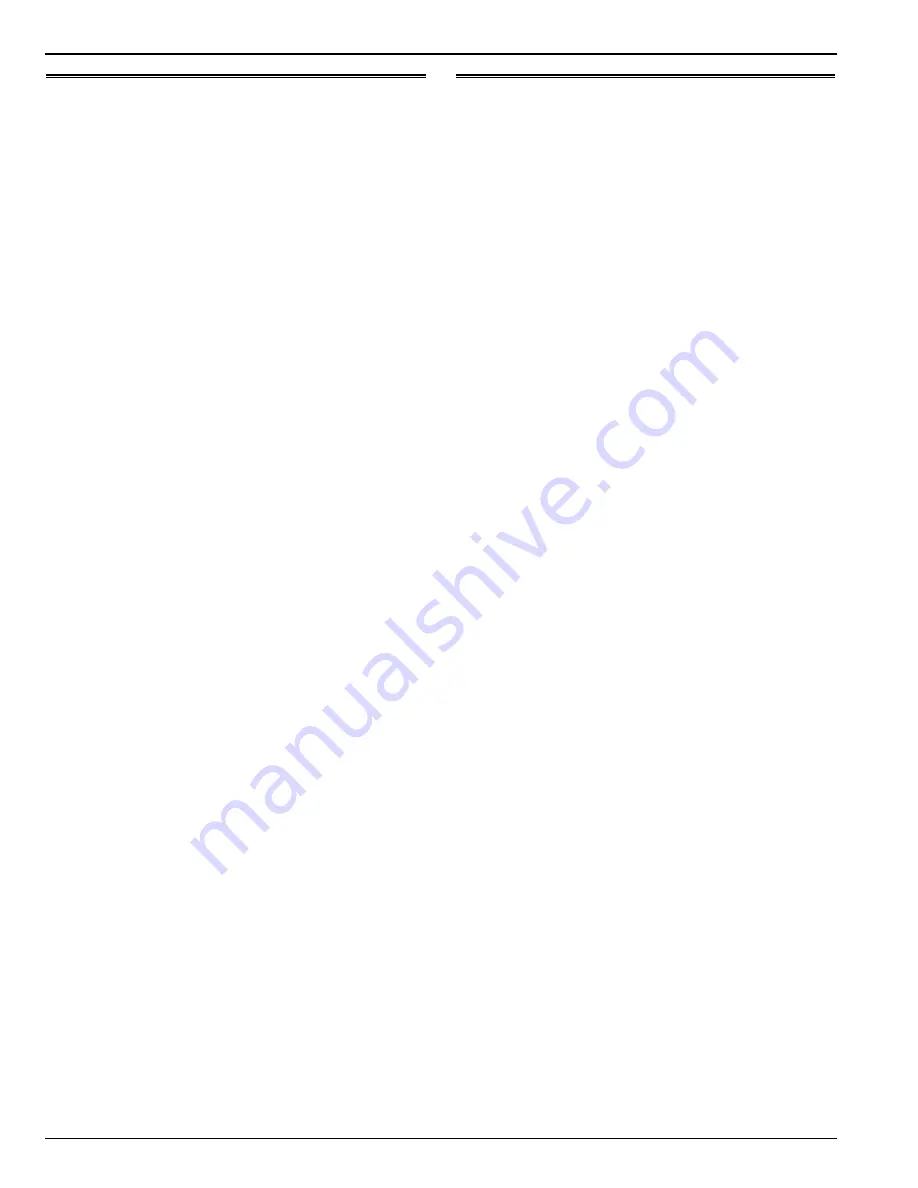
3-2
Unit Instruments
Operating Instructions
CSR-20 & CSR-40, September 1999
Unit Instruments
1.
STATUS INDICATOR LEDs are located on the
µ
P-D
controller and signal the following:
• Cool
• Defrost
• Modulation
• Supply
• Null
• Return
• Heat
• Power Limit
• In-Range
• Alarm
The In-range LED illuminates when the controlling
air sensor temperature is between 1.7 C (3.0 F) above set-
point and 2.5 C (4.5 F) below setpoint. The controller
inhibits the out-of-range alarm during defrost.
NOTE: The controller will not respond to an out-
of-range condition for 75 minutes to avoid nui-
sance alarms.
2.
THERMISTOR LEAD (OPTION). A thermistor lead is
located in the unit control box to provide air temperature
verification. The bulb of the thermistor lead is attached to
the return or supply air sensor in the evaporator section.
3.
REMOTE MONITOR CONNECTOR, 4-PIN (OPTION).
A receptacle is provided on the side of the control box for
connecting the ship’s 4-pin bridge light system to the unit.
The connector provided circuits for Compressor On,
Defrost and In-range. The remote in-range light is activat-
ed when the controlling air sensor temperature is between
1.7 C (3.0 F) above setpoint and 2.5 C (4.5 F) below set-
point.
4.
RECORDING THERMOMETER (OPTION). The
recording thermometer indicates and permanently records
the temperature of the air returning to the evaporator sec-
tion on a calibrated chart.
5.
POWER LINE COMMUNICATIONS MODEM
(OPTION). Several models remote monitoring modems
are available to provide remote monitoring via the power
cable. High speed transmission reads all controller infor-
mation.
• Thermo King modem is installed in a self-enclosed box
bolted above the compressor.
• Sabroe Controls modem is installed in the electrical con-
trol box.
• RTE modem is installed in the electrical control box.
Unit Protection Devices
1.
CIRCUIT BREAKERS. A 25 ampere manual reset circuit
breaker protects the 460/380V power supply circuit to the
unit electric motors and control system transformer. The
main power circuit breaker is located in the control box.
2.
FUSES. A number of fuses located in the power module
protect unit circuits and components.
• A 2 amp fuse (F1) protects the circuit to the modulation
valve.
• A 1 amp fuse (F2) protects the bridge light relay (option)
circuit.
• A 1 amp fuse (F3) is unused.
• A 5 amp fuse (F4) protects the circuit that supplies
power to Power Module Board.
• A 1 amp fuse (F5) protects the bridge light (option) cir-
cuit.
• A 5 amp fuse (F6) protects the IRMU (option) circuit.
• A 3 amp fuse (F7) protects the TRANSFRESH (option)
circuit.
• A 2 amp fuse (F8) protects the IRMU (option) circuit.
• A 3 amp fuse (F9) protects the chart recorder (option)
circuit.
• A 3 amp fuse (F10) protects the battery charger (option)
power input circuit.
• A 7.5 amp fuse (F11) protects the Output Module circuit.
• A 3 amp fuse (F12) protects the battery pack connector
circuit.
• A 3 amp fuse (F13) protects the battery charger (option)
output circuit.
• A 3 amp fuse (F14) protects the battery (option) circuit.
3. COMPRESSOR DISCHARGE GAS TEMPERATURE
SENSOR. A refrigerant injection system uses the com-
pressor discharge temperature to determine when cold
refrigerant will be injected into the center scroll of the
compressor to protect the compressor from excessively
high operating temperatures. At compressor discharge gas
temperature above 138 C (280 F), the controller energizes
the liquid injection valve. When the discharge gas tem-
perature drops to 132 C (270 F), the controller de-ener-
gizes the injection valve to stop refrigerant injection.
If the discharge gas temperature rises above 148 C
(298 F), the controller immediately stops the compressor
and evaporator fans. The condenser fan and phase select
outputs remain energized as the controller operates the
condenser fan to correct the condition. The controller dis-