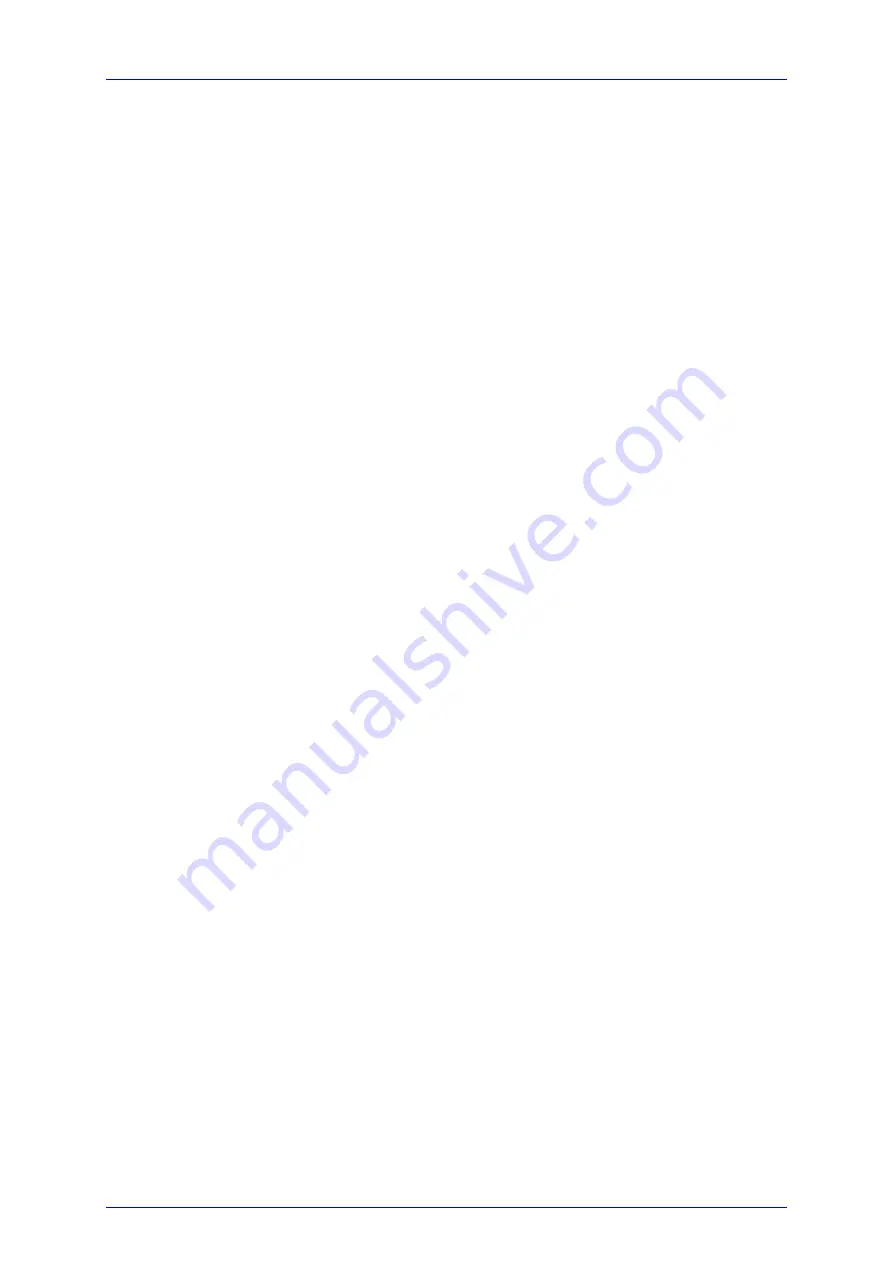
3.1 General notes on remote control
Temperature module TED8xxx / page 45
Numeric response data Type 2 (<NR2>)
Is a numerical value with or without sign in floating point notation without exponent.
Examples:
1.1 or +1.1 or -22.1 or 14356.789432
#
(Refer to IEE488.2 (8.7.3))
Numeric response data Type 3 (<NR3>)
Is a numerical value with or without sign in floating point notation with exponent with
sign . Examples:
1.1E+1 or +1.1E-1 or -22.1E+1 or 143.56306
(Refer to IEE488.2 (8.7.4))