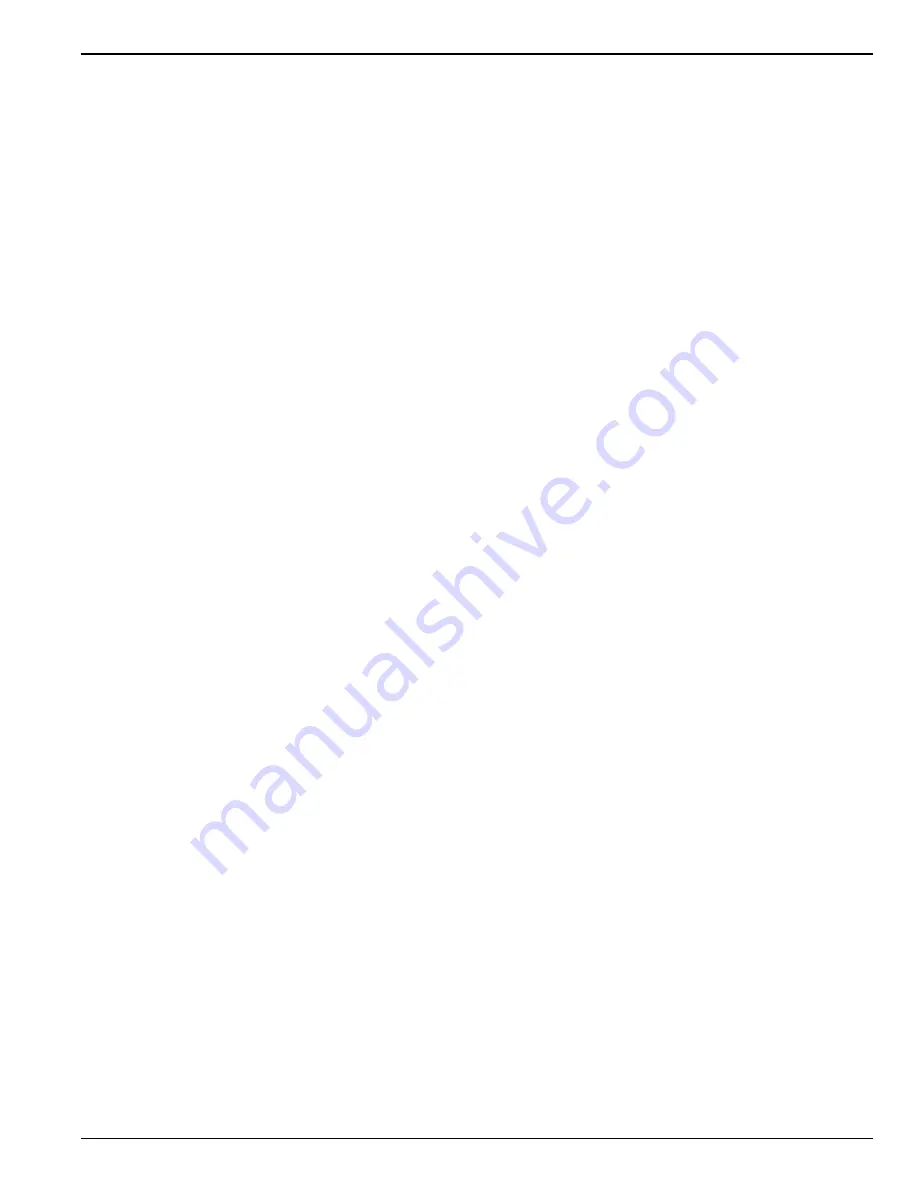
CSR-20 & CSR-40, September 1999
Refrigeration System Diagnosis and Service
Evacuation and Cleanup of System
6-13
4.
Connect the Evacuation Station and refrigerant tank with
gauge manifold (optional) to the unit as indicated on the
diagram on page 6-12. Connect evacuation hoses to the
service access valves on the suction and discharge line
process tubes.
5.
Open Evacuation Station valves (V1, V3, and V4). Open
valve V2 only when a reading on the Micron Meter is
desired. This is especially true when starting to evacuate
a unit and large amounts of moisture and oil will be pass-
ing by the sensor.
6.
Open the vacuum pump Iso-Valve™ built into the pump
housing below the handle. Keep the valve be kept open at
all times.
7.
If connecting a refrigerant tank and gauge manifold to the
evacuation station, close the gauge manifold and refriger-
ant tank valves to prevent refrigerant from being drawn
from the tank.
Unit Evacuation
1.
Turn on the Vacuum Pump. Open the Gas Ballast Valve
located on top of the pump housing behind the handle (the
valve is fully open at two turns counterclockwise).
Evacuate the system to 500 microns to achieve a final
equilibrium pressure of 2000 microns or less. The final
equilibrium pressure is determined with the Thermo King
Evacuation Station using the following procedure (called
a pressure-rise test):
a.
Evacuate the system using the Evacuation Station
until the vacuum level reaches 1000 microns. Then
close the Gas Ballast Valve,
b.
Continue evacuation to 500 microns or until vacuum
stabilizes at its lowest level. Contamination may
delay reaching the lowest level for a period of several
or more hours.
c.
Close valve V1 to isolate the vacuum pump from the
system.
d.
Observe the vacuum level on the Micron Meter.
When the Meter has stabilized, the value indicated on
the Micron Meter is the equilibrium pressure. This read-
ing must be 2000 microns or less.
NOTE: The presence of refrigerant in the com-
pressor oil may prevent a low vacuum reading
from being achieved. Compressor oil can contin-
ue to outgas for long periods of time.
2.
If the vacuum level appears to stall above 500 microns,
back seat the discharge service access valve and observe
the Micron Meter.
•
A drop in pressure indicates that the compressor oil is
out-gassing and further evacuation is necessary.
•
An increase in pressure indicates that a leak exists or
there is moisture in the system. Perform a “Pressure
Rise Test” and evaluate.
3.
Close valve V1 when the desired vacuum level has been
reached.
4.
Wait five minutes and read the Micron Meter.
•
A system that is leak free and dry will remain below
2000 microns for five minutes.
•
A system that rises above 2000 microns but stabilizes
below atmospheric pressure is probably contaminated
with moisture or has refrigerant out-gassing from the
compressor oil. Additional evacuation is required.
•
A system that continues to rise without stabilizing has
a leak and must be repaired.
5.
If the vacuum level remained below 2000 microns for five
minutes, the unit is ready to charge.
Pressure Rise Test
Evacuate the system and close valve V1. With valves V3 and
V4 open, the pump is isolated and the system is held under a
vacuum. If the Micron Meter rises, one of the following con-
ditions exist.
•
Leak: Watch the movement of the Micron Meter
needle. If the needle continues to rise until it reaches
atmospheric pressure, it is an indication that a leak
exists somewhere in the system. When a leak is in a
system, the vacuum will eventually stabilize at atmos-
pheric pressure (see graph, “Constant Pressure Rise
After Evacuation Indicates System Leak”, on page 6-
14).
•
Moisture: When the needle indicates a rise and then
stabilizes at a level below atmospheric pressure, it is
an indication that the system is vacuum tight, but is
still wet and requires additional dehydration and
pumping time (see graph, “Pressure Rise Levels Off
After Evacuation Indicates Moisture in System”, on
page 6-14).