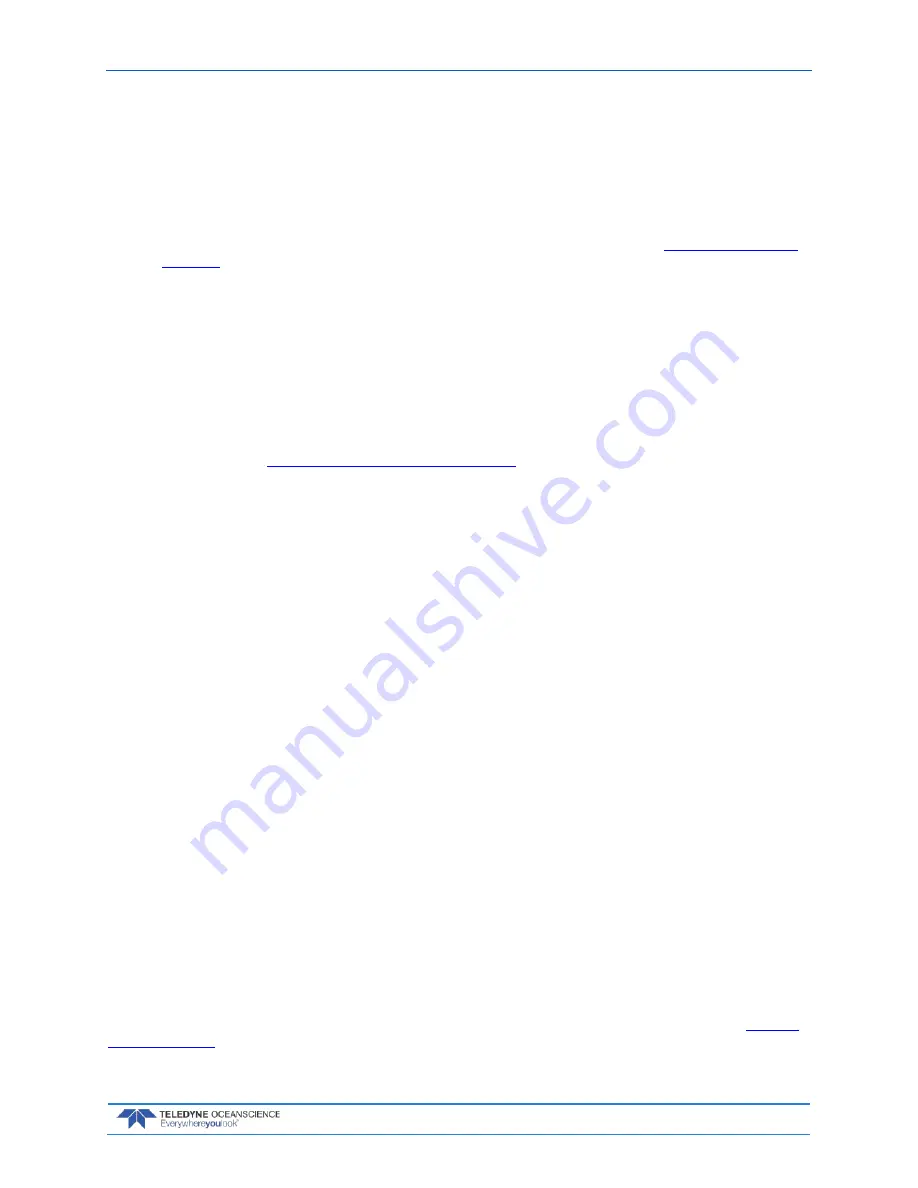
rapidCAST User’s Guide
March 2018
EAR-Controlled Technology Subject to Restrictions Contained on the Cover Page.
Page
17
Software Architecture
RapidCAST encompasses 2 types of software: RapidCAST Motion and RapidCAST Interface.
•
RapidCAST Motion is firmware that resides inside the Control Module, responsible for real-time
motion control and winch operation. It exposes a text-based interface that allows the winch to be
controlled via string messages. Due to the large number of messages required, however, users do
not interact directly with RapidCAST Motion. When new functionality is introduced through fu-
ture software releases, RapidCAST Motion can be upgraded in the field (see
Updating the Winch
Software
).
•
RapidCAST Interface is a graphical user interface that runs on a PC and is the primary method for
operating the winch. It functions as a messaging and task management layer that transmits com-
mands to RapidCAST Motion, hiding the latter’s complexity behind a friendly and intuitive graph-
ical interface.
As needs arise, Teledyne Oceanscience may modify or upgrade either software independently of the other.
Because of their message-based infrastructure, RapidCAST Motion and RapidCAST Interface must have
the same Compatibility Group to ensure proper function. A Compatibility Group is simply a number that
identifies whether a particular version of RapidCAST Motion or RapidCAST Interface are “speaking the
same language” and are therefore fully compatible.
The About window (see
Using the GUI Windows and Controls
) identifies the software versions on the
Control Module and on the PC, as well as their respective Compatibility Groups. If there is a mismatch,
the About menu item will be red. If there is a compatibility mismatch, the system should not be
operated, and the software needs to be upgraded or downgraded until their Compatibility
Groups match.
A Tour of the RapidCAST Interface
The Dashboard is the top panel and gives the operator a snapshot of the winch’s health and current state.
Important information such as the spool’s speed and rotation direction, the power-supply voltage, and
brake status are reported here. The Dashboard keeps the user informed of the system’s critical operating
parameters.
The Task Bar is the second section. It reports the winch’s current assigned task and provides a progress
estimate.
The bottom panel is the Tab Group, which is a collection of tabbed windows grouped according to com-
mon functionality. The Tabs are organized as follows:
•
Deployment: Allows the user to set deployment depth, as well as monitor and control an auto-
mated deployment.
•
Dive Table: Identifies the dive table used to calculate the Tension-Controlled Payout duration
from a target depth. Allows the user to define the polynomial coefficients of additional dive tables
and switch between them.
•
Jog and Teach: Allows the user to jog (move) the winch as well as define positions.
•
Winch Config: Allows the user to modify advanced operating parameters.
•
Maintenance: Contains a grouping of varied tasks associated with system maintenance and atypi-
cal activities such as software updates and health logging.
A Gauge Cluster on the left provides a graphical representation of the Tension Arm position as well as the
spool’s speed and rotation direction. When the Tension Arm is at its lowest position, the angular gauge in
the Interface Software should show the Tension Arm pointing at the far edge of the red zone. If the Ten-
sion Arm is not depicted at this position when the arm is fully relaxed, calibration is needed (see
Tension
Arm Calibration
).