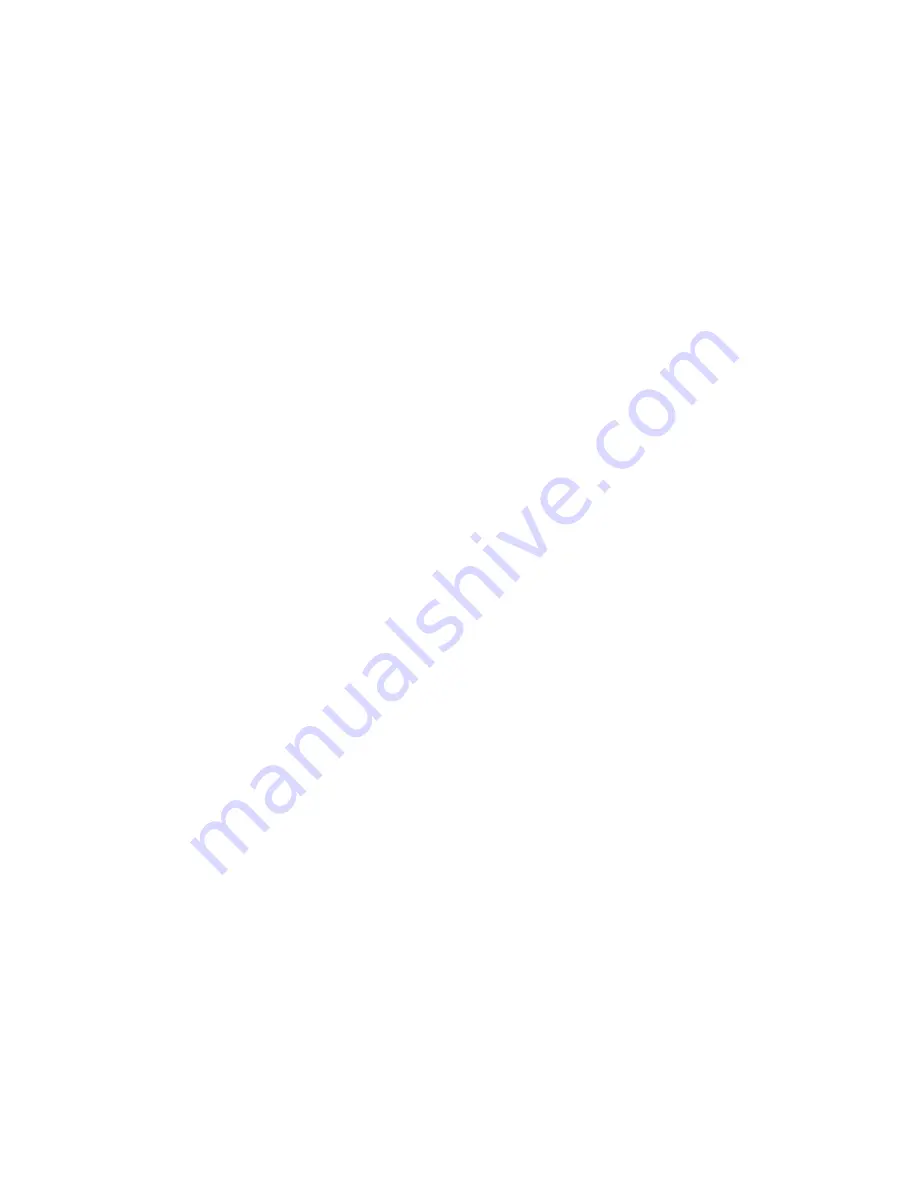
15
deck is lifted by a crane above the hull. The joint is prepared with 5200 epoxy compound and the
deck is then set onto the hull. The joint is then bolted together using stainless steel-bolts on varying
centers depending on the curve of the hull at the various points. Once the joining has been
accomplished, the joint is fiberglassed as shown in the figure. The result is a single piece, extremely
strong hull with a rigidly curved hollow beam in the form of a bulwark running nearly the entire
length of the yacht.
Once these critical operations have been finished to the satisfaction of the company engineers,
exterior trim is installed and the work on the accommodations is undertaken. A team of the world's
finest boat carpenters and finishers takes over the yacht and frames in the interior cabinets and bunks,
as shown on the plans. This work is done with extreme care and attention to detail. Framing is
actually glassed into the hull and becomes an integral part of it. As a result, the quality and livability
of the accommodations is largely a function of how well the framers do their job. Cabinets, doors,
drawers, and the like are done by cabinet makers in a specialty shop to the order of the production
foremen. TaYang engineers closely supervise every step to insure that dimensions are met and proper
installation is made. The result is a yacht whose strength and beauty are second to none and whose
accommodations precisely fit the needs of its new owner.
The aluminum spars supplied are ordered from overseas suppliers- Taiwan has no extrusion
capability at this writing. Generally, the suppliers have been ISOMAT of France and YACHT SPAR
out of New Zealand. ISOMAT masts are received already anodized and are not necessarily painted.
YACHT SPARS are painted at the yard and the color can be selected by the buyer. TaYang uses a
primer and polyurethane for this. Aluminum spars are also being imported from Japan. These are
painted by the spar manufacturer.
Standing rigging is assembled at the yard using Japanese stainless steel cable and Taiwanese-made
turnbuckles and swage end fittings. A crew at the factory sets up the spars and all of the rigging is
fitted to each yacht. This is an important factor in cutting down the number of modifications which
might have to be done in the U.S. Similarly, pulpit, lifelines, stanchions, and bowsprit are all installed
to insure proper fit. The stanchions and pulpits are among the industry’s best.
The final step is packing the yacht for shipment. Spars, rigging, and any projecting assemblies are
all disassembled and packed either in the hull, or, in the case of the masts, into special boxes. On the
shipping date, the yacht is loaded onto a lowboy and taken to the huge port city of Kaohsiung where it
is loaded aboard one of the many container carriers which operate between Taiwan and the United
States.
E. Procedures for Documentation
Documentation must be accomplished with the United States Coast Guard in the United States or
with the governing agency in the country where your vessel is to be registered. We suggest you
contact the Documentation office nearest you for full details, forms, instructions, duties and customs
Summary of Contents for VANCOUVER 42
Page 1: ...1 OPERATIONS AND MAINTENANCE MANUAL TAYANA VANCOUVER 42...
Page 2: ...2 Tayana V 42 Center Cockpit Sailplan...
Page 3: ...3 Tayana V 42 Aft Cockpit Interior Layout...
Page 12: ...12 Figure II 1 Fiberglass Layout Schedule...
Page 13: ...13 Figure II 2 V 42 Deck and Hull Joint...
Page 19: ......
Page 37: ...37 Figure IV 1 Fuel Supply Plumbing...
Page 38: ...38 Figure IV 2 Fluid Plumbing System...
Page 39: ...39 Figure IV 3 Center Cockpit Tankage Diagram...
Page 43: ...43 TABLE IV 1 Direct Current Energy Audit...
Page 48: ...48 Figure IV 6 Waste Water Plumbing System...
Page 51: ...51 Figure IV 8 Propane System...