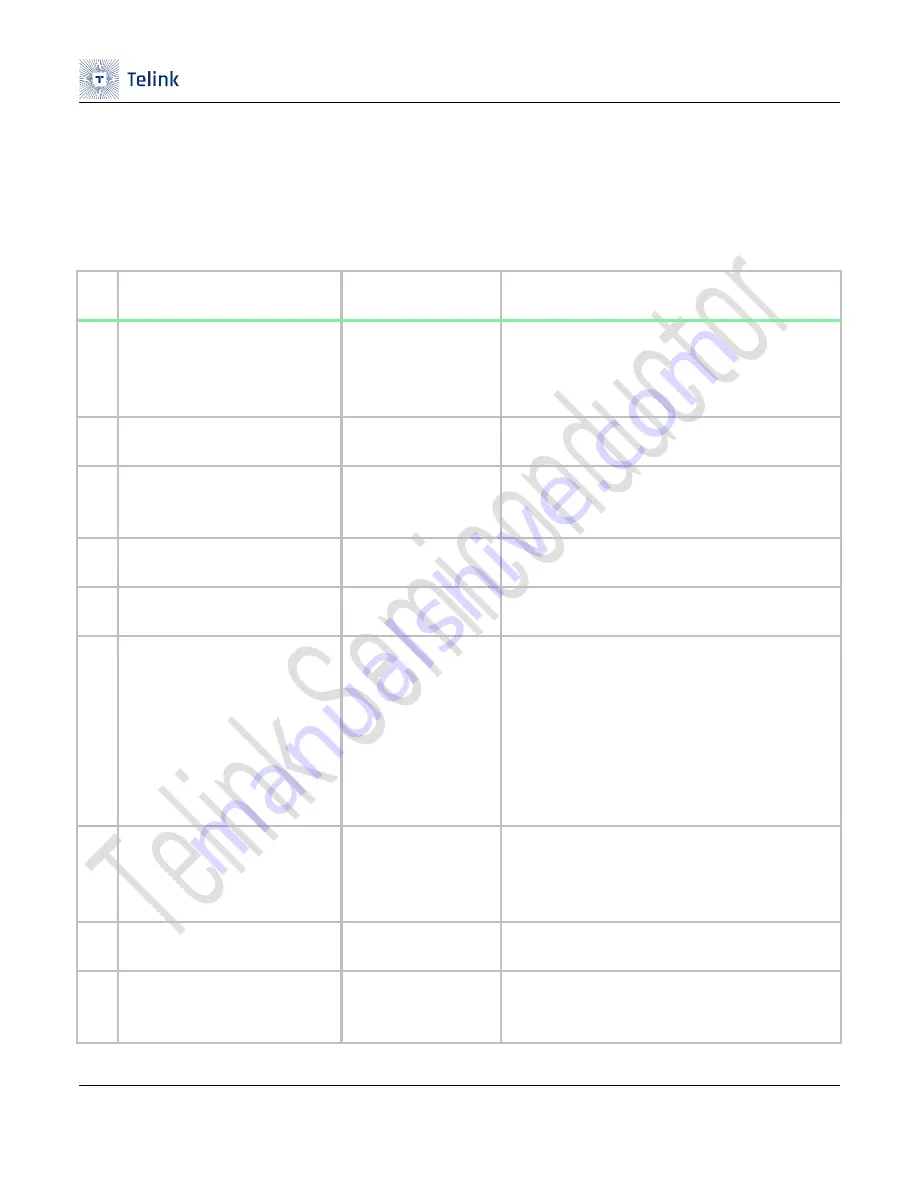
Telink FR1 PCB Design Guideline
AN-22051900-E1 Ver. 1.0.0
11
3.2
Carbon film routing
Carbon film routing is generally 1mm width routing, and the process of carbon film via hole is shown in the
table below.
Table 3-1 Design of carbon film via hole
No.
Item
Requirement and
description
Process limit capabilities, which can lead to
reduced yields or increased production difficulties
109 Carbon grouting board
Preferred FR1
thickness 1.6mm board
When using 1.2mm or 1.0mm thickness for card
type remote control, it is recommended to use
CEM-1 board to ensure the strength and avoid
board warping.
110
Drilling diameter of carbon
grouting hole
0.7mm
111
Diameter of copper plate for
carbon grouting hole
1.4mm
Copper plates at least 0.35mm larger than the hole
on one side, design as 15mm or 1.6mm if there is
enough space.
112
Diameter of weld-resistant
openings
1.3mm
Copper plate with green oil on one side 0.05mm
113 Diameter of insulated opening
1.6mm
0.1mm greater than copper plate on one side when
insulated
114
Diameter of the carbon film on
the surface of the grouting hole
1.8mm
When there is no protective oil, in principle the
carbon film is required to be 0.2mm larger on one
side of the copper plate to avoid revealing copper.
When it is not possible to meet the carbon film
single-side is 0.2mm larger than copper, set the
carbon film and copper have the same width or
single-side is 0.05mm larger, but in this case we
need to print protective oil.
115
Diameter of the carbon film on
the skimmer surface
1.8mm
Minimum 1.6mm; when there is no protective oil,
in principle, it requires that one side carbon film is
0.3mm larger than copper plate to avoid revealing
copper
116
Diameter of carbon hole
protection oil
2.3mm
Minimum 2.0mm, one side is larger than copper
0.2mm at least
117
Width of back carbon grouting
hole edge from carbon bridge
edge
≥
2.3mm
Optimum 2.5 mm. The back carbon coverage width
is at least 2.1 mm due to oil spillage of 0.65 mm on
one side of the hole.