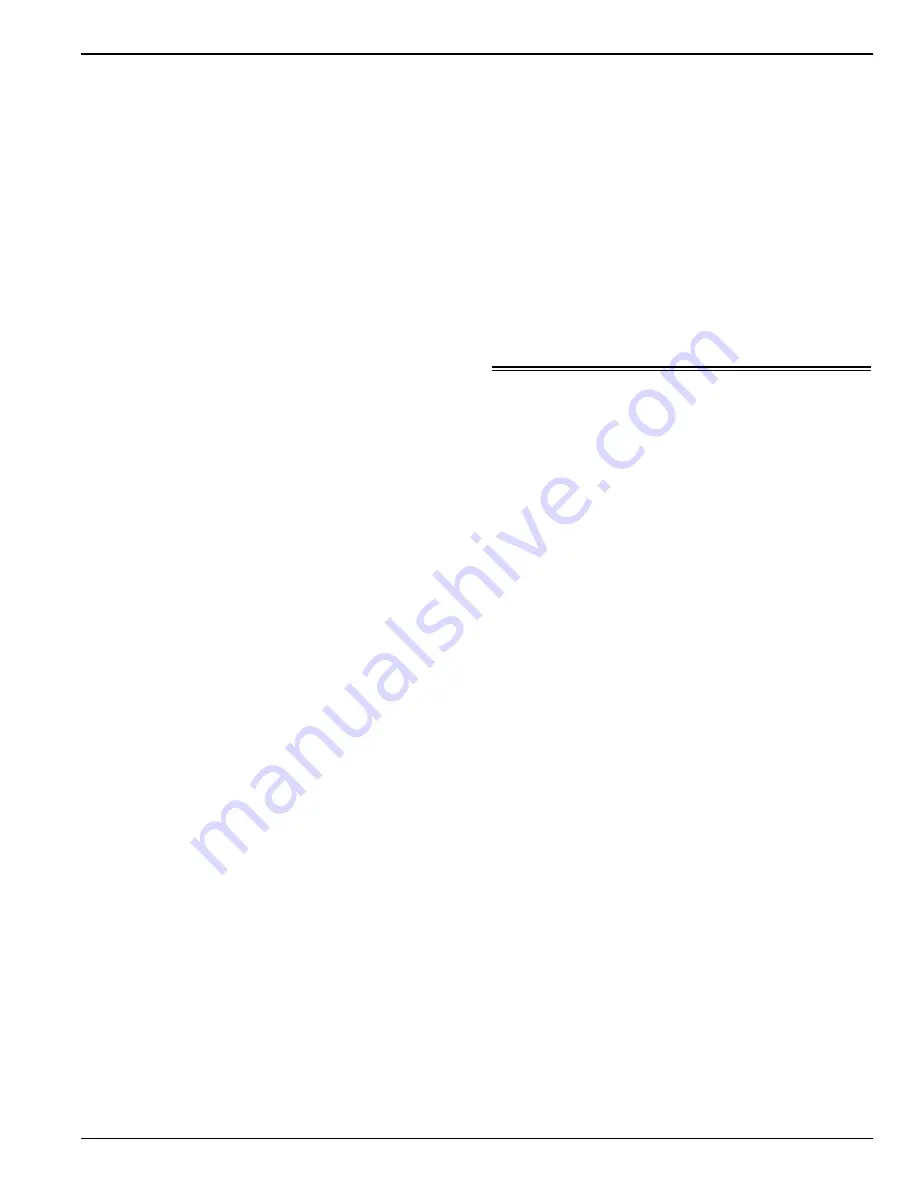
CSR-20 & CSR-40, September 1999
Operating Instructions
Pretrip Inspection
3-3
play will show “PAUSE ALM82” for 1 second every 10
seconds. After 5 minutes, the controller attempts to restart
the compressor. If the compressor still fails to start, fault
code 82 (Compressor Head Over Temperature) is generat-
ed. The controller will restart the compressor when the
fault condition corrects itself (resets).
4.
