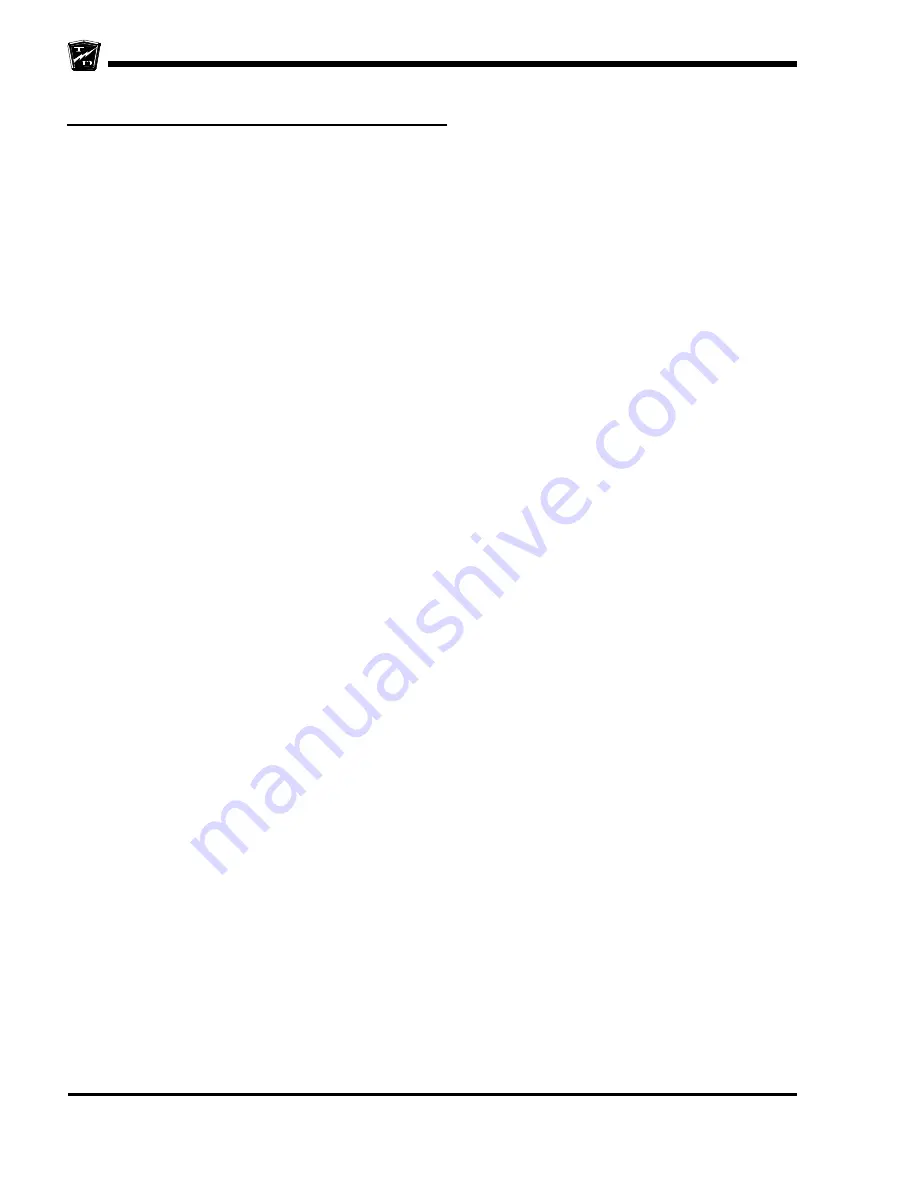
Appendixes
Appendixes
Appendix B
Page 6
Suggested Torque Values (critical hardware)
Torque Table
Torque Range
Group
Description
Ft-Lbs
In-Lbs
Nm
Brakes - - - - - - - - - - - - - - - - - - - - - - - -
Brake bolt (disc brake body)
11 - 11
132 - 132
15 - 15
Brake line tube nut fittings
12 - 13
144 - 156
16.3 - 17.7
Brake spider bolts (Dana 160mm hyd brakes)
25 - 35
300 - 420
34 - 47.6
Brake spider bolts (Dana 160mm mech brakes)
15 - 19
180 - 228
20.4 - 25.8
Brake spider bolts (Dana 7x1-3/4 brakes)
16 - 20
192 - 240
21.8 - 27.2
Electrical - - - - - - - - - - - - - - - - - - - - - - - -
Battery terminals
8 - 9
96 - 108
10.9 - 12.2
Front Axle - - - - - - - - - - - - - - - - - - - - - - - -
Front spindle nut
-
-
-
Note: Refer to maintenance section in the service manual
King pin
-
-
-
Note: Refer to maintenance section in the service manual
Rear Axle/Transmission - - - - - - - - - - - - - - - - - - - - - - - -
3rd member Gear case cover (GT drive)
45 - 50
540 - 600
61.2 - 68
Axle bolt (GT drive)
275 - 275
3300 - 3300
374 - 374
Axle hub nut (Dana)
95 - 115
1140 - 1380
129.2 - 156.4
Axle tube to center section (Dana F-N-R)
25 - 35
300 - 420
34 - 47.6
Carrier cap bolts (Dana)
100 - 120
1200 - 1440
136 - 163.2
Differential Cover plate (Dana H12)
18 - 25
216 - 300
24.5 - 34
Drain plug (Dana H12)
25 - 40
300 - 480
34 - 54.4
Drain plug (GT drive)
21 - 25
252 - 300
28.6 - 34
Gear case to 3rd member (GT drive)
18 - 20
216 - 240
24.5 - 27.2
Motor mounting (GT/Dana)
6.5 - 7
78 - 84
8.8 - 9.5
Pinion nut (F2/F3)
175 - 175
2100 - 2100
238 - 238
Pinion nut (GT drive)
154 - 169
1848 - 2028
209.4 - 229.8
Ring gear (Dana)
35 - 45
420 - 540
47.6 - 61.2
Wheel lug nut
75 - 90
900 - 1080
102 - 122.4
Steering - - - - - - - - - - - - - - - - - - - - - - - -
Ball joint clamp
28 - 32
336 - 384
38.1 - 43.5
Ball joint nut
40 - 45
480 - 540
54.4 - 61.2
Pitman nut (18-308-21 steering gear)
75 - 100
900 - 1200
102 - 136
Pitman nut (18-308-25 steering gear)
181 - 217
2172 - 2604
246.2 - 295.1
Rod end nut
20 - 25
240 - 300
