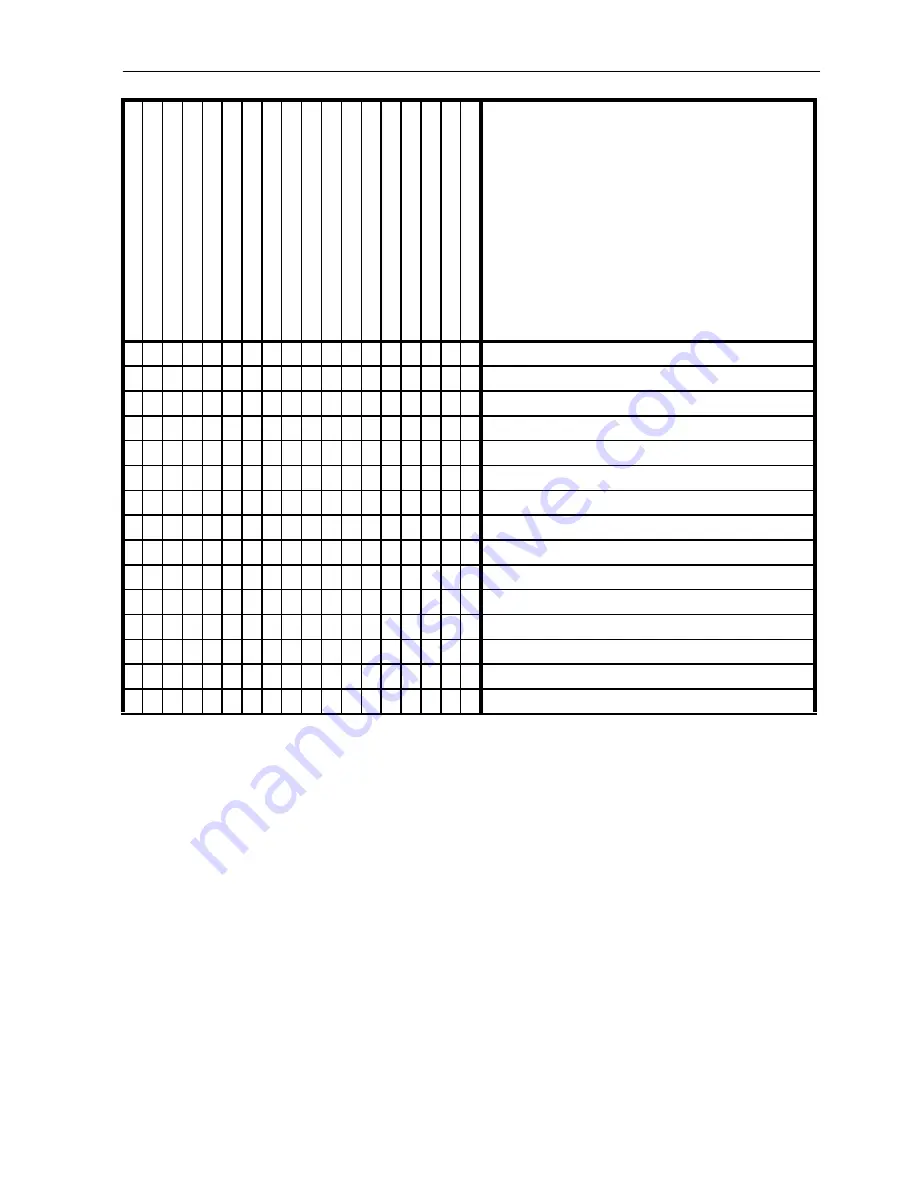
Refrigeration Diagnosis
147
•
•
•
•
Leaky Zone 1 hot gas solenoid (HGS)
•
•
Closed Zone 1 hot gas solenoid (HGS)
•
•
•
Leaky Zone 1 liquid line solenoid (LLS)
•
•
•
•
•
•
Closed Zone 1 liquid line solenoid (LLS)
•
Leaky Zone 1 liquid return check vale (LRCV)
•
•
Leaky Zone 1 suction line solenoid (SLS)
•
•
•
Leaky Zone 1 suction line check valve (SLCV)
•
•
Leaky Zone 2 hot gas solenoid (RHGS)
•
•
•
•
Closed Zone 2 hot gas solenoid (RHGS)
•
•
Leaky Zone 2 liquid line solenoid (RLLS)
•
•
•
Closed Zone 2 liquid line solenoid (RLLS)
•
Leaky Zone 2 liquid return check valve (RLRCV)
•
•
Leaky Zone 2 suction line solenoid (RSLS)
•
•
•
Leaky Zone 2 suction line check valve (RSLCV)
•
•
•
•
Leaky purge valve (PV)
R
api
d
c
y
c
ling be
tw
e
en C
o
o
l
a
nd H
e
a
t
Un
it co
o
ls in
He
a
t
a
n
d
De
fr
o
s
t
c
ycle
Un
it
h
e
a
ts in
r
e
fr
ig
e
ra
tio
n
c
ycle
H
igh he
ad
p
re
s
s
u
re
Lo
w he
ad
p
re
s
s
u
re
N
o
hea
d pr
es
s
u
re
H
igh s
u
c
ti
on pr
es
s
u
re
Lo
w s
u
c
ti
on pr
es
s
u
re
N
o
su
ct
io
n pr
es
su
re
U
n
it
o
p
e
rat
in
g i
n
a va
c
uum
R
e
c
e
iv
er
s
igh
t g
las
s
em
pt
y
S
u
c
ti
on l
in
e
fr
os
ti
n
g
ba
ck
U
nab
le
t
o
pum
p do
wn
s
y
s
te
m
Un
a
b
le
to
p
u
ll va
cu
u
m
in
lo
w
sid
e
Un
a
b
le
to
h
o
ld
v
a
c
u
u
m
in
lo
w s
id
e
No
isy
co
m
p
re
s
s
o
r
Un
it n
o
t
re
fr
ig
e
ra
tin
g
U
n
it
n
o
t hea
ti
n
g
or
def
ro
s
ti
n
g
Sy
mpto
m
Possible Causes
Summary of Contents for MD-MT
Page 4: ...4...
