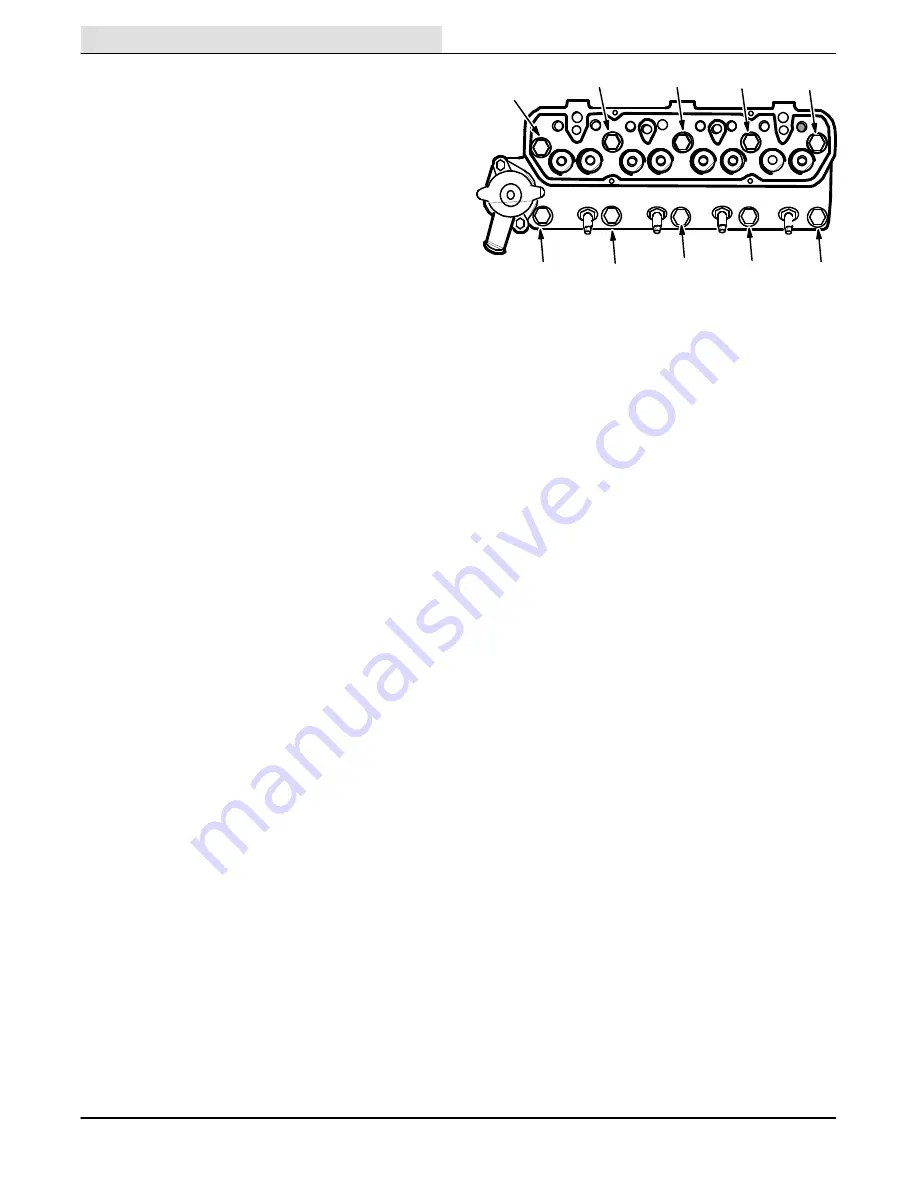
MAINTENANCE
3-32
275 SERIES II MM190 (12---89)
7. Unplug the vacuum line and connect it to the
distributor vacuum advance unit. Start the
engine and accelerate it to approximately 2000
rpm. Note the engine speed when the advance
begins and the total amount of advance.
Advance of the ignition timing should begin
sooner and advance farther than when
checking the centrifugal advance alone. Stop
the engine.
8. If the vacuum advance is not functioning
properly, remove the distributor and check it on
a distributor tester.
9. After adjusting timing, be sure to increase the
engine idle speed to its normal setting.
