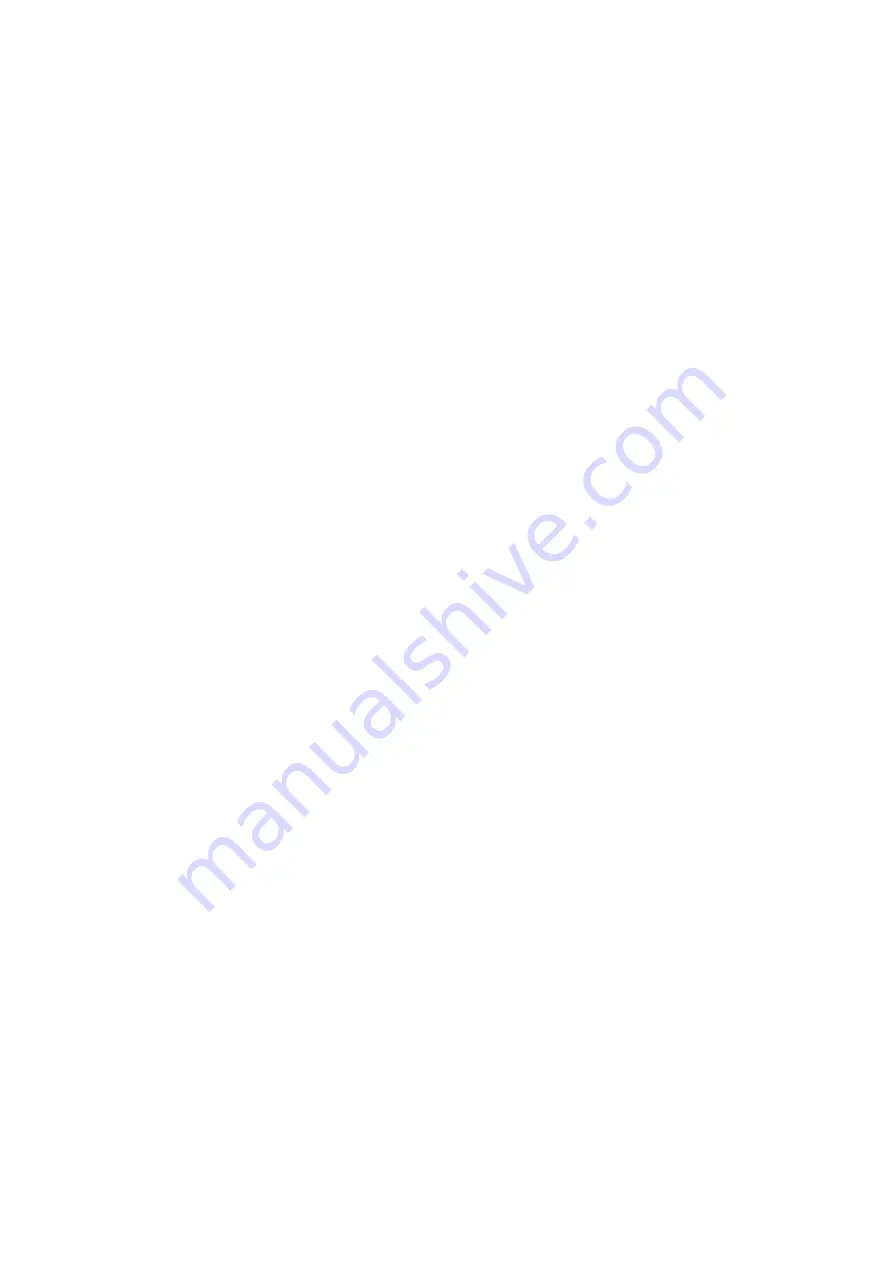
Automatic boiler for wood pellets
36
7.2.4
Annual audit
Every boiler of the KP series should undergo annual audit after the end of the main heating season. This audit is
necessary in order to prevent from possible non-standard conditions in the next year of operation of the
equipment. If the annual audit is not performed as per the below mentioned programme, this may be considered
by the manufacturer to be the reason for rejection of guarantee conditions in the second year of use. At the same
time, the user gets exposed to a risk of any failure which may cause loss of operating certainty or large physical
damage.
Annual audit - due to demanding activities - has to be entrusted to a trained servicing company which will make
record of the audit in the documentation of the boiler.
We proceed as follows during the annual audit:
Turn off the main switch of the control unit
disconnect the boiler from network by pulling the mains cord from the wall socket or by turning the socket
circuit off in the switchboard.
As we will also work inside the boiler, let us the boiler 2 - 3 hours to cool down before we start next work.
After the boiler gets cooled down
we will start dismantling of ceramic parts through the burner door - i.e.:
remove the ceramic shield over the burner door (by gradual moving to the left and
release it then to the bottom right side from the fixation aperture)
remove the ceramic reflector by simple pulling forward
remove all parts of ceramic burning out grate. Lift the back side to a maximum possible hights, front side
lower down and remove the part out.
Now remove all ash buildups by steel brush from ceramic parts.
Note:
Do not forget that it is about one ceramic. Work carrefully so you do not damage all parts.
Cleaning the draughts of combustion products
If there is automatic cleaning installed, there just has to removed a dust above exchanger by a vacuum
cleaner or by forfeiture dust throught pipes of heat exchanger in to a burning chamber.
proceed as follows:
close the burner door so that the boiler does not contaminate the boiler room too much when we will clean
the draughts,
remove lid of the jacketing,
dismantle the lid of the boiler body (4 screws) and place it on the floor. When you mount it back later,
remove slightly ash from it and be careful not to damage insulation during this operation.
now release ash from turbulators and
vacuum dust from the space above exchager
Note:
With advantage we use ash separator and regular vacuum cleaner
Dismantling of the burner
remove the fan from the extension pipe on the flange of the burner,
dismantle the flanged joint (4 screws) from the drive of the spiral-chute Feeder F2, remove the complete
feed screw and place aside. Check it for wear and tear at the same time.
dismantle now the whole burner flange (4 screws) and remove the burner. Clean the whole inside surface
of the burner carefully with a wire brush, mainly in the place of the feeder's outlet and also in all places of
round and slotted nozzles. These places are most susceptible to sedimentation of solid products of burning.
Summary of Contents for KP 12-ES
Page 21: ...Automatic boiler for wood pellets 20 Picture No 15 Jacketing KP 22S KP 22 ES ...
Page 22: ...Automatic boiler for wood pellets 21 Picture No 16 Jacketing KP 62S KP 62 ES ...
Page 43: ...Automatic boiler for wood pellets 42 9 3 1 2Menu users settings ...
Page 45: ...Automatic boiler for wood pellets 44 Cleaning an ash removeing Skin Time window setting ...
Page 48: ...Automatic boiler for wood pellets 47 Actual values Configuration ...
Page 54: ...Automatic boiler for wood pellets 53 Cleaning Ash removing USB Time window setting ...
Page 55: ...Automatic boiler for wood pellets 54 Load from USB Save on USB ...
Page 60: ...Automatic boiler for wood pellets 59 ...
Page 62: ...Automatic boiler for wood pellets 61 ...
Page 63: ...Automatic boiler for wood pellets 62 i ...
Page 70: ...69 Picture No 31 Principle of the modulation ...
Page 72: ...71 Picture No 33 Directory information consuption wood pellets for boiler family KP ...
Page 73: ...72 Picture No 34 Circuit diagram control unit ...
Page 74: ...73 Picture No 35 Circuit diagram modul HZS 533 ...
Page 75: ...74 Picture No 36 Circuit diagram HZS 533 HZS 535 ...