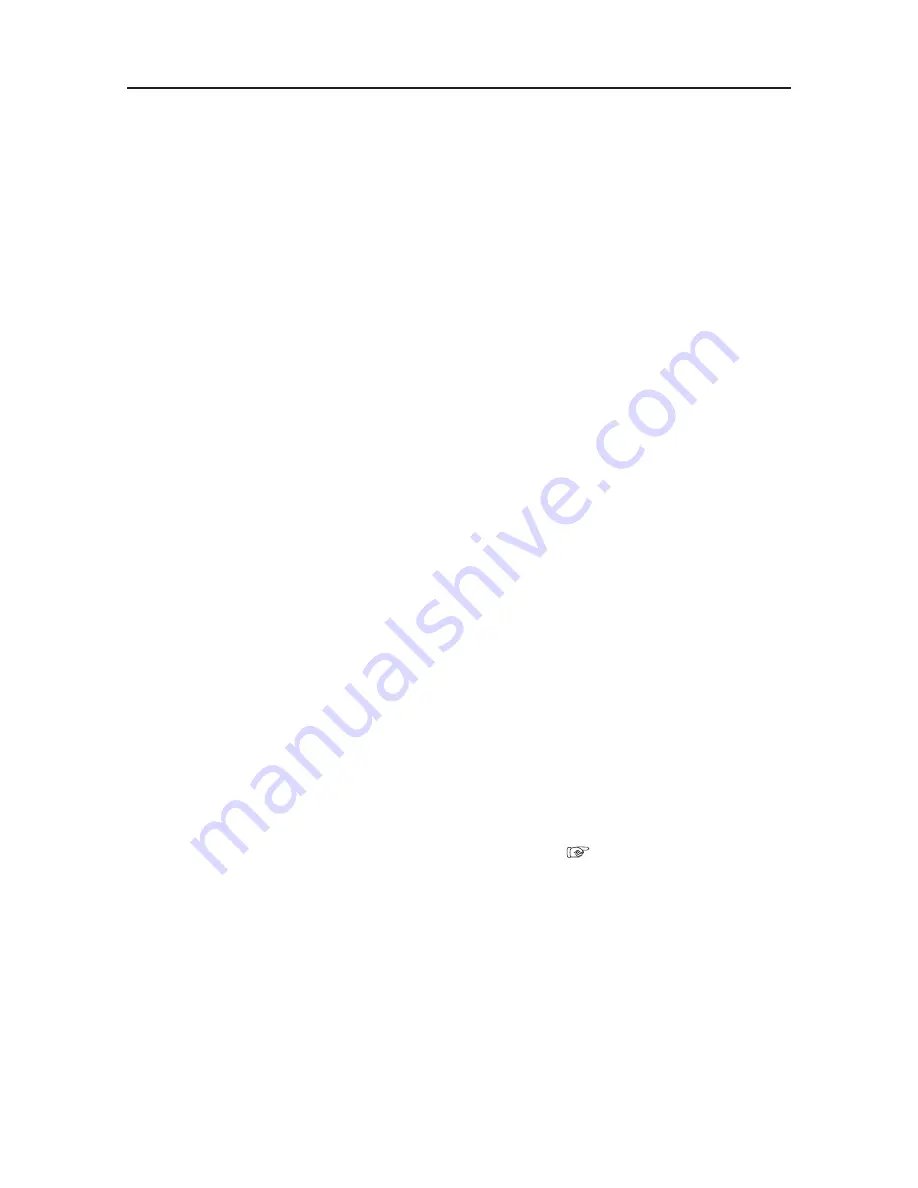
IV-37
HYDRAULIC UNITS
GEAR PUMP
Other likely causes are as follows.
• Excessive load due to damage to the relief valve.
• Cavitaion or aeration.
• Hydraulic oil temperature is too high.
• Hydraulic oil is deteriorated.
• Hydraulic oil
·
s viscosity is low.
If it is necessary to replace the bushings, this means
that the gear shaft and gear side surfaces are also
rough or worn severely, so replace the gears at the
same time as the bushings are replaced.
Gear
Replace a gear if it is in the following condition.
1. The shaft or the gear side surfaces ar so rough
that they look like they have been clawed.
2. There are cracks in the tooth roots and there is
extreme abnormal wear in the tooth surfaces.
3. None of the points coming into contact with the
oil seal should be abraded to a depth in excess of
0.1 mm.
Seals
• Check oil seals for scratches in the seal surface,
wear, deformation or deterioration of the rubber
·
s
elasticity. If a seal is abnormal, replace it.
• Replace seals when the hydraulic pump is disas-
sembled.
• Check the backup ring for scaling and cutting. If
it is abnormal, replace it.
Test Operation
The best method for testing the pump
·
s operation is
to mount it in a test stand. However, if that cannot
be done, test it under the conditions it would be sub-
jected to if it were installed in the machine.
Also, if any abnormal wear is discovered during
disassembly, be sure to replace the hydraulic oil and
return filter.
1. Install a pressure gauge in the high pressure pip-
ing near the pump.
2. Run the engine at 500~1,000 min
-1
and set the
control valve in the neutral position.
3. Run the pump for 10 minutes under the condi-
tions in (2), then increase the engine
·
s speed
to 1,500~2,000 min
-1
and run it for another 10
minutes.
4. Next, run the pump so that it reaches the rated
pressure (
“II. Specifications, Specification
Tables”) for 5 minutes at a time for each addi-
tional 1.96~2.94 MPa of pressure.
Afterward, after operating each ciruit for about 5
minutes, replace the return filter or clean it.
In addition, during the process of raising the pres-
sure, pay careful attention to the oil temperature,
the pump
·
s surface temperature and the operating
noise. If the oil temperature or the pump
·
s surface
temperature become abnormally high, eliminate the
load from the pump and let the temperature drop
before resuming the test.
Summary of Contents for TL150
Page 1: ...TL150 Track Loader BOOK No CT7E901 WORKSHOP MANUAL Serial No 21500004...
Page 4: ...0 4...
Page 5: ...I 1 I GENERAL...
Page 18: ...I 14 GENERAL...
Page 19: ...II 1 II SPECIFICATIONS...
Page 44: ...III 1 III MACHINE CONFIGURATION...
Page 94: ...III 51 MACHINE CONFIGURATION ELECTRICAL SYSTEM ELECTRICAL SYSTEM ELECTRICAL WIRING DIAGRAM...
Page 122: ...III 79...
Page 146: ...MACHINE CONFIGURATION III 103...
Page 147: ...IV 1 IV HYDRAULIC UNITS...
Page 152: ...IV 6 HYDRAULIC UNITS HST PUMP 1 Plug 2 Plug 3 Plug 4 Screw 5 Seal Nut 6 Plug Pump Assembly 4 4...
Page 189: ...IV 43 HYDRAULIC UNITS GEAR PUMP INSPECTION AND ADJUSTMENT IV 36 38 TROUBLESHOOTING IV 39...
Page 230: ...IV 84 HYDRAULIC UNITS PILOT VALVE INSPECTION AND ADJUSTMENT IV 79 TROUBLESHOOTING IV 80...
Page 261: ...IV 115 HYDRAULIC UNITS TRAVEL MOTOR DISASSEMBLY AND ASSEMBLY Special tools...
Page 263: ...IV 117 HYDRAULIC UNITS TRAVEL MOTOR...
Page 282: ...IV 136 HYDRAULIC UNITS TRAVEL MOTOR...
Page 283: ...V 1 V TROUBLESHOOTING...