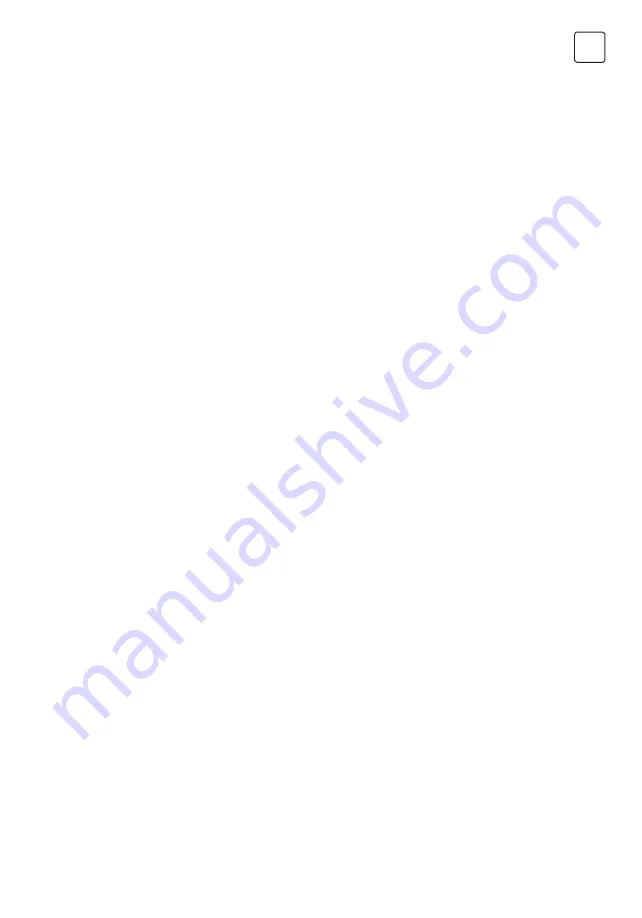
53
ENG
Procedures of Charging Refrigerants
Scrap and Recovery
As a supplement to the general procedure, the following requirements need to be added:
- Make sure that there is no contamination among different refrigerants when using a refrigerant charging device.
The pipeline for charging refrigerants should be as short as possible to reduce the residual of refrigerants in it.
- Storage tanks should remain vertically up.
- Make sure the grounding solutions are already taken before the refrigeration system is charged with refrigerants.
- After finishing the charging (or when it is not yet finished), label the mark on the system.
- Be careful not to overcharge refrigerants.
Scrap
:
Before this procedure, the technical personnel shall be thoroughly familiar with the equipment and all its features,
and make a recommended practice for refrigerant safe recovery. For recycling the refrigerant, shall analyze the
refrigerant and oil samples before operation. Ensure the required power before the test.
1.Be familiar with the equipment and operation.
2.Disconnect power supply.
3.Before carrying out this process, you have to make sure:
• If necessary, mechanical equipment operation should facilitate the operation of the refrigerant tank.
• All personal protective equipment is effective and can be used correctly.
• The whole recovery process should be carried out under the guidance of qualified personnel.
•The recovering of equipment and storage tank should comply with the relevant national standards.
4. lf possible, the refrigerating system should be vacuumized.
5. If the vacuum state can’t be reached, you should extract the refrigerant in each part of the system from many
places.
6. Before the start of the recovery, you should ensure that the capacity of the storage tank is sufficient.
7. Start and operate the recovery equipment according to the manufacturer’s instructions.
8. Don’t fill the tank to its full capacity (the liquid injection volume does not exceed 80% of the tank volume).
9. Even the duration is short, it must not exceed the maximum working pressure of the tank.
10. After the completion of the tank filling and the end of the operation process, you should make sure that the
tanks and equipment should be removed quickly and all closing valves in the equipment are closed.
11. The recovered refrigerants are not allowed to be injected into another system before being purified and tested.
Note
: The identification should be made after the appliance is scrapped and refrigerants are evacuated. The
identification should contain the date and endorsement. Make sure the identification on the appliance can reflect
the flammable refrigerants contained in this appliance.
Recovery
:
1. The clearance of refrigerants in the system is required when repairing or scrapping the appliance. It is
recommended to completely remove the refrigerant.
2. Only a special refrigerant tank can be used when loading the refrigerant into the storage tank. Make sure the
capacity of the tank is appropriate to the refrigerant injection quantity in the entire system. All tanks intended to
be used for the recovery of refrigerants should have a refrigerant identification (i.e. refrigerant recovery tank).
Storage tanks should be equipped with pressure relief valves and globe valves and they should be in a good
condition. If possible, empty tanks should be evacuated and maintained at room temperature before use.
3. The recovery equipment should be kept in a good working condition and equipped with equipment operating
instructions for easy access. The equipment should be suitable for the recovery of R32 refrigerants. Besides,
there should be a qualified weighting apparatus which can be normally used. The hose should be linked with
detachable connection joint of zero leakage rate and be kept in a good condition. Before using the recovery
equipment, check if it is in a good condition and if it gets perfect maintenance. Check if II electrical components
are sealed to prevent the leakage of the refrigerant and the fire caused by it. If you have any question, please
consult the manufacturer.
4. Through blowing process, the system is charged into the anaerobic nitrogen to reach the working pressure
under the vacuum state, then the oxygen free nitrogen is emitted to the atmosphere, and in the end, vacuumize
the system. Repeat this process until all refrigerants in the system is cleared. After the final charging of the
anaerobic nitrogen, discharge the gas into the atmosphere pressure, and then the system can be welded. This
operation is necessary for welding the pipeline.
Summary of Contents for TA22FFML-07410A
Page 59: ......
Page 60: ...www tesla info ...