EVAPORATOR OVER TEMPERATURE PROTEC-
TION. An evaporator coil sensor monitors coil tempera-
ture during heat and defrost modes. If the coil sensor tem-
perature reaches 38 C (100 F), the controller de-energizes
the heater contactor. If the coil sensor reaches 50 C (122
F), the controller also de-energizes the evaporator fan and
phase select contactors; and generates a shutdown Alarm.
Fault code 09 (Evaporator Coil Over Temperature) is dis-
played on the controller display when the ALARM key is
pressed.
5.
HIGH PRESSURE CUTOUT (HPCO) SWITCH. The
refrigerant high pressure cutout opens, interrupting 24 Vac
control power to the compressor contactor if the compres-
sor discharge pressure rises above 3243 +/- 48 kPa, 32.43
+/- 0.48 bar, 470 +/- 7 psig. This immediately stops the
compressor and evaporator fans. The condenser fan and
phase select outputs remain energized as the controller
operates the condenser fan to correct the condition. The
controller display will show “PAUSE ALM10” for 1 sec-
ond every 10 seconds.
After 5 minutes, the controller attempts to restart the
compressor. If the compressor fails to start, fault code 10
(High Pressure Cutout) is generated. The controller will
restart the compressor when the fault condition corrects
itself (resets). The high pressure switch resets (closes)
when the pressure drops back to 2588 +/- 262 kPa, 25.88
+/- 2.62 bar, 375 +/- 38 psig.
6.
HIGH PRESSURE RELIEF VALVE. A high pressure
relief valve is installed in the liquid line near the receiver
tank. The relief valve protects against excessive pressure
build-up within the refrigeration system from extraordi-
nary and unforeseen circumstances. The valve is a spring-
loaded piston that lifts when refrigerant pressure exceeds
3447 +520/-104 kPa, 34.47 +5.20/-1.04 bar, 500 +75/-15
psig. The valve is located so that refrigerant pressure
expelled from the valve would be directed away from any-
one servicing the unit. The valve will reset when this pres-
sure drops to 2758 kPa, 27.58 bar, 400 psig. The valve is
non-repairable and requires no adjustment. If the valve
fails to reseat properly, recover the refrigerant charge and
replace the valve.
7.
OVERLOAD PROTECTION. The condenser fan motor,
evaporator fan motors and compressor motor include
internal overload protection with automatic reset. If the
compressor motor overload protector opens, the
µ
P-D
controller detects the open motor protector and records
alarm code 50. The controller will attempt to restart the
compressor every 5 minutes.
8.
PHASE SEQUENCE SELECTION. When the On/Off
switch is turned ON, the controller display shows “Phase
Check” while it determines the correct phase sequence.
Phase selection takes 50 to 80 seconds; or more on
extremely noisy power lines. The controller then ener-
gizes phase select contactor ABC or CBA to ensure prop-
er condenser fan, evaporator fan and compressor rotation.
Pretrip Inspection
Visual Inspection
The following visual inspections should be made before the
container is loaded:
1.
Visually check the unit for physical damage.
2.
Check the electrical connections in the unit control box,
making sure they are fastened securely.
3.
Check the conditions of wires and terminals. Repair or
replace if necessary.
4.
Check the refrigeration system for leaks. Inspect for evi-
dence of oil leaks at all joints and connections.
5.
Check the condenser and evaporator coils. Clean if neces-
sary. Use an air or water spray jet directed against the coil
from the air discharge side. Also inspect the condenser
fan grille for damage. If the grille is damaged or missing,
abnormally high head pressure may result. Repair or
replace the grille if necessary.
CAUTION: Air or water spray jet pressure should
not be high enough to damage (bend) coil fins.
6.
Check the mounting bolts on the unit, compressor and fan
motors. Tighten if necessary.
7.
Clean the defrost drains.
8.
Optional: Inspect water-cooled condenser-receiver tank,
water lines and fittings for water leaks. When water lines
are disconnected, also check to be sure that the water
drains completely from the condenser-receiver tank.
Report defective fittings and tanks that do not drain to a
technician.