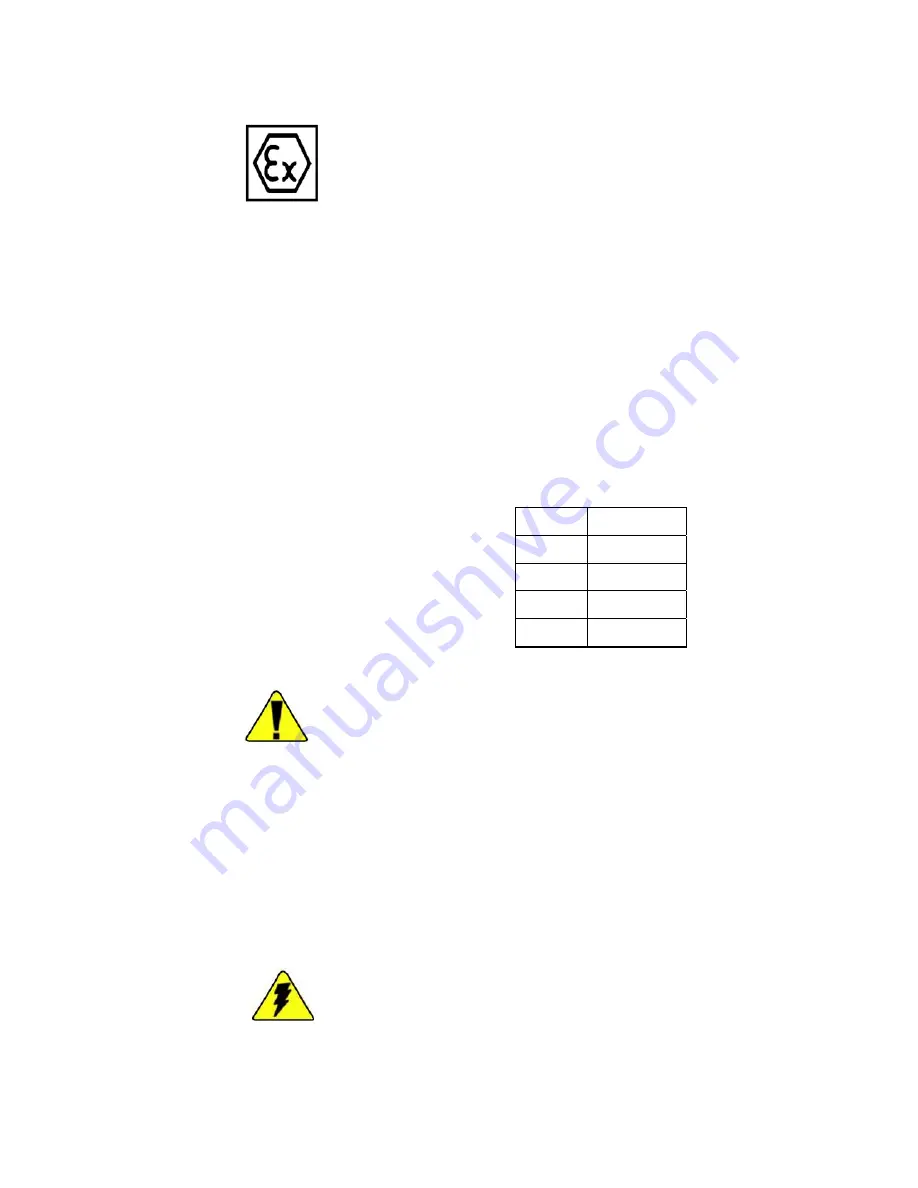
Specifications
ATEX
STD5000 and STD6000 IS operation
Enclosure is manufactured from aluminum alloy. In rare cases, ignition
sources due to impact and friction sparks could occur. This shall be
considered when equipment is installed in locations that specifically require
Group II, Category IG equipment.
Equipment may be used in Zones 0, 1, and 2 with flammable gases and
vapors with temperature classes T1, T2, T3, and T4. Installation must be
in accordance with applicable code of practice (e.g. EN 60079-14).
Equipment may also be used in the presence of explosive dust atmospheres
in Zones 20, 21, and 22. Installation must be in accordance with applicable
codes of practice (e.g. EN 61241-14). Be sure to apply the required safety
margins for temperature.
The equipment must be connected to a suitably certified ATEX barrier
whose parameters must be compatible with the following electrical
parameters:
U
i
30Vdc
I
i
100mA
P
i
0.75W
C
i
5.3nF
L
i
7μH
STD6000 flame proof operation
Refer to the STD6000 label in
Figure C–2
.
In accordance with the exclusion of EN 60079-1-2007 clause 15.4.3.2.2
for enclosures containing sinters and with volumes above 0.1 L, the
STD6000 converter shall not be used in the presence of carbon disulphide.
Equipment is supplied with a ½-inch NPTF (tapered) thread for electrical
connections, which shall be as follows:
1.
An approved metallic conduit incorporating a stopper box, or
2.
A suitably certified flame proof gland.
Warning
Parallel thread glands should not be inserted directly into the
tapered thread conduit entry without the use of a suitably certified flame
proof ½-inch NPTF-to-metric adapter.
▲
Thermo Fisher Scientific
STD5000 & STD6000 User Guide
C-5
Summary of Contents for STD5000
Page 1: ...STD5000 STD6000 Current to Pressure Transducers User Guide P N MA45 5600 00 Revision...
Page 2: ......
Page 4: ...This page intentionally left blank...
Page 6: ...This page intentionally left blank...
Page 8: ...This page intentionally left blank...
Page 18: ...This page intentionally left blank...
Page 24: ...This page intentionally left blank...
Page 32: ...This page intentionally left blank...
Page 34: ...This page intentionally left blank...
Page 43: ...Specifications Figure C 2 Thermo Fisher Scientific STD5000 STD6000 User Guide C 7...