27.2 - 34
Steering shaft pinch bolt
24 - 26
288 - 312
32.6 - 35.4
Steering wheel nut (18-308-21 steering gear)
28 - 32
336 - 384
38.1 - 43.5
Steering wheel nut (18-308-25 steering gear)
72 - 86
864 - 1032
97.9 - 117
Suspension - - - - - - - - - - - - - - - - - - - - - - - -
Leaf spring hangers
-
-
-
Note: Refer to maintenance section in the service manual
Summary of Contents for B 2-48
Page 2: ......
Page 70: ...Maintenance Service and Repair Steering Page 22 Exploded View of Steering Gear ...
Page 88: ...TAYLOR DUNN ...
Page 114: ...TAYLOR DUNN ...
Page 120: ...TAYLOR DUNN ...
Page 132: ...TAYLOR DUNN ...
Page 134: ...TAYLOR DUNN ...
Page 164: ...Illustrated Parts Parts Page 2 Front Axle ...
Page 166: ...Illustrated Parts Parts Page 4 Steering Knuckle ...
Page 168: ...Illustrated Parts Parts Page 6 Steering Linkage ...
Page 174: ...Illustrated Parts Parts Page 12 Rear Suspension View from rear ...
Page 176: ...Illustrated Parts Parts Page 14 Transmission Gear Case ...
Page 180: ...Illustrated Parts Parts Page 18 Rear Brakes Front Brakes ...
Page 182: ...Illustrated Parts Parts Page 20 Brake Lines Master Cylinder ...
Page 184: ...Illustrated Parts Parts Page 22 Motor ...
Page 186: ...Illustrated Parts Parts Page 24 Motor Mount Apply 94 421 34 grease to inside of motor coupler ...
Page 188: ...Illustrated Parts Parts Page 26 Wheels and Tires Ref wheel hub 1 2 5 assembly 4 3 6 7 8 9 10 ...
Page 196: ...Illustrated Parts Parts Page 34 Lighting Stobe Light 4 1 2 3 5 6 7 ...
Page 206: ...Illustrated Parts Parts Page 44 Seat Cushions and Deck ...
Page 208: ...Illustrated Parts Parts Page 46 Mirrors 92 202 00 Assembly Miscellaneous Frame Components ...
Page 210: ...Illustrated Parts Parts Page 48 Decals ...
Page 212: ...Illustrated Parts Parts Page 50 Cab Options Steel Cab Fiberglass cab ...
Page 218: ...Illustrated Parts Parts Page 56 Hydraulic Dump Body Option ...
Page 220: ...Illustrated Parts Parts Page 58 Rear Cargo Box 1 2 3 4 5 6 5 Top Covers ...
Page 222: ...Illustrated Parts Parts Page 60 Hitches ...
Page 224: ...TAYLOR DUNN ...