Page 10: ...Table of Contents 10...
Page 22: ...Specifications 22...
Page 43: ...Unit Description 43 Figure 15 Engine Side Door Open ARD041...
Page 48: ...Unit Description 48...
Page 128: ...Refrigeration Service Operations 128...
Page 134: ...Hilliard Clutch Maintenance 134...
Page 136: ...Structural Maintenance 136...
Page 148: ...Refrigeration Diagnosis 148...
Page 150: ...Remote Evaporator Specifications 150...
Page 152: ...Remote Evaporator Maintenance Inspection Schedule 152...
Page 156: ...Remote Evaporator Unit Description 156...
Page 160: ...Remote Evaporator Structural Maintenance 160...
Page 162: ...Remote Evaporator System Diagnosis 162...
Page 166: ...Wiring and Schematic Diagrams Index 166...
Page 167: ...167 MD RD MT Model 30 w In Cab Schematic Diagram Page 1 of 2...
Page 168: ...168 MD RD MT Model 30 w In Cab Schematic Diagram Page 2 of 2...
Page 169: ...169 MD RD MT Model 30 w In Cab Wiring Diagram Page 1 of 3...
Page 170: ...170 MD RD MT Model 30 w In Cab Wiring Diagram Page 2 of 3...
Page 171: ...171 MD RD MT Model 30 w In Cab Wiring Diagram Page 3 of 3...
Page 172: ...172 MD RD MT Model 30 w In Cab CYCLE SENTRY Schematic Diagram Page 1 of 2...
Page 173: ...173 MD RD MT Model 30 w In Cab CYCLE SENTRY Schematic Diagram Page 2 of 2...
Page 174: ...174 MD RD MT Model 30 w In Cab CYCLE SENTRY Wiring Diagram Page 1 of 3...
Page 175: ...175 MD RD MT Model 30 w In Cab CYCLE SENTRY Wiring Diagram Page 2 of 3...
Page 176: ...176 MD RD MT Model 30 w In Cab CYCLE SENTRY Wiring Diagram Page 3 of 3...
Page 177: ...177 MD RD MT Model 30 CYCLE SENTRY Wiring Diagram Page 1 of 3...
Page 178: ...178 MD RD MT Model 30 CYCLE SENTRY Wiring Diagram Page 2 of 3...
Page 179: ...179 MD RD MT Model 30 CYCLE SENTRY Wiring Diagram Page 3 of 3...
Page 180: ...180 MD RD MT Model 50 w In Cab Schematic Diagram Page 1 of 2...
Page 181: ...181 MD RD MT Model 50 w In Cab Schematic Diagram Page 2 of 2...
Page 182: ...182 MD RD MT Model 50 w In Cab Wiring Diagram Page 1 of 3...
Page 183: ...183 MD RD MT Model 50 w In Cab Wiring Diagram Page 2 of 3...
Page 184: ...184 MD RD MT Model 50 w In Cab Wiring Diagram Page 3 of 3...
Page 185: ...185 MD RD MT Model 50 w In Cab CYCLE SENTRY Schematic Diagram Page 1 of 2...
Page 186: ...186 MD RD MT Model 50 w In Cab CYCLE SENTRY Schematic Diagram Page 2 of 2...
Page 187: ...187 MD RD MT Model 50 w In Cab CYCLE SENTRY Wiring Diagram Page 1 of 3...
Page 188: ...188 MD RD MT Model 50 w In Cab CYCLE SENTRY Wiring Diagram Page 2 of 3...
Page 189: ...189 MD RD MT Model 50 w In Cab CYCLE SENTRY Wiring Diagram Page 3 of 3...
Page 190: ...190 MD RD MT Model 50 CYCLE SENTRY Wiring Diagram Page 1 of 3...
Page 191: ...191 MD RD MT Model 50 CYCLE SENTRY Wiring Diagram Page 2 of 3...
Page 192: ...192 MD RD MT Model 50 CYCLE SENTRY Wiring Diagram Page 3 of 3...