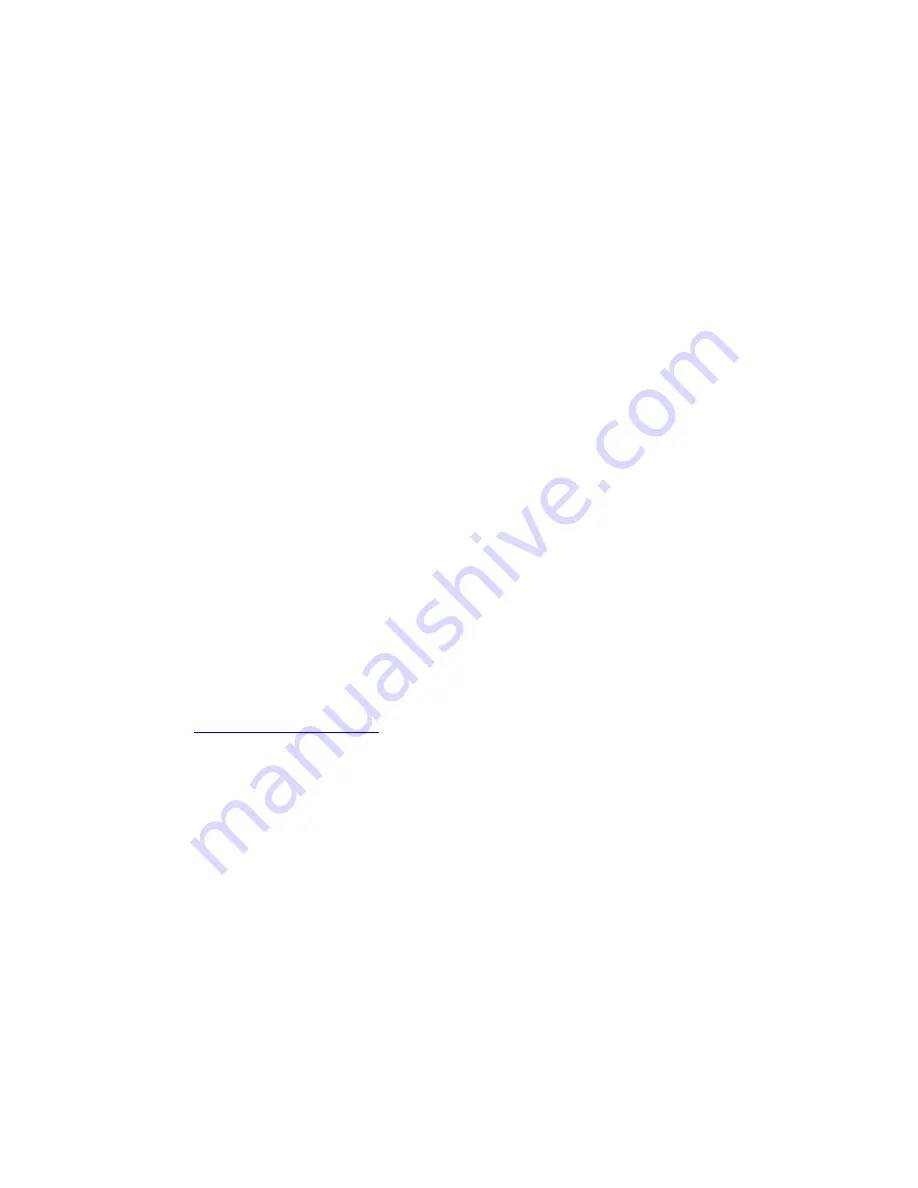
Thermo Scientific AquaSensors
™
DataStick
™
Ethernet Communications User Guide
54
7 Modbus TCP and PCCC
This section describes the Modbus TCP and Programmable Controller Communication
Commands (PCCC).
7.1 Modbus TCP
The product supports all measure, calibrate, configure and diagnose features of the
DataStick via Modbus TCP.
According to the Modbus-IDA Website:
The Modbus Protocol is a messaging structure developed by Modicon in 1979. It
is used to establish master-slave/client-server communications between
intelligent devices. It is a de facto standard, truly open and the most widely used
network protocol in the industrial manufacturing environment. It has been
implemented by hundreds of vendors on thousands of different devices to
transfer discrete/analog I/O and register data between control devices. It's a
lingua franca or common denominator between different manufacturers.
TCP/IP is the common transport protocol of the Internet and is actually a set of
layered protocols, providing a reliable data transport mechanism between
machines. Ethernet has become the de facto standard of corporate enterprise
systems, so it comes as no surprise that it has also become the de facto standard
for factory networking. Ethernet is not a new technology. It has matured to the
point that the cost of implementing this network solution has been dropping to
where its cost is commensurate with those of today's field-buses.
Using Ethernet TCP/IP in the factory allows true integration with the corporate
intranet and MES systems that support the factory. To move Modbus into the
21st century, an open Modbus TCP/IP specification was developed in 1999. The
protocol specification and implementation guide are available for download
Combining a versatile, scaleable, and ubiquitous physical network (Ethernet)
with a universal networking standard (TCP/IP) and a vendor-neutral data
representation, Modbus gives a truly open, accessible network for exchange of
process data.
The Modbus TCP registers are defined in the tables in Section 7.3,