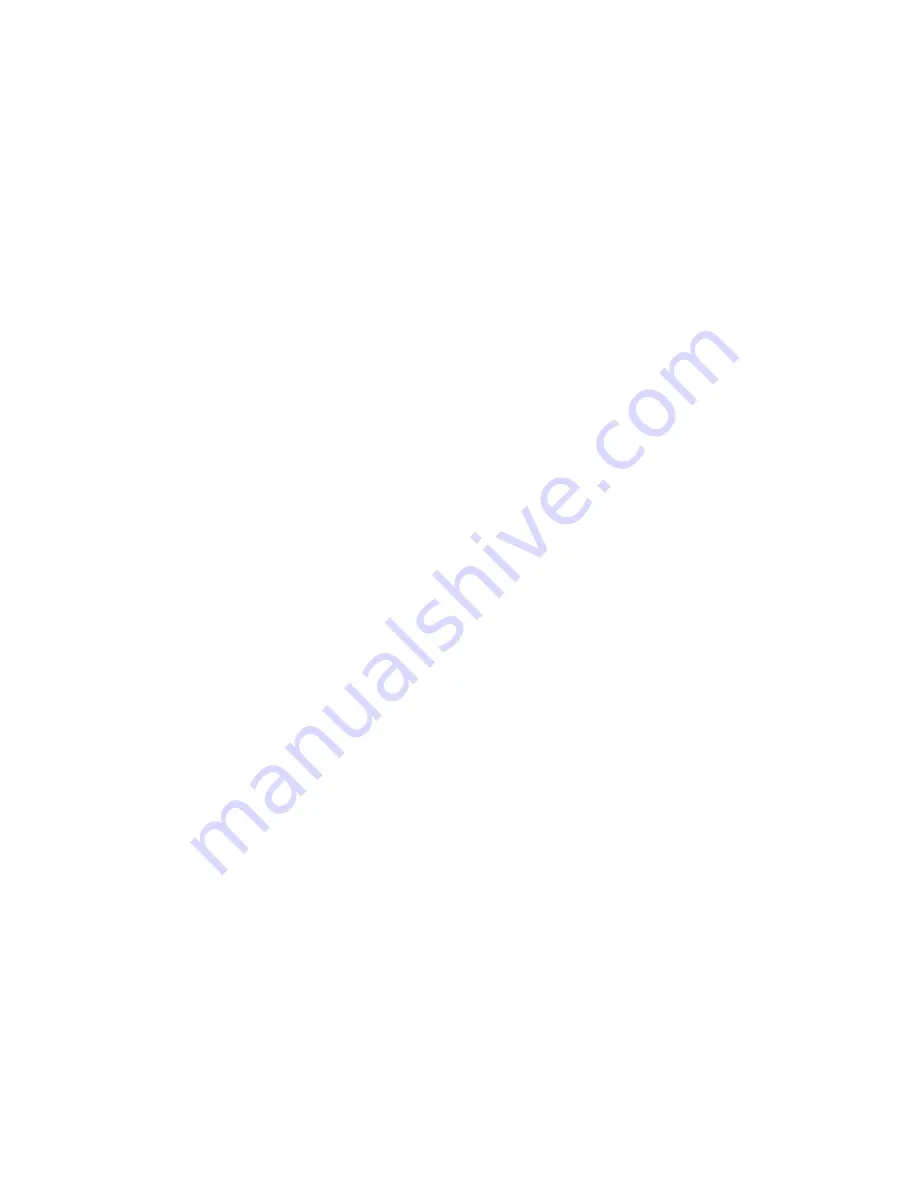
Service Manual
xv
Tables
Table 1-1
Transfer roll core sensor combinations 1-6
Table 1-2
Tray switch sensor combinations (main engine feeder) 1-7
Table 1-3
Tray switch sensor combinations (Lower Tray Assembly) 1-7
Table 1-4
Phaser 440 rear panel DIP Switches 1-9
Table 1-5
Service mode error code summary 1-11
Table 1-6
Physical dimensions 1-12
Table 1-7
Printer clearances 1-12
Table 1-8
Functional specifications 1-13
Table 1-9
Electrical specifications 1-14
Table 1-10
Environmental specifications 1-15
Table 2-1
Configuration page settings 2-13
Table 2-2
Values for modifying the DEVPARAMS.PS file 2-27
Table 6-1
Motor and solenoid resistances 6-8
Table 6-2
Decoding the front panel display 6-18
Table 6-3
Print engine error codes and their meanings 6-19
Table 6-4
Power problems 6-24
Table 6-5
Front panel indicators and their meanings 6-24
Table 6-6
Macintosh printing problems 6-25
Table 6-7
PC DOS printing problems 6-26
Table 6-8
Windows printing problems 6-28
Table 6-9
Workstation printing problems 6-29
Table 9-1
Selecting self-test print patterns 9-3
Table 9-2
Self-check mode summary 9-4
Table 9-3
Top loss adjust settings 9-8
Table 9-4
Top margin adjust settings 9-10
Table 9-5
Mechanical and interrupt switch check summary 9-13
Table 9-6
Setting thermal head temperature (based on thermal head resistance) 9-17
Table A-1
FRU exterior parts list
A-2
Table A-2
FRU interior parts list
A-4