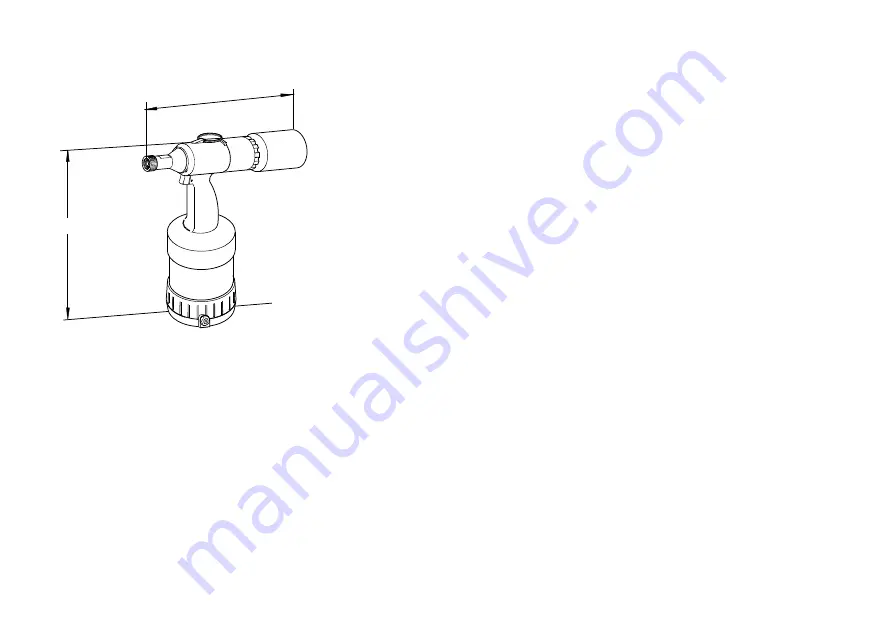
31
Disposing of the riveting tool
Ensure that the hydraulic oil is inside the riveting tool. Dispose it off in an
environmentally friendly manner.
Send the riveting tool back to the manufacturer in it’s original packing, if
still available.
Technical data
Type of riveting tool:
MS 75
Height:
320 mm (without tension head)
Width:
275 mm (without tension head)
Weight:
1.9 kg
Operating pressure:
5-7 bar
Compressed air supply
nominal diameter:DN 6
Power output (at 6 bar):
approx. 24 kN
Operating stroke:
approx. 15 mm
Operating range
Locking ring bolt:
C106/ C6L
5.0 - 6.5 mm
MAGNA-GRIP
5.0 and 6.5 mm
Blind rivet:
MAGNA-LOK/ BULB
5.0 and 6.5 mm
BOM
5.0 mm
Sound emission level
in the workplace:
L
PAI
<70dB(A)
Vibration level:
a
hw
<2,5m/s
2
Further technical data on the tension heads are enclosed with the tension
heads.
275 mm
320 mm