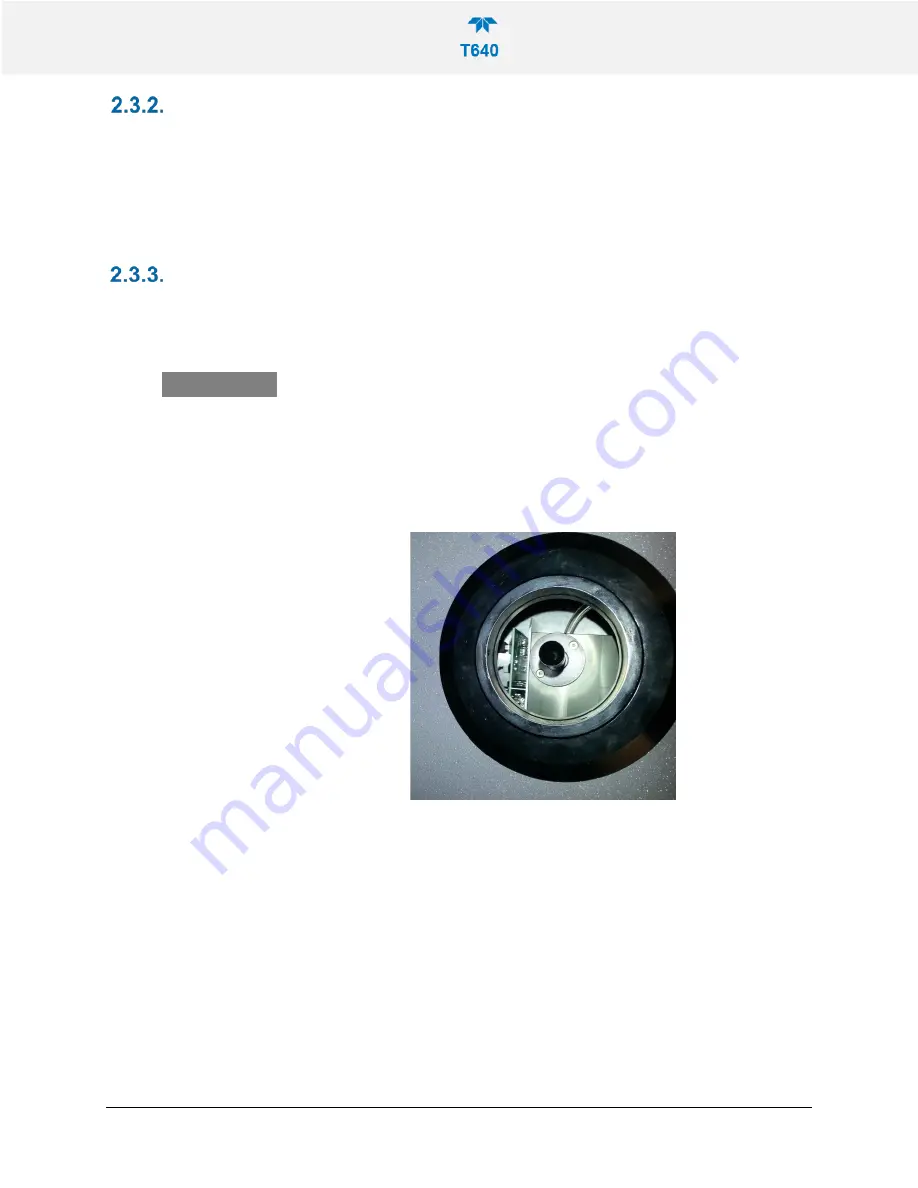
08354B DCN7877
Teledyne API T640 PM Mass Monitor
21
COMMUNICATIONS INTERFACE CONNECTIONS
For network or Internet communication with the instrument, connect an Ethernet
cable from the analyzer’s rear panel Ethernet interface connector to an Ethernet
port. Although the analyzer is shipped with DHCP enabled by default, it should be
manually assigned a static IP address. See Section 3.2.13. The USB ports are for
other utilities described later in this manual.
AEROSOL SAMPLE CONDITIONER (ASC) CONNECTIONS AND
INSTALLATION
The ASC requires an inlet nozzle adapter for installation.
IMPORTANT
IMPACT ON READINGS OR DATA
The black inlet nozzle to the optical sensor is specific to the
instrument and is not interchangeable with other T640
instruments. Use caution when handling and contact TAPI Tech
Support if this piece is ever damaged as it could affect the
instrument’s performance.
Figure 2-7. Top View of Inlet Nozzle
Summary of Contents for T640
Page 2: ......