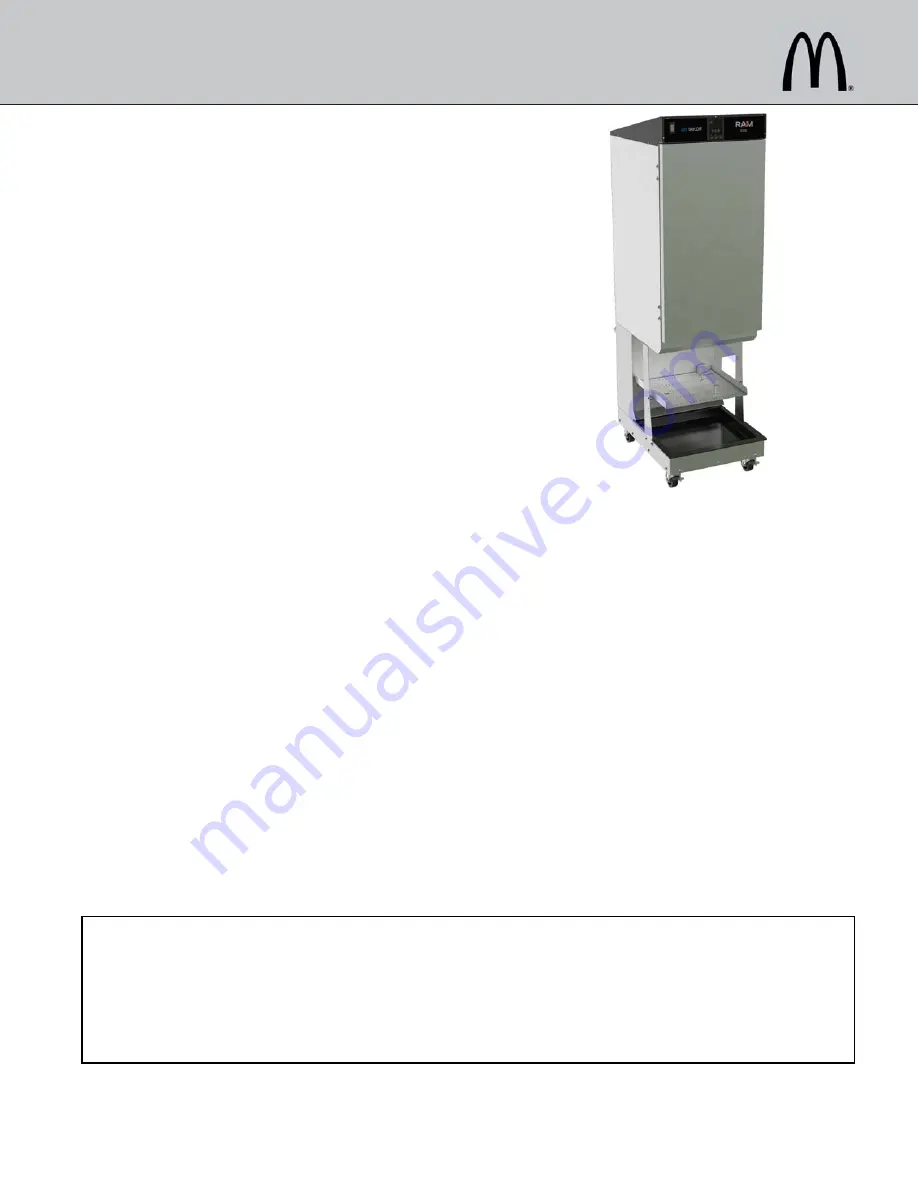
This manual is for the exclusive use of licensees and employees of McDonald's Corporation
.
©2005 McDonald's Corporation
04/07/20 (Original Publication)
Printed in
All Rights Reserved
(Updated 04/21/20)
The United States of America
EM SD11
089363-MCD
Warranty
Warranty information is contained in this Equipment Manual. Refer to the warranty information listed in the Limited Warranty on
Equipment and Limited Warranty on Parts sections and to the warranty classifications listed in the Parts Identification/Function
section when service is performed on your machine.
It is recommended that the operator take the necessary time to carefully read through the complete warranty information.
Thoroughly understand your warranty protection before you begin operation.
For any questions pertaining to the Taylor warranty, please contact Taylor Company, Rockton, Illinois 61072.
Frozen Food Dispenser
Taylor Model R200
Place this chapter in the Frozen Food
section of the Equipment Manual.
Manufactured exclusively for
McDonald's
®
by
Taylor Company
750 N. Blackhawk Blvd.
Rockton, IL 61072
Phone: (815) 624-8333
Toll Free Number
Outside Illinois:
1 (800) 228-8309
Inside Illinois:
1 (800) 851-5639
Fax: (815) 624-8000
Table of Contents
Introduction ........................................................................................................................................................................... 1
Unpacking and Installation.................................................................................................................................................... 1
Intended Use ........................................................................................................................................................................ 1
Specifications........................................................................................................................................................................ 1
Safety.................................................................................................................................................................................... 2
Equipment Safety ................................................................................................................................................................. 4
Dispenser Assembly ............................................................................................................................................................. 6
Disassembly, Defrost, and Cleaning..................................................................................................................................... 9
Dispenser Startup ................................................................................................................................................................. 9
Operation ............................................................................................................................................................................ 10
User Function Menu Structure ............................................................................................................................................ 13
Configuration (Config) Functions Menu Structure............................................................................................................... 14
Service Functions Menu Structure...................................................................................................................................... 16
Error Detection.................................................................................................................................................................... 20
Troubleshooting .................................................................................................................................................................. 21
Calibrations and Adjustments ............................................................................................................................................. 28
Parts Identification .............................................................................................................................................................. 31
Refrigeration System .......................................................................................................................................................... 42
Disposal of Equipment........................................................................................................................................................ 47
Electrical Diagram............................................................................................................................................................... 48
Limited Warranty on Equipment.......................................................................................................................................... 49
Limited Warranty on Parts .................................................................................................................................................. 51
Summary of Contents for McDonald's R200
Page 50: ...48 ELECTRICAL DIAGRAM Figure 33 ...
Page 56: ...089363 MCD ...