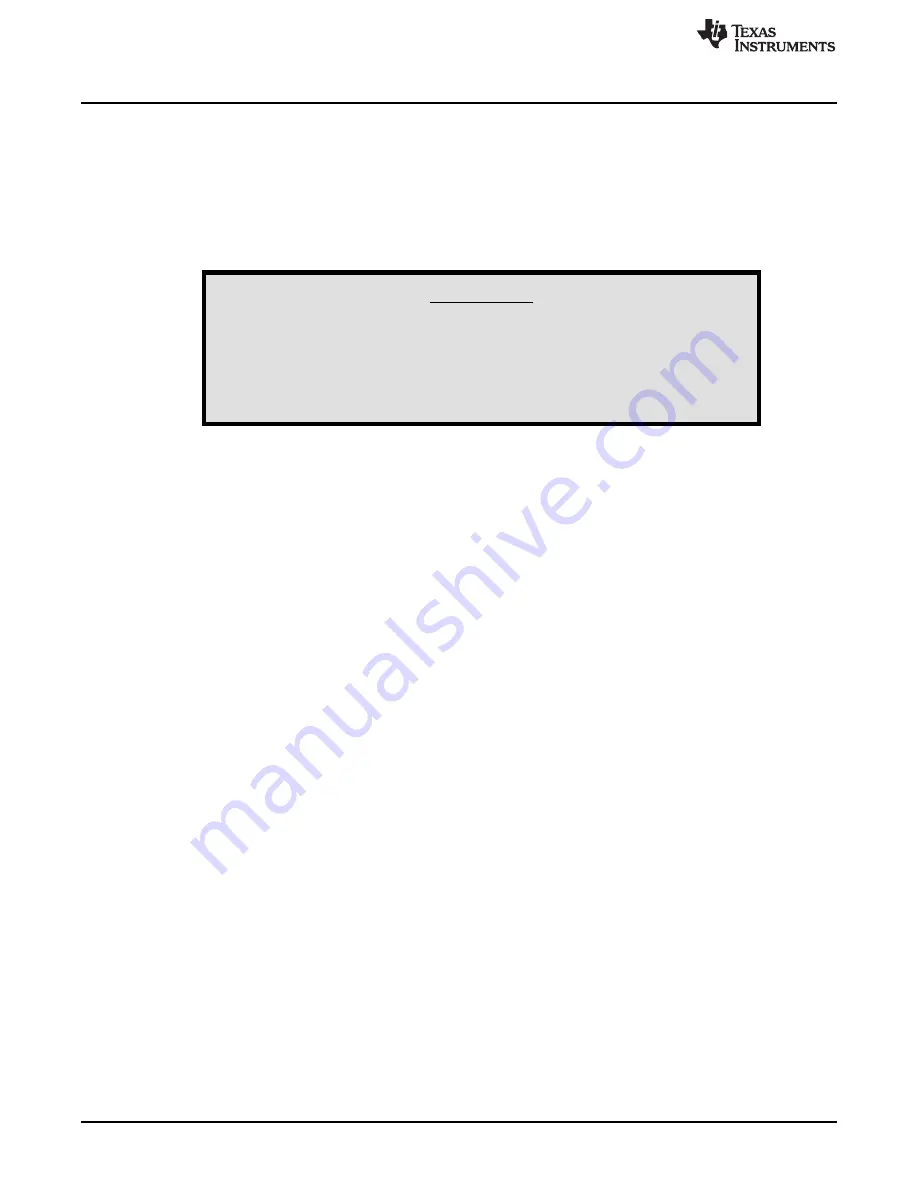
Test Setup and Results
www.ti.com
10
SLLU298 – May 2018
Submit Documentation Feedback
Copyright © 2018, Texas Instruments Incorporated
ISO5852SDW Driving and Protecting SiC and IGBT Power Modules
To minimize risk of electrical shock hazard, always follow all high voltage safety rules and regulations
while operating electrical equipment!
When evaluating ISO5852SDWEVM-017 with EVM attached to its intended vendor provided power
module as part of the system level measurements and assessments, the power module will have
accessibility of high voltage and high temperatures that impact the EVM’s operating conditions as well.
High voltages with transients up to 1500Vpk can appear between isolated areas of the EVM, bounded as
illustrated in
Figure 9
. The externally provided power module also radiates heat that indirectly provides air
flow and convection that can elevate the temperature of EVM board.
WARNING
To minimize risk of fire hazard, it is critical to assure that the
external power module’s electrical and thermal ratings are never
exceeded
as
published
by
the
external
power
module’s
manufacturer’s datasheet, and the maximum temperature of any
external power module should never exceed 130
o
C.
The EVM provides isolated thermal dissipation diagnostic signals available at connector J1 shown in
Figure 9
, which measure high voltage input rail and thermistor temperatures inside the external power
module. Both BUS_P (pin 17) to BUS_N (pin 18) and TRO_P (pin 20) to TRO_N (pin 19) diagnostic
signals must be strictly monitored to assure both high voltage and thermal protective features are being
utilized.
The user is required to provide necessary interface controller hardware to shut down and deenergize the
system immediately if BUS_P to BUS_N signal exceeds 1.85 VDC, or signal TRO_P to TRO_N drops
below 0.135 VDC.
2.2
Equipment
•
Power Supplies
–
At least up to 6-V and 1-A power supply for powering EVM, for example: BK Precision, series 1715
–
At least up to 300-V and 10-mA power source for testing bus isolated sense amplifier within EVM
•
Function Generator and accessories
–
One 2-channel function generator, for example: Tektronix AFG3102
–
Two standard 50-
Ω
BNC coaxial cables
–
Two 50-
Ω
BNC male to female feed-thru terminators, for example: Tektronix 011-0049-02
•
Oscilloscope and accessories
–
Oscilloscope 500-MHz or higher with at least 4 channels, for example: Tektronix DPO7104
–
Four at least 500-MHz bandwidth passive voltage probes, for example: P6139A
•
Six Digital Multi-Meters (DMM), for example Fluke 187
•
Other
–
20-wire flat cable with receptacle 71600-120LF from FCI with opposite end wired to PCB with
related test points
–
Wires 7 to 10 inch long with clips on both ends to make jumpers on some test points
–
Resistance decade box, for example 72-7270 from Tenma
Test procedure includes four main tests with different test setups
1. Power up and bias supply voltages test
2. Input and output pulse switching waveforms test
3. Thermistor isolated amplifier input and output signal test
4. Bus voltage sense isolated amplifier input and output signal test