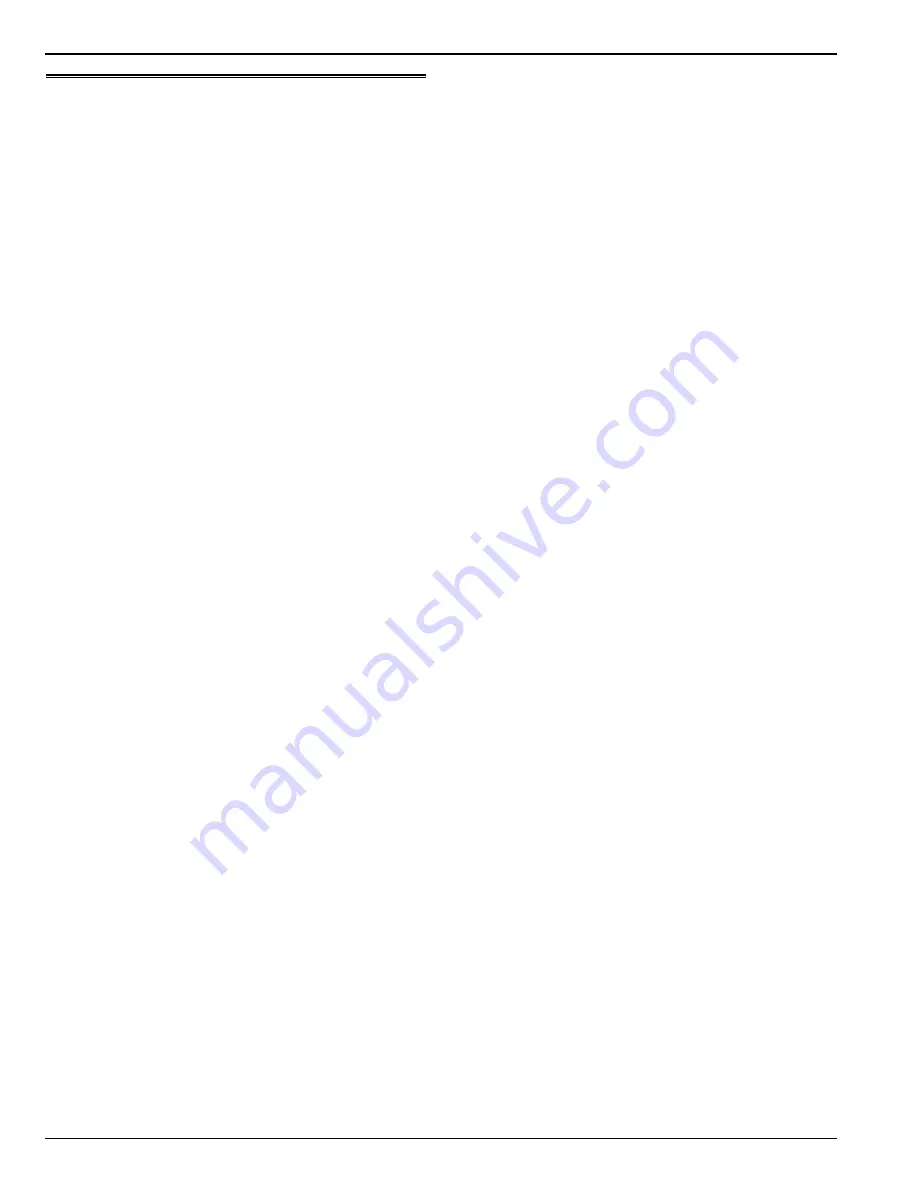
6-6
Piercing Type Service Valves
Refrigeration System Diagnosis and Service
CSR-20 & CSR-40, September 1999
Installing and Removing Piercing Type
Service Valves and a Gauge Manifold Set
To service the refrigeration system on CSR hermetic units,
special piercing type service access valves must be attached to
the discharge and suction line process tubes. These process
tubes are located in the compressor compartment.
When service or maintenance is complete, the hermetic
refrigeration system must be returned to normal. The suction
and discharge line process tubes must be carefully sealed and
the service valves must be removed from the system.
Piercing Type Service Valve Installation
NOTE: Before installing any piercing type service
valve, carefully check to ensure that the valve and
access port connection function properly.
1.
Stop the unit and allow compressor suction and discharge
lines to cool to ambient temperature.
2.
Inspect piercing type service valves for correct fittings for
attachment of gauge manifold hoses, refrigerant recovery
equipment, a vacuum pump and other service tools.
3.
Remove the compressor compartment bracket.
4.
Clean dirt and moisture from the unit’s process tubes.
5.
Position the piercing port of the service valve about 13
mm (0.5 in.) from the existing crimp (or end) of the
process tube on the suction line.
6.
Install and secure the piercing valve on process tube.
Carefully check to ensure that the piercing valve connec-
tion on the process tube is secure.
7.
Leak check the service valve connection with an electron-
ic leak detector.
8.
Repeat steps 5 through 7 to install a piercing type service
valve on the discharge line process tube.
Gauge Manifold Set Installation
NOTE: As long as a slight positive pressure remains
in the manifold set and hoses, the gauge manifold
set may be reinstalled without additional purging.
To purge a gauge manifold set and hoses, see
“Gauge Manifold Valve Positions” in this chapter.
1.
Inspect gauge manifold for proper hose and fitting con-
nections. Both the low side (suction) and high side (dis-
charge) hand valves on the gauge manifold should be fully
closed to center port.
2. Clean dirt and moisture from around ports on piercing
valves. Remove service port caps (if required).
3.
Attach the low side hose (compound gauge) to the pierc-
ing valve port on the suction process tube finger tight.
4.
Attach high side hose (pressure gauge) to the piercing
valve port on the discharge process tube finger tight.
5.
The gauge manifold set is now ready to use to check sys-
tem pressures and perform MOST service procedures.
Gauge Manifold Set Removal
NOTE: To ensure minimum refrigerant release to the
atmosphere, the compressor should be operating.
While this is not possible in all cases, the same pro-
cedure should be followed.
1.
Operate the unit in a cool mode.
2.
Close the refrigerant tank hand valve (if attached to the
gauge manifold set).
3.
Open both manifold hand valves.
4.
Remove the discharge line from the piercing valve port.
5.
Operate the unit in cool mode until the suction pressure
decreases below 385 kPa, 3.85 bar, 50 psig.
6.
Stop the unit.
7.
Remove the suction line from the piercing valve port.
Piercing Type Service Valve Removal
NOTE: Before removing a piercing type service
valve, make sure the unit successfully completes a
controller Pretrip Test to verify that the refrigerant
charge and unit operation are correct.
1.
Carefully crimp the suction line process tube about 13 mm
(0.5 in.) from the service access valve to seal and isolate
suction line process tube from the service valve.
NOTE: Perform the following three procedures
as quickly as possible to prevent refrigerant
loss.
2.
Remove the piercing type service valve from suction
process tube.
3.
Cut the end of process tube off where the tube was pierced
by the service valve. This leaves about 13 mm (0.5 in.) of
process tube open behind the crimp.
4.
Fill the open end process tube with high temperature sol-
der.
5.
Repeat steps 1 through 4 to seal the process tube and
remove the service valve on from the discharge line.
6.
Leak check the process tubes with an electronic leak
detector.