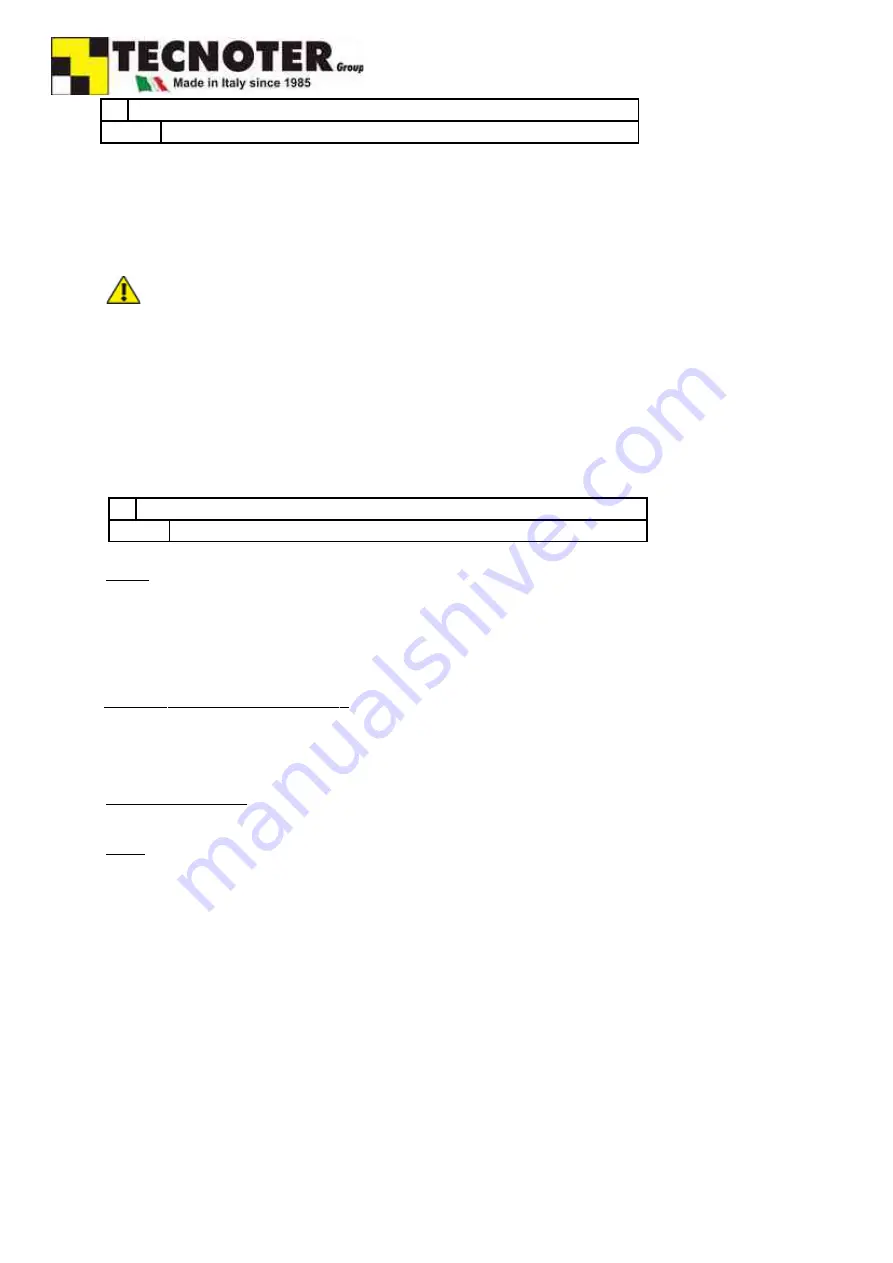
6
MAINTENANCE
6.2
PRECAUTIONS
DANGER! ENERGY NOT DEPLETED IN THE MAGNET!
No intervention can be made on the hydraulic magnet until 20 minutes have passed since the last activation/
operation.
DANGER! ENERGY NOT DEPLETED IN THE MAGNET!
No person, even the most skilled, can touch the hydraulic magnet until 20 minutes have passed since the last activation/operation.
ATTENTION
Check the good working order of the main mechanical components of the hydraulic magnet at the start of the
shift.
When performing maintenance or repairs, it is good practice to apply the following recommendations:
1. Before starting any work, affix a sign stating “undergoing maintenance" in a visible position;
2. At the end of the job, restore and correctly fix all guards that have been removed or opened.
3. The controls and the relative maintenance operations of components and the plant must be performed with the hydraulic power isolated.
4. The adjustment, lubrication, cleaning, replacement of worn parts, controls and repairs must be performed with the machine at a standstill and in
safe conditions.
5. Maintenance personnel must use suitable PPE and wear work clothing.
6. Where possible, guards and safety devices must not be removed. If this takes place, they must be restored as soon as the reasons for which they
have been removed temporarily have been resolved and before commissioning of the machine.
7. Maintenance interventions are prohibited on moving parts.
6
MAINTENANCE
6.3
PERIODIC MAINTENANCE
During maintenance, check the following parts in particular:
Po
l e t i ps
Pole tips are the parts of the magnet that are in direct contact with the material to handle; for this reason they are subject to wear. Periodic inspection
allows to identify potential situations of danger or poor efficiency. Check the pole tips to identify:
Presence of air gaps between pole tip and polarity of the magnet, which causes a reduction of the magnet's capacity.
Presence of cracks on the connection welding, which weaken the mechanical structure and can cause the sudden detachment of the
pole tip from the body of the magnet.
Mechanical wear: present especially when the magnet is intended for handling highly abrasive materials. It must be verified that the wear
is not such to affect the welding between bottom cover and pole tips. Excessive wear also leads to a substantial reduction of the contact surface
with consequent reduction of the magnet's capacity.
L o w
e r c l o sur
e w
i t h
an
t i - w
e a r n o n-ma
g n et
ic
s t e e l
in many cases it comes into direct contact with the material to be handled, therefore it is subjected to the same problems as the pole
tips. Check it periodically in order to identify the eventual presence of:
cracks or splits in the connection welding with the casing that allows the passage of humidity towards the winding, causing damage to
earth.
dents or large deformations: as the winding could be in direct contact with the internal surface of the lid, any deformation could
damage it or break the insulation layer.
C h a i n s
an
d
sus
p e ns
ion
b o l t s
Periodically check the chains, the suspension bolts and all attachment points. Check that the connection welding of the bolts with the lid has no cracks.
It is prohibited to weld a chain component, because the welding may affect the quality of the steel and cause breakage.
S t o ra
ge
To prevent the penetration of humidity through damaged welding or defects in sealing of the gaskets, it is advised not to place the magnet in contact
with the ground when not in use.
1. The hydraulic magnet does not require any lubrication!! There are no greasing points!!
2. It is prohibited to wash the hydraulic magnet with pressurised or non-pressurised jets of water.
3.
The hydraulic magnet can only be cleaned manually using a damp cloth.
Division: Tecnoter srl
Hyd. Magnet
LQMI
Ver. T
Page 29/38
Rev: 1.0a_En –
15/07/2018