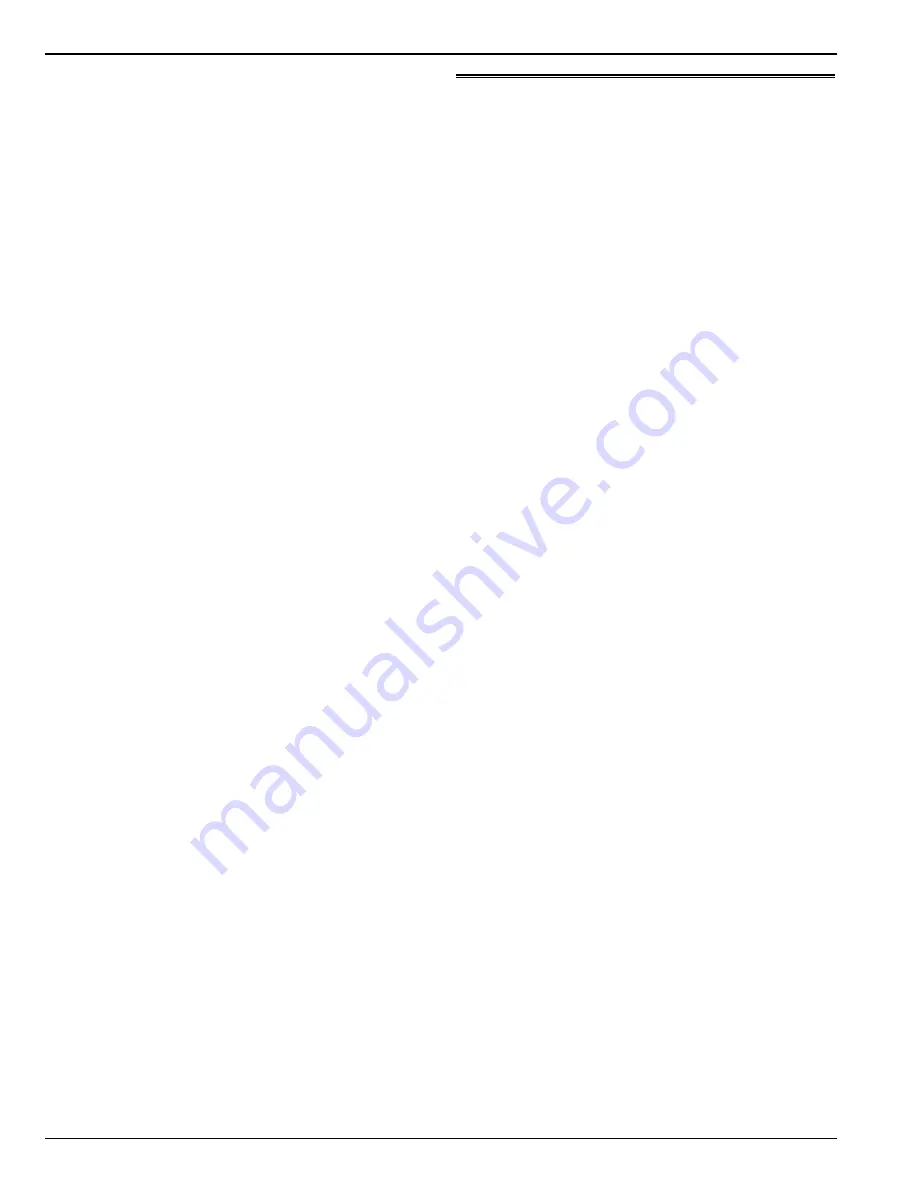
6-10
Refrigerant Recovery
Refrigeration System Diagnosis and Service
CSR-20 & CSR-40, September 1999
Refrigerant Recovery from Hermetic
Refrigeration Systems
Caution: Use only refrigerant recovery equipment
approved for and dedicated to R-404A recovery.
When removing any refrigerant from a Thermo King refrigera-
tion system, use a recovery process that prevents or absolutely
minimizes the refrigerant that can escape to the atmosphere.
Typical service procedures that require removal of refrigerant
from the unit include:
•
To empty the unit of refrigerant when an unknown
amount of charge is in the system and a correct charge is
required.
•
To empty the unit of contaminated refrigerant when the
system has become contaminated. Place this refrigerant
gas in a contaminated refrigerant bottle to be reclaimed
later.
•
To remove a leak test charge from the refrigeration sys-
tem. Because this refrigerant gas will contain some air,
place it in a contaminated refrigerant bottle to be
reclaimed later.
NOTE: Always refer to specific recovery equipment
Operator and Service Manuals.
Vapor Recovery
1.
Disconnect unit from 3-phase power supply.
2.
Install piercing type service access valves on the process
tubes located on the discharge and suction lines in the
compressor compartment. Attach service lines to the ser-
vice access valves and recovery machine and properly
purge the lines.
3.
Set the recovery machine for vapor recovery.
NOTE: CSR Hermetic units do not have service
valves or fittings installed in the refrigeration
system. Therefore, only vapor recovery of the
refrigerant charge is possible.
4.
Turn ON the recovery machine and open (back seat) both
service access valves.
5.
Continue to operate the recovery machine until unit pres-
sures drop to 0 kPa, 0 bar, 0 psig pressure.
CAUTION: Nitrogen (N2 ) is under 15,170 kPa, 151.70
bar, 2200 psig, or greater. Pressure is for full cylin-
der at 21 C (70 F). DO NOT use Oxygen (O2), acety-
lene or any other types of pressurized gas on refrig-
eration systems or any component of a system.
Dehydration, pressure testing, purging and soldering can
be accomplished with the use of dry nitrogen (N2 ). The prop-
er equipment and application of equipment is of greatest
importance.
Procedure
1.
Attach gauge manifold set (refer to “Gauge Manifold Set
Attachment and Purging” for proper procedure for con-
necting to the unit).
2.
Close both hand valves on the gauge manifold (front seat-
ed).
3.
Connect charging hose to a source of nitrogen. Adjust
pressure regulator to the proper pressure for the required
procedure.
4.
Purge system high side to low side.
MAXIMUM Gas Pressure for Service Procedures
• Leak Testing: 1034 to 1200 kPa, 10.34 to 12.00 bar, 150-174 psig,
• Purging/Dehydration: 69 to 138 kPa, 0.69 to 1.38 bar, 10-20 psig,
• Soldering: 35 kPa, 0.35 bar, 5 psig.