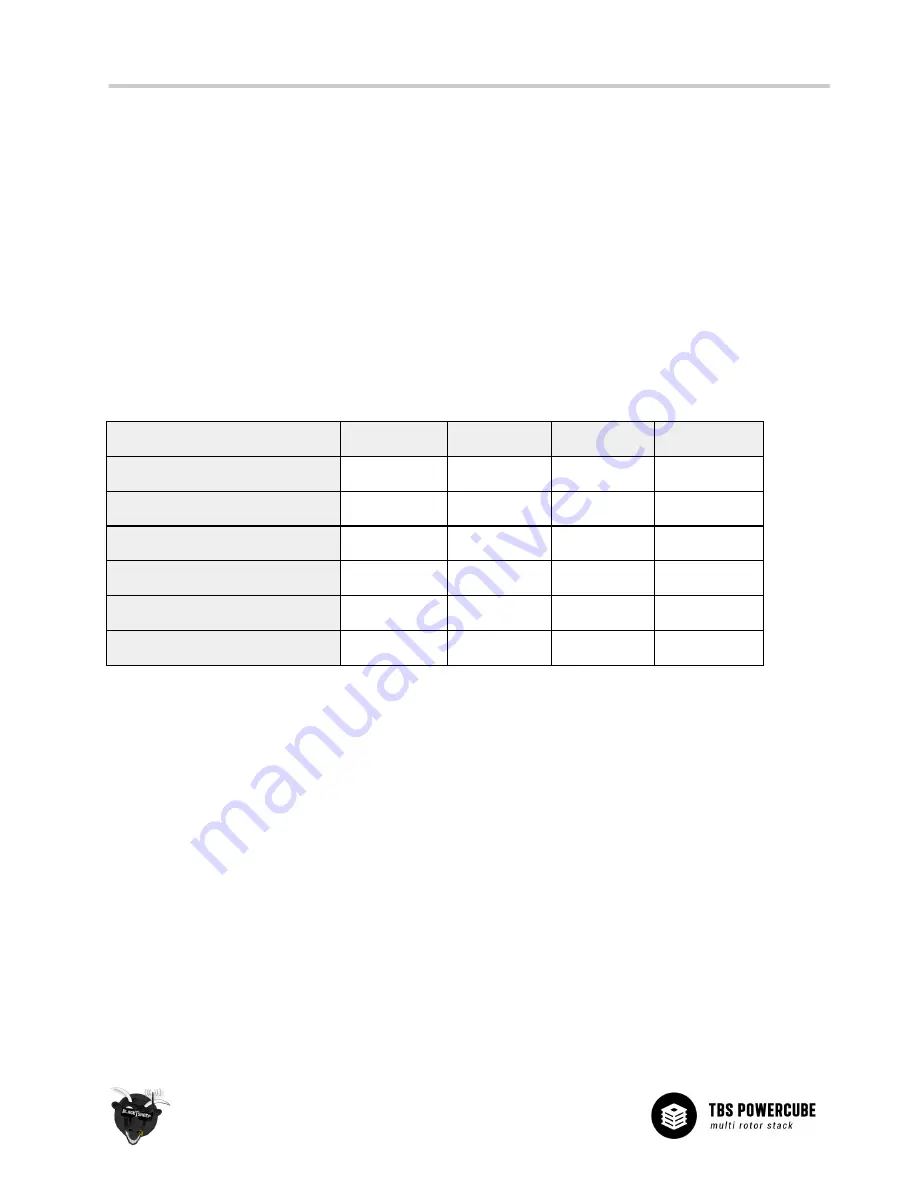
Connecting TBS equipment
There is an issue when you want to run BST devices like the GPS or BLACKBOX direct without a CORE PRO.
Most of the BST devices needs 5V which the CORE PRO provides. The CROSSFIRE RX does not power the BST
line when 5V is applied to the servo connectors.
The following explains the required power needs:
●
TBS BLACKBOX - Can be powered by the BST 5V or by the Flight Controller over the ext. FC port
●
TBS GPS - Can only be powered by the BST 5V
●
TBS CURRENT SENSOR - Provides VBatt but needs BST 5V to run itself
●
TBS CROSSFIRE RX - Can be powered over one of the eight servo connectors or by BST 5V
●
TBS CORE PRO / FPVISION - This is only device is providing 5V on the BST line
Power type: BST 5V
VBATT
ESC BEC 5V
FC 5V
TBS CROSSFIRE
✔
PWR IN
✔
PWR IN
TBS BLACKBOX
✔
PWR IN
✔
PWR IN
TBS GPS
✔
PWR IN
TBS CORE PRO / FPVISION
✔
PWR OUT
✔
PWR IN
TBS CURRENT SENSOR
✔
PWR IN
✔
PWR OUT
TBS BULLETPROOF ESC (SET)
✔
PWR OUT
33