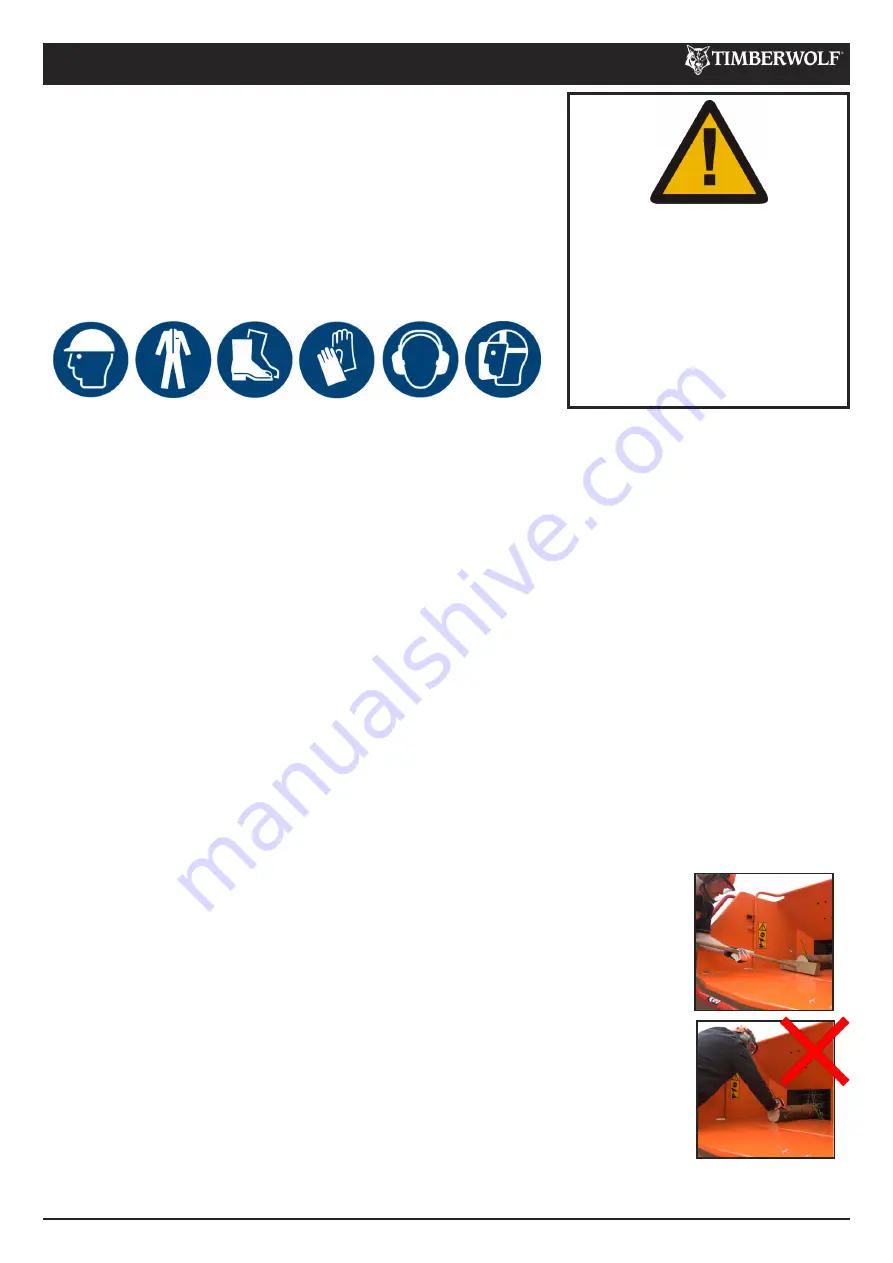
Always stop the chipper engine before making any adjustments, refuelling or cleaning.
•
Always check the rotor has stopped rotating and remove the chipper ignition key before maintenance of any
•
kind, or whenever the machine is to be left unattended. If in doubt, look through the in-feed funnel to see if
rotor is still moving.
Always check the machine is well supported and cannot move. If working on an incline, position on solid
•
ground, across the slope.
Always operate the chipper with the engine set to maximum speed when chipping.
•
Always check (visually) for fluid leaks. If found, resolve the leak before operating the chipper.
•
Always take regular breaks. Wearing personal protective equipment for long periods can be
•
tiring and hot.
Always keep hands, feet and clothing out of feed opening, discharge and moving parts.
•
Always use the next piece of material or a push stick to push in short pieces. Under no
•
circumstances should you reach into the funnel.
Always keep the operating area clear of people, animals and children.
•
Always keep the operating area clear from debris build up.
•
Always keep clear of the chip discharge tube. Foreign objects may be ejected with great
•
force.
Always ensure protective guarding is in place before commencing work. Failure to do so may
•
result in personal injury or loss of life.
Always operate the chipper in a well ventilated area - exhaust fumes are dangerous.
•
Ensure a fire extinguisher is available on site.
•
Ensure a personal first aid kit and hand cleaning materials are available (e.g. waterless skin cleanser).
•
The operator should be aware of the following points:
Maintain a safety exclusion zone around the chipper of at least 10 metres for the general public or employees
•
without adequate protection. Use hazard tape to identify this working area and keep it clear from debris build up.
Chips should be ejected away from any area the general public have access to.
