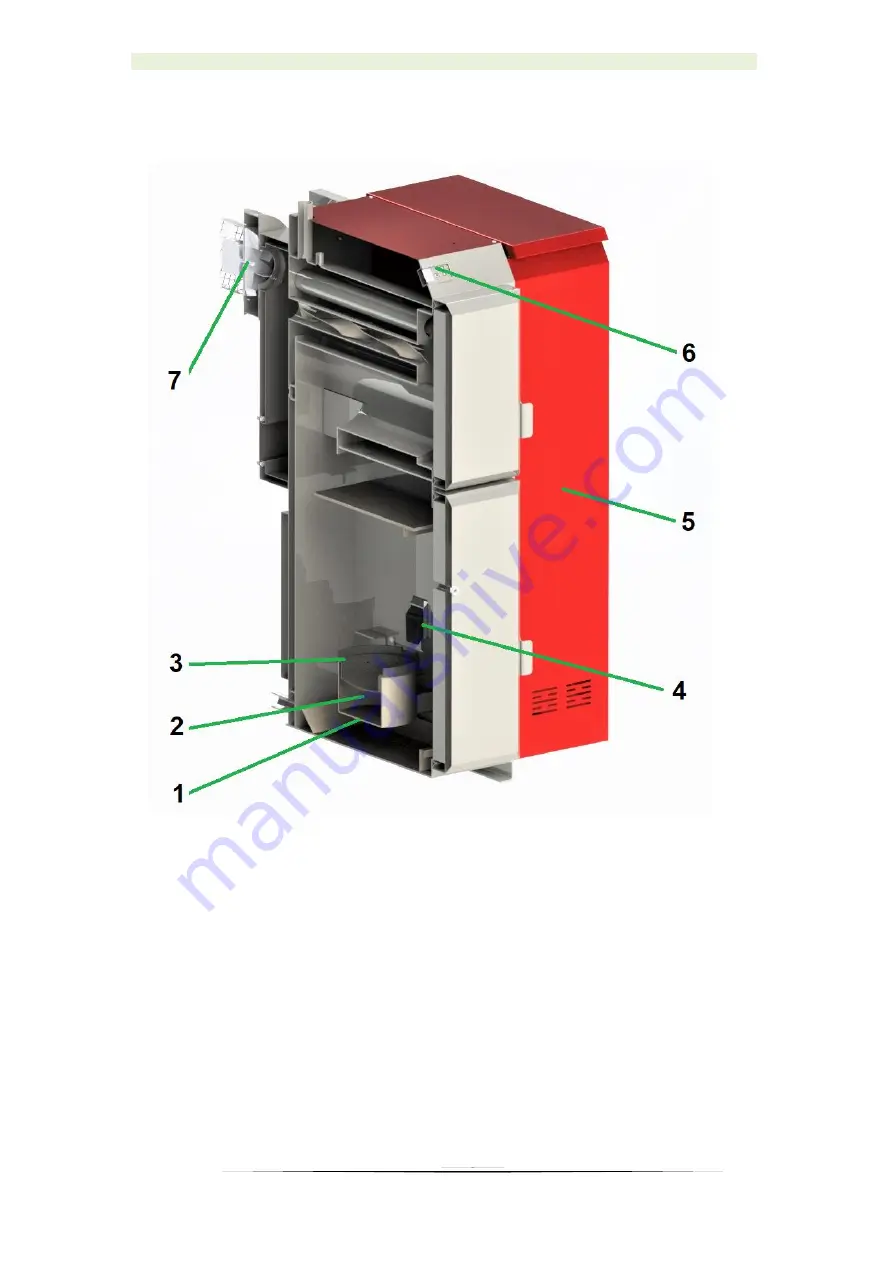
PELLING
11
3.2
Pellet boiler PELLING
1.
Combustion burner
2.
Heater
3.
Combustion chamber
4.
Dispenser
5.
Silo
6.
Control unit
7.
Exhaust fan
In the Pelling boiler the pellets introduced into the combustion burner 1. They are
automatically ignited with an electric heater 4. Burnt pellet (ash) is collected in the ash
pan 3. which is placed under the combustion burner. The air necessary for combustion
is supplied to the combustion burner.
The boiler power is aligned to the requirements of the cetral heating system.
The usability and efficiency of the boiler is pre-optimized.
Summary of Contents for Pelling 100
Page 2: ...2...
Page 17: ...PELLING 17...
Page 18: ...PELLING 18 Clock adjustments Clock adjustments can be done on following way...
Page 20: ...PELLING 20 Flowchart 2 Flowchart 3 Flowchart 4...
Page 37: ...PELLING 37 8 Connection options 8 1 Hydraulic schemes for connection...
Page 38: ...PELLING 38...
Page 39: ...PELLING 39...
Page 40: ...PELLING 40...
Page 43: ...PELLING 43...
Page 47: ...PELLING 47 12 EU Label...
Page 48: ...PELLING 48...
Page 49: ...PELLING 49...