ENGINE IGNITION TIMING (For machines serial
number 006500 and above)
The ignition system does not require any mechanical
external adjustments, however the spark plug high
tension leads must be inserted correctly, if ever
removed, at each numbered coil position to the
corresponding spark plug number in the cylinder
(front to rear #1, 2, 3, and 4).
The ESC module controls the timing position in the
start mode at 10
_
BTDC until the rpm reaches
250 rpm, thereafter the sensors are processed and
timing is set to be compatible with engine speed,
crankshaft position, engine load, engine coolant
temperature and overspeed by the module.
CYLINDER HEAD -- GASOLINE, LPG
CYLINDER HEAD
A three-stage torque procedure should be used
when reassembling the cylinder head. The cylinder
head bolts must be tightened after the first
50 hours of operation, for machines below serial
number 006500 and seasonally thereafter for all
gasoline and LPG machines.
Snug down cylinder head bolts in the proper
sequence; first to 7 to 11 ft lb (10 to 15 Nm), then to
30 to 37 ft lb (40 to 50 Nm), then to 60 to 66 ft lb (80
to 90 Nm), and then after ten to fifteen minutes
torque to 74 to 81 ft lb (100 to
110 Nm).
Tighten the intake manifold bolts to 15 to 18 ft lb (20
to 24 Nm) after every 800 hours of operation.
1
2
3
4
5
6
7
8
9
10
03532
CYLINDER HEAD BOLT TIGHTENING SEQUENCE
The cylinder head bolts must be retorqued after the
engine is put into operation and brought up to
proper operating temperatures. To retorque head
bolts, follow the correct sequence. Loosen one head
bolt at a time one-quarter turn, 90 degrees; then
retorque it to the correct value.
NOTE: Power wrench torque limit must be held at
least 10 ft lb (14 Nm) below hand torque
specification; then hand torque to the specifications.
VALVE TAPPET CLEARANCE
The valve tappet clearance must be checked and
adjusted if necessary after every 400 hours of
operation.
To set the valve clearance without the engine
operating, rotate the crankshaft until No. 1 cylinder is
at the top of the compression stroke. Check the
timing marks. It should read 0 or TDC. Both valves
on No. 1 cylinder are now closed. Set the valve
clearance on both valves. Next, rotate the crankshaft
180
_
, and set the valve lash on both valves on No. 2
cylinder. Again rotate the crankshaft 180
_
, and set
the valve lash on both valves on No. 4 cylinder.
Rotate the crankshaft another 180
_
, and set the
valve lash on both valves on No. 3 cylinder.
Check and adjust, for machines below serial number
006500, the intake valve clearance from 0.009 in
(0.22 mm), and the exhaust valve clearance from
0.023 in (0.59 mm) while the engine is cold.
Check and adjust, for machines serial number
006500 and above, the intake valve clearance from
0.009 in (0.22 mm), and the exhaust valve clearance
from 0.013 in (0.32 mm) while the engine is cold.
Summary of Contents for 275 Series II
Page 1: ...r 275 Series II Sweeper Scrubber ...
Page 6: ...ABOUT THIS MANUAL 275 SERIES II MM190 12 89 d ...
Page 18: ...SPECIFICATIONS 1 2 275 SERIES II MM190 12 89 ...
Page 22: ...SPECIFICATIONS 1 6 275 SERIES II MM190 12 89 ...
Page 24: ...OPERATION 275 SERIES II MM190 12 89 2 2 ...
Page 74: ...MAINTENANCE 3 14 275 SERIES II MM190 12 89 04644 HYDRAULIC SCHEMATIC LOW DUMP MODEL ...
Page 75: ...MAINTENANCE 3 15 275 SERIES II MM190 12 89 04645 HYDRAULIC SCHEMATIC MULTI LEVEL DUMP MODEL ...
Page 97: ...MAINTENANCE 3 37 275 SERIES II MM190 12 89 04643 ELECTRICAL SCHEMATIC DIESEL ...
Page 98: ...MAINTENANCE 3 38 275 SERIES II MM190 12 89 04642 ELECTRICAL SCHEMATIC ACCESSORIES ...
Page 99: ...MAINTENANCE 3 39 275 SERIES II MM190 6 90 06187 ELECTRICAL SCHEMATIC AUTO SHAKER RFS ...
Page 100: ...MAINTENANCE 3 40 275 SERIES II MM190 6 90 06187 ELECTRICAL SCHEMATIC AUTO SHAKER RFS ...