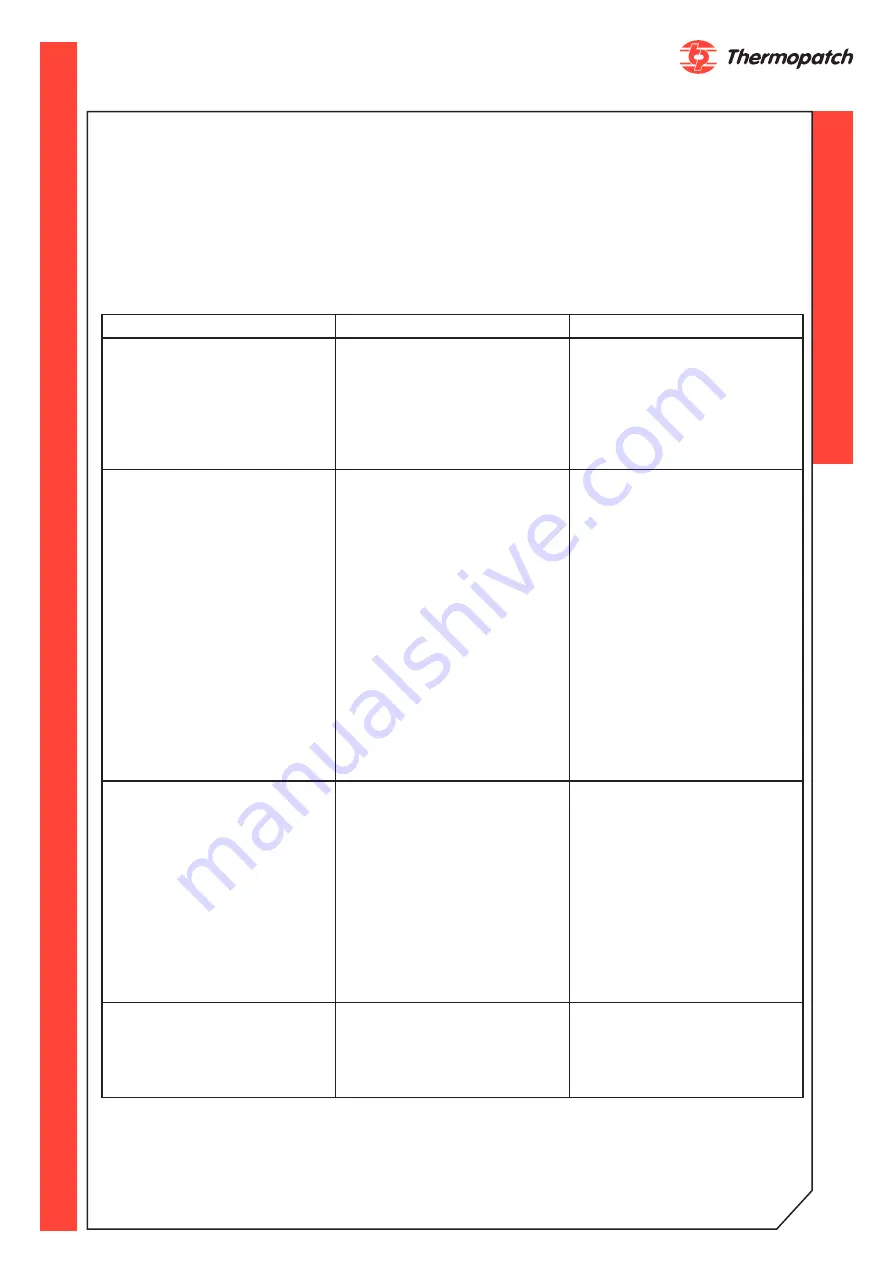
thermopatch.com
24
7. Troubleshooting
Before referring to the information below, check for proper set-up and operation as outlined
in “DP2000T Setup”.
Solutions are listed with the most probable ones listed first.
Some procedures may require completion by a person with some mechanical and electrical
skill. Call Customer Service for assistance or to order replacement parts.
Problem
Possible Cause
Solution
Display is blank
Machine is unplugged or
outlet has no power
Emergency stop activated
Electrical power switch or
light not “ON” or is defective
Loose or broken wires or
connectors
Check
Check
Check/Replace
Check/Repair
No heat
Machine is unplugged or out-
let has no power
Electrical power switch is not
“ON” or is defective
Temperature reading is in-
correct
Print Head heat is defective
Heat sensor is defective
Defective temperature con-
trol
Loose or broken wires or
connectors
High limit thermostat is de-
fective
Check
Check/Replace
Replace
Replace
Replace
Replace
Check/Repair
Replace
High or low heat
Heat sensor is defective
Defective temperature con-
troller
Temperature reading is in-
correct
Loose or bad connectors
Short between sensor wires
(high heat only)
Replace
Replace
Adjust
Check/Repair
Check/Repair
Print pressure drops or fluc
-
tuates (on air (gauge) or
hisses
Leak in air supply hose
Dust is lodged in the air
lines, regulator,
or solenoid air valves
Repair/Replace
Disassemble and clean