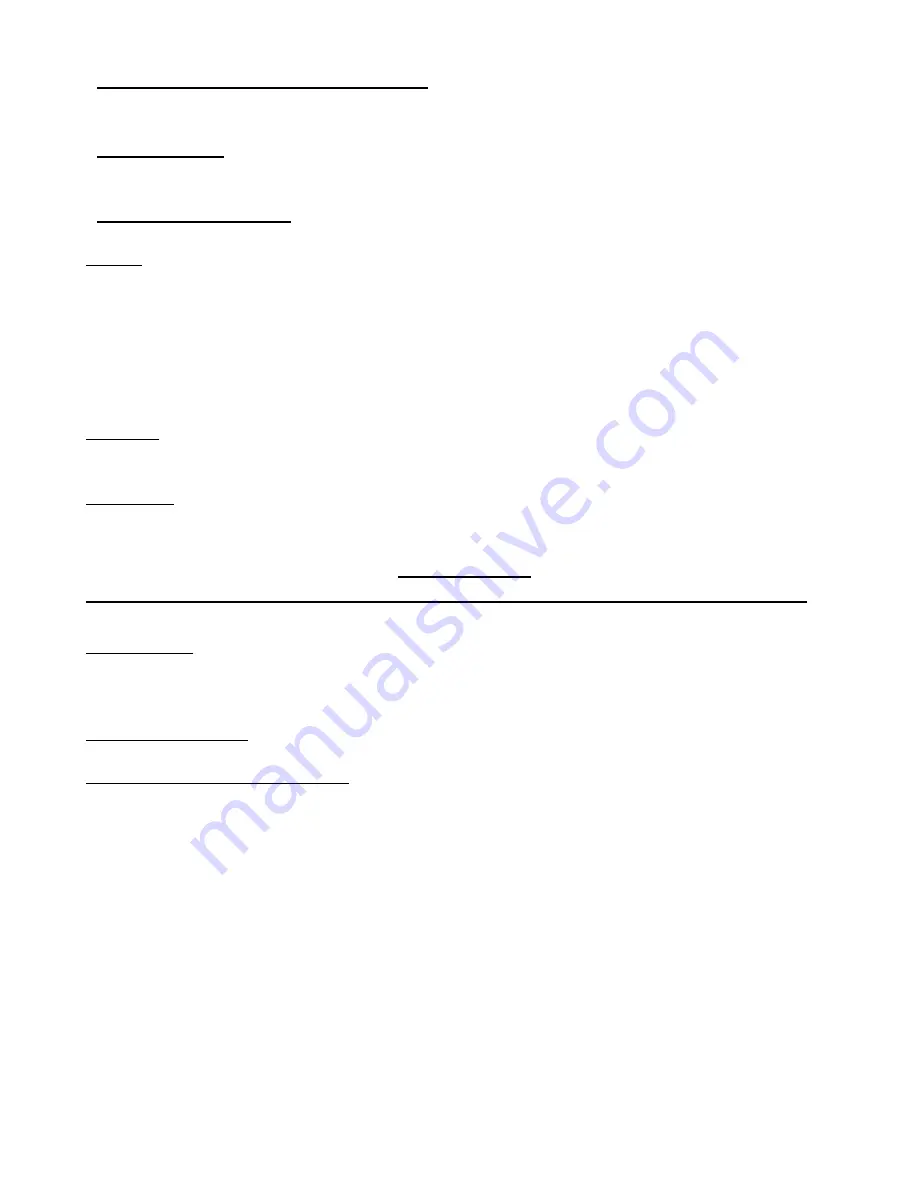
16
MAINTENANCE INSTRUCTIONS
The maintenance is to be performed by factory trained lift service personnel only.
Important:
Regularly inspect the hydraulic pressure developed upon the rated capacity,
and make sure the pressure doesn’t exceed the operating pressure (2500 psi).
LIFT MAINTENANCE :
The following is a minimum maintenance schedule:
DAILY: - Raise and lower the lift
(with no vehicle)
at the beginning of each shift to verify the
runways are level, safety locks are engaging, and the lift is operating properly.
- Check all hydraulic fittings and lines for damage and leaks. Check electrical wiring
for damage. Check all moving parts for uneven or excessive wear. Repair or
replace all damaged, worn, or broken components immediately.
- Clean all debris from the base frame area
- Remove oil/grease on runways and rolling jack lift pads.
WEEKLY: - Check hydraulic fluid in reservoir and top up if required.
- Check cables, cable pulleys and lifting cylinder.
MONTHLY: - Check that all anchor bolts are torqued to 75 ft-lbs (102Nm).
- Clean and lubricate moving parts (diagram 18).
WARNING:
FAIL TO LUBRICATE MAY CAUSE PERMENENT DAMAGE TO THE LIFT.
EVERY YEAR: - Have a certified lift technician inspect and certify all aspects of the lift as per
"Automotive Lift Operation, Inspection and Maintenance" (ALOIM)
guidelines.
EVERY TWO YEARS: - Change and replace hydraulic oil in cylinders and powerpack reservoir.
LUBRICATION SPECIFICATIONS: -where grease is required use a multi-purpose lithium grease
- where lubricating oil is required use a SAE 30 oil
- where hydraulic oil is required use ISO 32 hydraulic oil
(10W non detergent)
The following criteria will determine when a lifting cable is no longer acceptable
for service:
12 randomly distributed broken wires in one lay or four broken wires in one strand in one
lay in running ropes
one outer wire broken at the contact point with the core of the rope, which has worked its
way out of the rope structure and protrudes or loops out from the rope structure
wear of one-third the original diameter of outside individual wires
Summary of Contents for TLS430FDCEx1 Series
Page 23: ...23 Diagram 2 Front Crossmember...
Page 25: ...25 Diagram 3 Rear Crossmember...
Page 29: ...29 Diagram 6 Lifting Cable Routing...
Page 32: ...32 Diagram 8 Anchor Bolt Installation...
Page 33: ...33 Diagram 9 Driver Side Runway Assembly...
Page 41: ...41 Diagram 17 Power Unit Wiring Diagram...