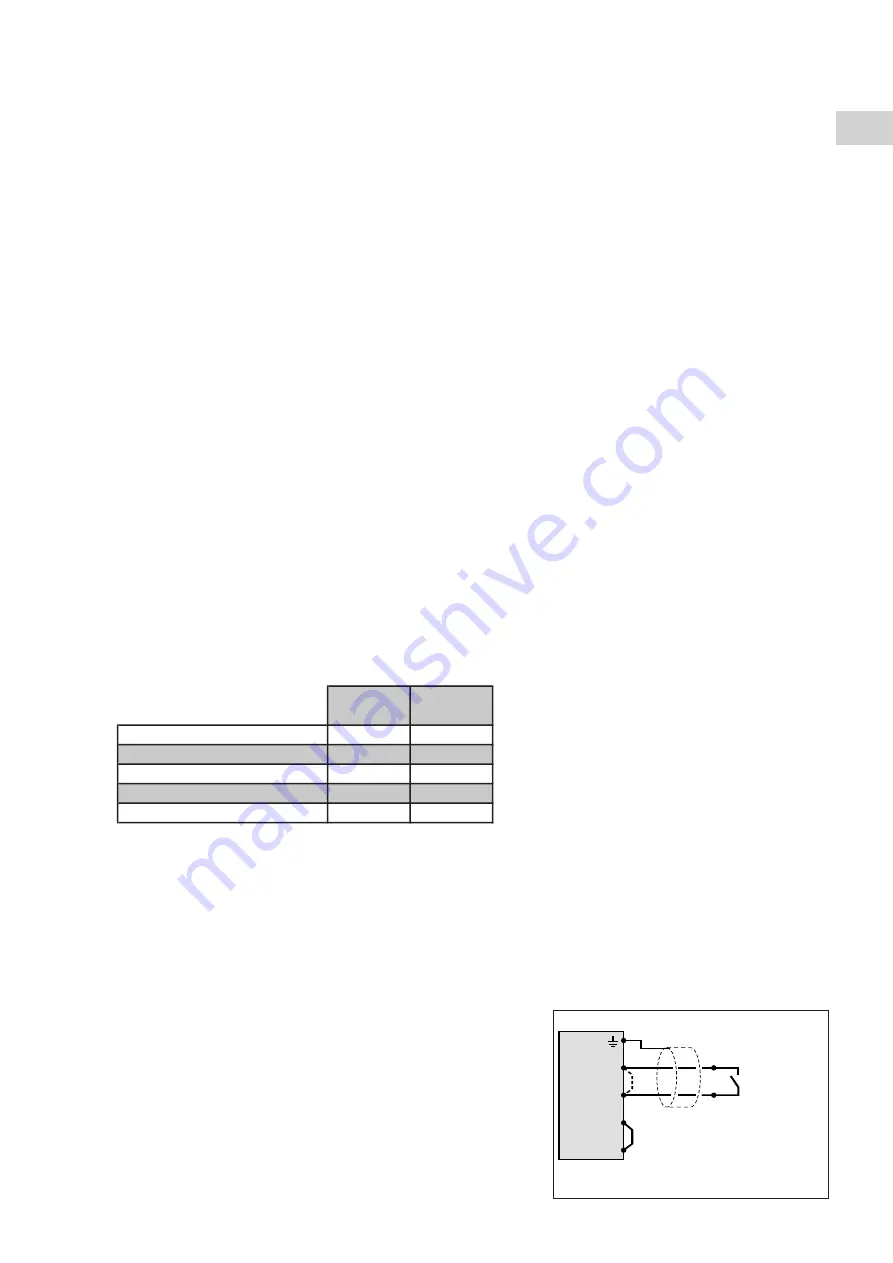
GB
5
4.2 - HYDRAULIC CONNECTION
• Connect the water pipes to the corresponding connections. See Ø and position on page 3.
• Install the hydraulic filter (supplied) on the water intake. Connect it using 2 isolation valves (not supplied) for cleaning
purposes.
• Install a shut-off valve (not supplied) if a fill / drainage connection is used.
•
CAUTION:
This device is not fitted with an expansion tank or a safety valve
.
These elements must be incorporated into the installation’s hydraulic circuit.
For installation of an electric heating module, install this safety valve in direct connection with the module (without isolation
valve).
NOTE:
"Water connection hose" accessories may be used (refer to the accessories paragraph).
4.3 - ELECTRICAL CONNECTION
4.3.1 - GENERAL:
• The acceptable voltage variation is: ± 10% during operation.
• The electrical connection conduits must be fixed.
• Use the cable clamps at the rear of the unit and route the wires under the electric panel, at the level of the terminal strips.
• Class 1 unit.
• The electrical installation must comply with the standards and regulations applicable where the unit is being installed (in
particular NF C 15-100
≈
IEC 364).
4.3.2 - POWER SUPPLY
• The power supply must come from an isolation and electric protection device (not supplied) in accordance with existing
regulations.
• The installation must be protected by a
three-pole circuit-breaker
(not included). See ratings in the table below.
Note
:
The unit is designed to be connected to a power supply having a TT neutral regime (neutral to ground) or TN.S regime
(to neutral) as per NF C 15-100.
POWER SUPPLY CABLE
• Section
: see table below.
• The sections are given as an indication only. They have to be verified and adapted, if necessary, according to the
installation conditions and the standards in force.
• Make the electrical connections to the terminal board as per the electrical diagrams.
CURRENTS AND CROSS-SECTIONS
CAUTION:
In the case of a three-phase power supply, prior to commissioning the unit, make sure that the phase rotation
order is correct. If the rotation order is not respected, the phase-sequence controller restricts the unit from
operating.
To fix this, simply invert the 2 phases.
4.3.3 - CONTROL BY EXTERNAL CONTACT
• The unit can be controlled remotely by connecting a good-quality, potential-free external contact (not supplied) (contact
closed = operation authorised, contact open = stand-by).
• The On / Stand-by signal is connected to terminals 1 and 2 of the PCB located in the switch box (remove the existing
bridge - see diagram).
• The wiring of this contact must not be routed near power cables in
order to avoid electromagnetic disturbances.
• Use shielded cable with twisted pair (shielding grounded on generator
side).
• Max. connection cable length: 100 m.
• Minimum wire size: 0.5 mm
2
.
PHT 13
PHT 16
400/3N/50
400/3N/50
Nominal current
A
6.7
8.6
Max. current
A
8.9
10.7
Starting current
A
69
70
Protection rating
A
12
16
Cross-section of power cable
5 G 2.5 mm
2
5 G 2.5 mm
2
1
2
4
3
PHT
On/Stand-by
(
k
) Jumper to be removed
(
k
)
Summary of Contents for PHT 13
Page 18: ...F GB D P I E...
Page 19: ...F GB D P I E...