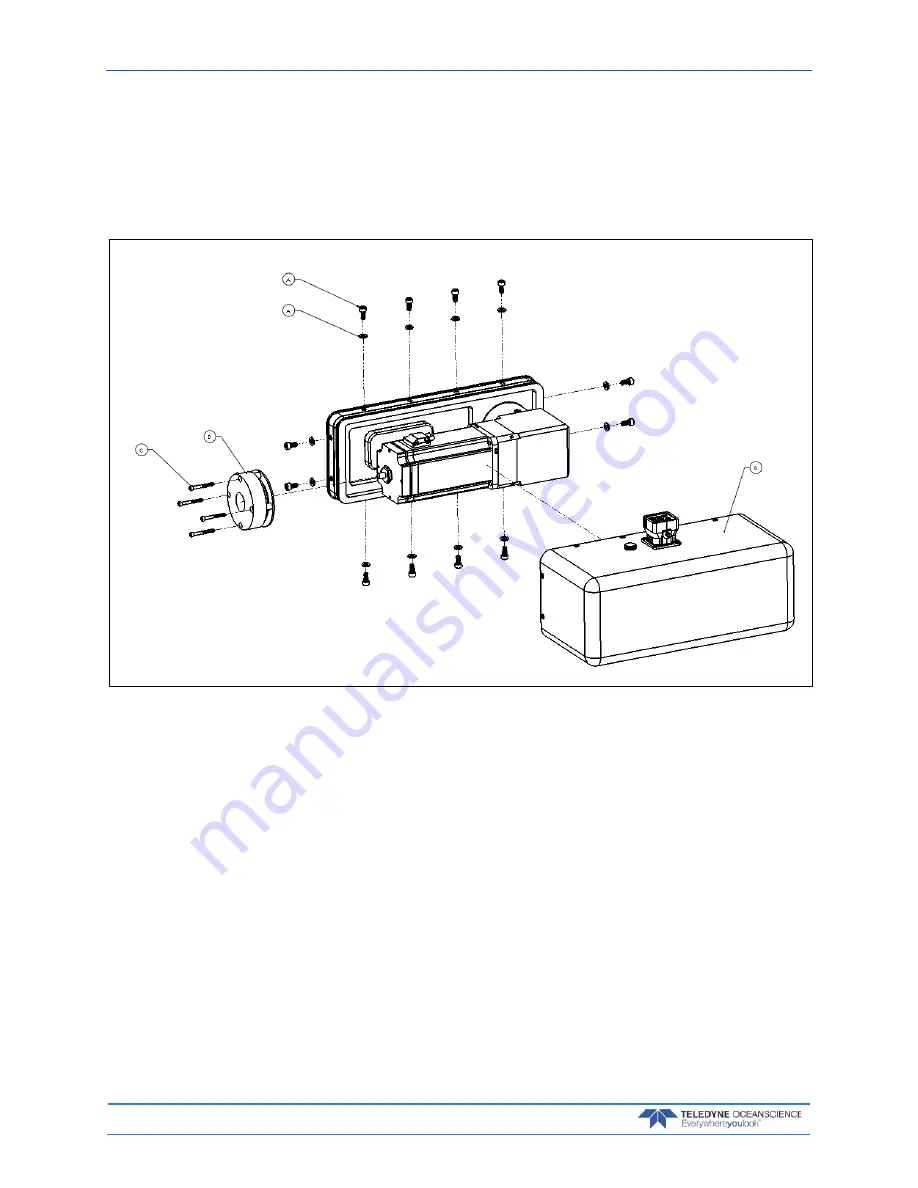
March 2018
rapidCAST User’s Guide
Page
66
EAR-Controlled Technology Subject to Restrictions Contained on the Cover Page.
6. Remove the Brake:
a.
Remove the twelve (12) X M6 screws and washers using a 5mm hex key.
b.
Slide off the motor cover making sure the motor wires are no longer attached.
c.
Remove the four (4) X #8-32 screws using a 9/64 hex key.
d.
Slide off the brake.
7. Now that the brake has been removed, the spool is free to rotate, but it is still secured.
8. Recovery by hand is possible by rotating the spool IN manually.
9. Recovery using a power drill connected to the motor rear shaft is recommended if one is available.
The motor is connected to the spool through a reduction gearbox, which provides increased out-
put torque and reduced output speed. The rotational speed of the spool will be less than the input
rotational speed of the drill.
a.
In general, the drill chuck can be coupled directly to the shaft in the rear of the motor. Be
sure the chuck and motor shaft are clean and free from grease.
b.
For maximum torque, a 7/8inch deep socket can be connected to the brake nut on the mo-
tor shaft. This will eliminate slippage of the drill chuck on the shaft, but may damage
the brake nut and hinder further operations with the system.
c.
As you rotate the motor shaft using the drill, slowly release the spool to make sure the drill
has adequate torque to pull in the line.
d.
STOP if the drill is unable to rotate the spool or if anything is abnormal. Inspect the setup
and try again if possible.
e.
In case recovery with a drill is not possible, disconnect the drill and recover the probe by
hand, rotating the spool IN manually.