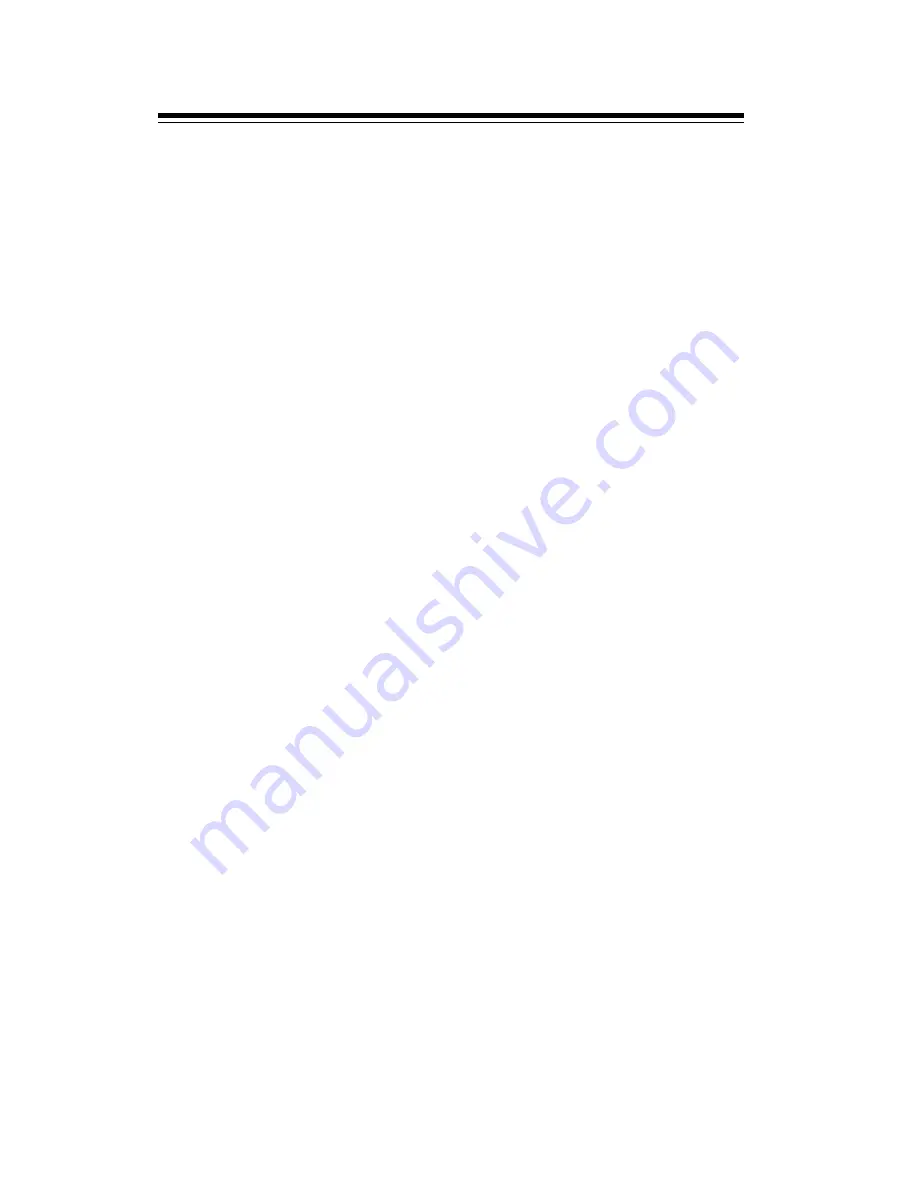
12
Notes
1.
Keep body weight minimum
by selecting proper materials
and designs. This will save fuel
and increase tyre life.
2.
Use curved window glass, avoid
sharp corners and protruding
out destination boards to
reduce wind resistance.
3.
Select body dimensions,
seating space and gangway
width to comply with current
government regulations.
4.
Ensure ease of removal and
assembly of various aggregates
like gearbox, suspension,
battery, spare wheel etc.
Provide flaps/cut outs for
servicing.
5.
De-rust, phosphate and apply
primer to the body skeleton
before fixing panels.
6.
Use zinc plated hardware of
standard quality for various
body joints.
7.
Protect instrument panel,
steering wheel, driver’s /co-
driver’s seats, clutch fluid
containers, hoses etc. from
damage while carrying out
structural work.
8.
Do not drill or weld chassis
frame or remove any rivet. Do
not use chassis or leaf spring as
electrical earthing point during
welding.
9.
Do not clamp bus body cross
bearers to chassis cross
members.
10.
No body mountings should foul
with any chassis aggregate or
frame cross member.
11.
Avoid practice of cutting
chassis cross member for
mounting of ‘U’ bolts.
12.
Do not extend chassis rear
overhang.
13.
Avoid eccentric mounting of
cross bearers.
14.
Do not use balata packing more
than 6 mm thick for cross
bearer mounting. This will
result in premature perishing
and damage to chassis long
member. In case thicker
packing is required, use steel
plates to compensate
alongwith 6 mm balata packing.
15.
Avoid ‘U’ bolts touching chassis
long members. This should be
done by using aluminium alloy
packing between ‘U’ bolt
bottom radius and long
member bottom flange.
16.
As far as possible, avoid post
location over wheel arch.
17.
No modification to front face
of cowl should be attempted
which would restrict air flow to
the radiator and air cleaner.
Reducing the height/width of
centre flap or closing louvers
provided on cowl front face
are to be avoided.
1.5 Body building
General