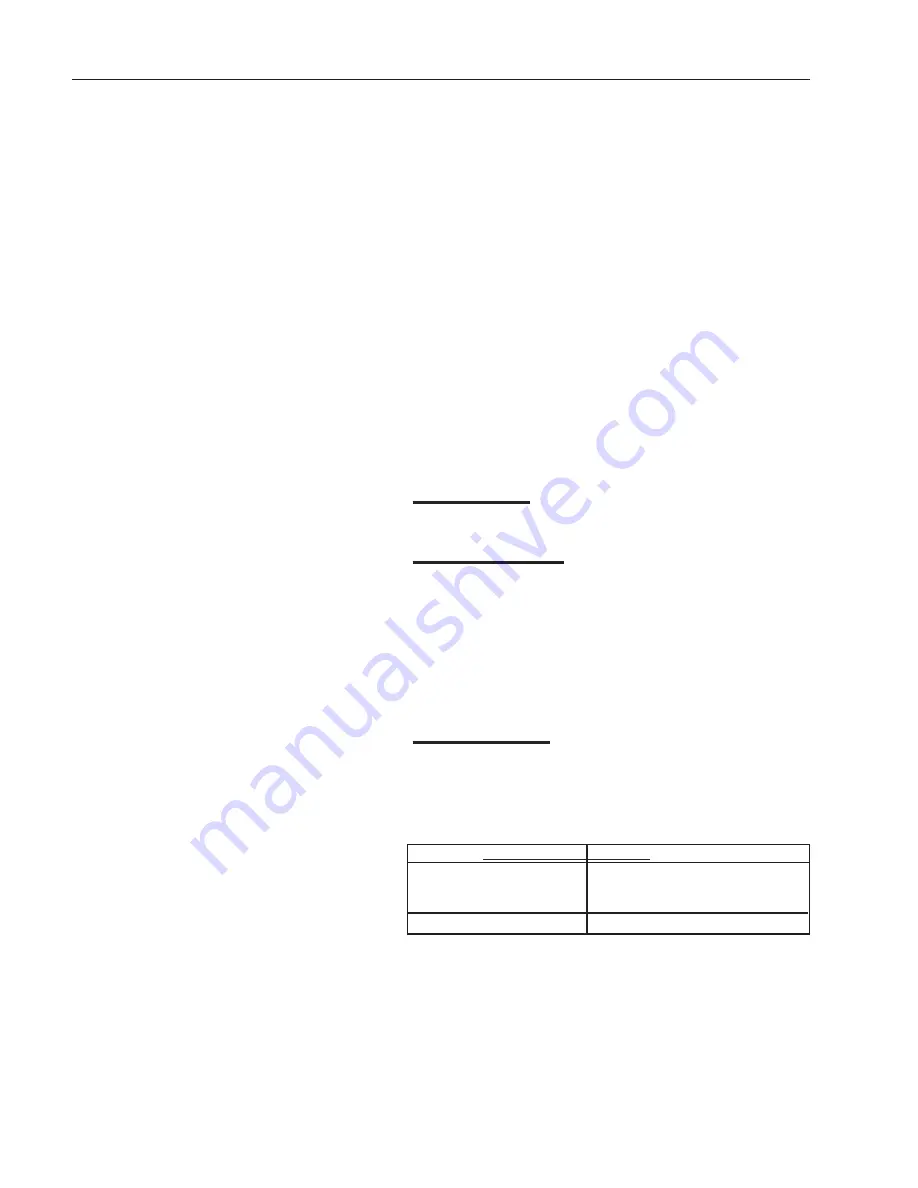
22
The Barnstead ULTROpure Reverse Osmosis System is
automatically operated by a microprocessor controller. This
controller monitors and responds to the ULTROpure pro-
tective interlocks and storage reservoir level sensors.
The ULTROpure is equipped with a % Rejection Monitor.
This feature provides a digital display of resistivity, water
temperature and percentage salt rejection, as well as offer-
ing a visual indication that the percent rejection rate is
above a user definable setpoint.
The following operating sequence illustrates automatic op-
eration, events and features of the basic microprocessor
controller as well as operation of the % Rejection Monitor.
Controller
Power Up Mode
Each time the ULTROpure is turned on, a 30-second delay
allows water to enter and fill the system before the high
pressure pump starts. During the first 10 seconds of this
delay, the low feedwater pressure switch is locked out to
prevent premature shutdown triggered by the sudden, ini-
tial pressure surge of the pump.
Running Mode
The ULTROpure safety interlocks are activated in the run-
ning mode to respond, if necessary, to fault conditions. The
active interlocks and corresponding functions are:
Switches
Functions
Low feedwater pressure
High pressure pump
protection
High membrane pressure
System protection
Should a fault condition be detected, the switch signals the
controller to shut down the ULTROpure. During the shut-
down period, the indicator light corresponding to the exist-
ing fault condition will be illuminated.
The user must investigate the cause of the fault condition
prior to system restart. This is accomplished by noting the
specific indicator light, turning to the Troubleshooting Chart
(beginning on page 34 of this manual) and performing the
applicable test and remedy procedure.
Controller and % Rejection Monitor
Summary of Contents for ULTROpure 682 Series
Page 5: ...5 Figure A Flow Diagram ...
Page 37: ...37 Wiring Schematic for Customer Supplied Switches for Storage Reservoirs Schematics ...
Page 41: ...41 ...
Page 42: ...42 ...
Page 43: ...43 ...