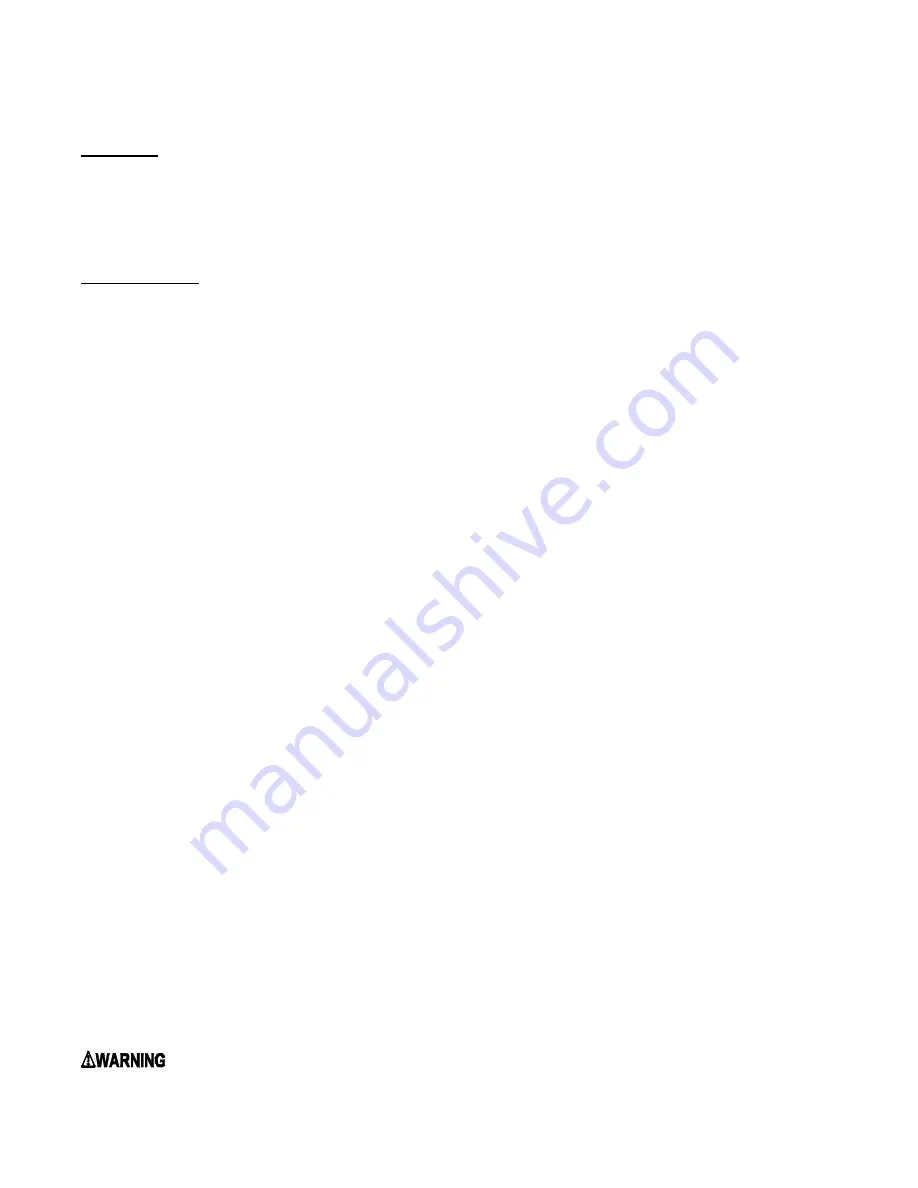
All installations and services must be performed by qualified service personnel.
51
VI. TROUBLESHOOTING
NOTICE:
Before troubleshooting, familiarize yourself with the startup and checkout procedures.
To assist you in troubleshooting this furnace, it is equipped with an integrated ignition control with
diagnostics. These diagnostics evaluate what control system has experienced a failure and will activate a
flashing light on the control in different sequences to help pinpoint the failure which has occurred.
IMPORTANT:
For your convenience, Thermo Products has installed a sight glass in the blower door of
this furnace. The number of flashes in groups should be observed through this sight glass and recorded
before turning off power to the furnace. Momentarily pressing the “Last Error” button on the control
board will initiate the display of the last 5 failure codes, even if the furnace power has been shut off.
Holding the “Last Error” button for 5 seconds, or more, will erase the error history.
DIAGNOSTIC FEATURES
The integrated control continuously monitors its own operation and the operation of the system. If a
failure occurs, the LED will indicate a failure code as shown below. If the failure is internal to the control,
the light will stay on continuously. In this case, the entire control should be replaced, as the control is not
field-repairable.
If the sensed failure is in the system (external to the control), the LED will flash in the following flash-
pause sequences to indicate failure status (each flash will last approximately 0.25 seconds, and each pause
will last approximately 1 second).
CLQS1 (Single Stage Furnaces)
LED Off - No power to control, pushbutton switch pressed, or control fault
LED steady ON (Any color) - Control hardware fault detected
Slow Green flash - No call for heat, no active errors
Slow Orange flash - Call for heat present, no active errors
1 RED flash - High limit switch open
2 RED flashes - Pressure switch open with inducer on
3 RED flashes - Pressure switch closed with inducer off
4 RED flashes - 1 hour lockout code
5 RED flashes - Incorrect line voltage polarity or incorrect polarity on 24 VAC line from
transformer
6 RED flashes – Too many limit trips in one call for heat
7 RED flashes – Pressure switch cycle lockout
8 RED flashes - Too many flame dropouts detected
9 RED flashes – Not Used
10 RED flashes – Flame present with gas valve off
Rapid flash – Incorrect 24 VAC phasing/twinning error
: Power must be disconnected before servicing.
Summary of Contents for CLQS1-050T36N
Page 2: ......
Page 4: ......
Page 47: ...All installations and services must be performed by qualified service personnel 45...
Page 55: ...All installations and services must be performed by qualified service personnel 53...
Page 56: ...All installations and services must be performed by qualified service personnel 54...
Page 57: ...All installations and services must be performed by qualified service personnel 55...
Page 59: ...All installations and services must be performed by qualified service personnel 57...
Page 60: ...All installations and services must be performed by qualified service personnel 58...