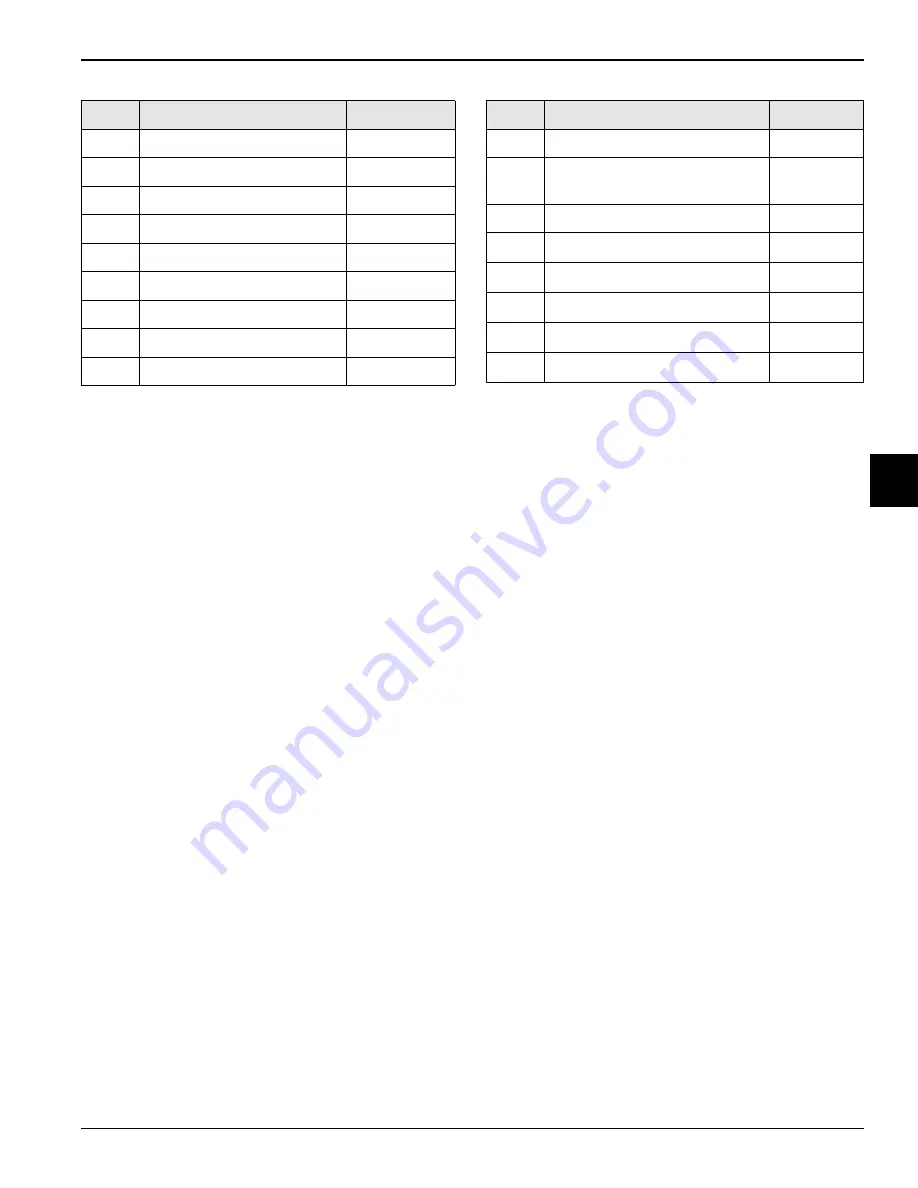
OPERATOR PARTS IDENTIFICATION
4-7
Models 702/741/772
Operator Parts Identification
4
Item
Description
Part No.
1
Kit A.-Cover-Hopper
X65368
2
Pan-Drip 11-5/8 Long
027503
3
Panel-Upper Side L.
028700
4
Tube-Feed-SS-3/16
028967-3
5
Panel-Rear
017563
6
Louver-Side-Top
051191
7
Panel-Upper Side R.
028701
8
Panel A.-Side Right
X44855-SER
9
Adaptor A.-Caster
X18915
Item
Description
Part No.
10
Caster-4” SWV 5/8 Stem
018794
11
Caster-4” SWV 5/8 Stem
w/Brake
034081
12
Panel-Service
046584
13
Shield-Splash
037041
14
Tray-Drip
014533
15
Panel A.-Side Left
X44853-SER
16
Panel A.-Front
X51264
17
Stud-Nose Cone
022822
Summary of Contents for 741
Page 10: ...1 6 TO THE INSTALLER Models 702 741 772 To the Installer 1...
Page 32: ...6 8 OPERATING PROCEDURES Models 702 741 772 Operating Procedures 6 Notes...
Page 38: ...9 2 PARTS REPLACEMENT SCHEDULE Models 702 741 772 Parts Replacement Schedule 9 Notes...
Page 44: ...11 4 LIMITED WARRANTY ON PARTS Models 702 741 772 Limited Warranty on Parts 11 Notes...