Hazardous material - Some species of trees and bushes are poisonous. The chipping action can produce vapour,
•
spray and dust that can irritate the skin. This may lead to respiratory problems or even cause serious poisoning.
Check the material to be chipped before you start. Avoid confined spaces and use a face mask if necessary.
Be aware when the chipper is processing material that is an awkward shape. The material can move from side to
•
side in the funnel with great force. If the material extends beyond the funnel, the brash may push you to one side
causing danger. Badly twisted brash should be trimmed before being chipped to avoid thrashing in the feed funnel.
Be aware that the chipper can eject chips out of the feed funnel with considerable force. Always wear full head and
•
face protection.
Always work on the side of the machine furthest from any local danger, e.g. not road side.
•
Never leave the chipper unattended when running. Machines must be supervised at all times when in use.
•
In the event of an accident, stop the machine, remove the key and call the emergency services immediately.
•
5 / 65
SAFE WORKING
C190-0113
01.07.2019
Rev: 4.0
WARNING
Chainsaw safety helmet (EN 397) fitted with mesh visor (EN 1731) and
•
ear defenders (EN 352).
Work gloves with elasticated wrist.
•
Steel toe cap safety boots (EN 345-1).
•
Close fitting heavy-duty non-snag clothing. High-visability clothing (EN
•
471) if risk assessment identifies the need.
Face mask if appropriate.
•
DO NOT wear rings, bracelets, watches, jewellery or any other items
•
that could be caught in the material and draw you into the chipper.
OPERATOR'S PERSONAL PROTECTIVE EQUIPMENT (PPE)
BASIC WOODCHIPPING SAFETY
The chipper will feed material
through on its own. To do this, it
relies on sharp blades both on the
feed rollers and the chipper rotor.
To keep the blades sharp, only feed
the machine with clean brushwood.
DO NOT put muddy/dirty wood,
roots, potted plants, bricks, stones
or metal into the chipper.
GENERAL SAFETY MATTERS
TW 230VTR
ü
Summary of Contents for TW 230VTR
Page 1: ...timberwolf uk com TW 230VTR WOOD CHIPPER UKINSTRUCTION MANUAL...
Page 29: ...TW 230VTR 27 65 DECLARATION OF CONFORMITY C190 0113 01 07 2019 Rev 4 0...
Page 30: ...TW 230VTR 28 65 IDENTIFICATION PLATE C190 0113 01 07 2019 Rev 4 0 EXAM PLE...
Page 33: ...TW 230VTR 31 65 ELECTRICAL PARTS LOCATOR C190 0113 01 07 2019 Rev 4 0...
Page 35: ...TW 230VTR 33 65 HYDRAULIC LAYOUT C190 0113 01 07 2019 Rev 4 0...
Page 40: ...TW 230VTR 38 65 C190 0112 17 07 2019 Rev 3 0...
Page 41: ...39 65 C190 0112 17 07 2019 Rev 3 0 TW 230VTR...
Page 42: ...TW 230VTR 40 65 C190 0112 17 07 2019 Rev 3 0...
Page 43: ...41 65 C190 0112 17 07 2019 Rev 3 0 TW 230VTR...
Page 44: ...TW 230VTR 42 65 C190 0112 17 07 2019 Rev 3 0...
Page 45: ...TW 230VTR 43 65 C190 0112 17 07 2019 Rev 3 0...
Page 46: ...TW 230VTR 44 65 C190 0112 17 07 2019 Rev 3 0...
Page 47: ...TW 230VTR 45 65 C190 0112 17 07 2019 Rev 3 0...
Page 48: ...TW 230VTR 46 65 C190 0112 17 07 2019 Rev 3 0...
Page 49: ...47 65 C190 0112 17 07 2019 Rev 3 0 TW 230VTR...
Page 51: ...TW 230VTR 49 65 C190 0112 17 07 2019 Rev 3 0...
Page 52: ...TW 230VTR 50 65 C190 0112 17 07 2019 Rev 3 0...
Page 53: ...TW 230VTR 51 65 C190 0112 17 07 2019 Rev 3 0...
Page 54: ...TW 230VTR 52 65 C190 0112 17 07 2019 Rev 3 0 Kit No P2821...
Page 55: ...TW 230VTR 53 65 C190 0112 17 07 2019 Rev 3 0...
Page 56: ...54 65 C190 0112 17 07 2019 Rev 3 0 TW 230VTR...
Page 57: ...TW 230VTR 55 65 C190 0112 17 07 2019 Rev 3 0...
Page 58: ...TW 230VTR 56 65 C190 0112 17 07 2019 Rev 3 0...
Page 59: ...TW 230VTR 57 65 C190 0112 17 07 2019 Rev 3 0...
Page 60: ...TW 230VTR 58 65 C190 0112 17 07 2019 Rev 3 0...
Page 61: ...TW 230VTR 59 65 C190 0112 17 07 2019 Rev 3 0...
Page 62: ...TW 230VTR 60 65 C190 0112 17 07 2019 Rev 3 0...
Page 63: ...61 65 C190 0112 17 07 2019 Rev 3 0 TW 230VTR...
Page 64: ...62 65 C190 0112 17 07 2019 Rev 3 0 TW 230VTR...
Page 65: ...63 65 C190 0112 17 07 2019 Rev 3 0 TW 230VTR SUPPLIED WITH WINCH KIT P2030 P0002390...