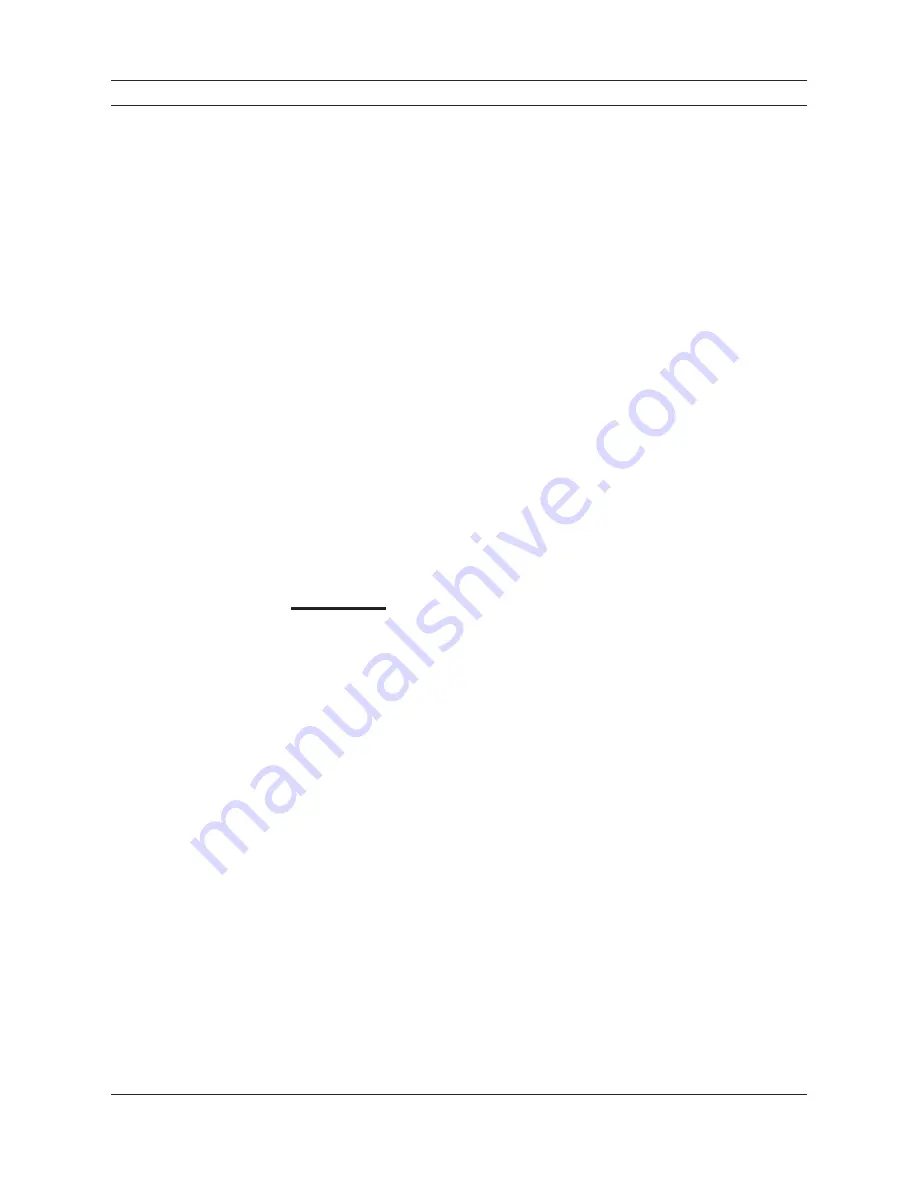
III-102
Technicians frequently add refrigerant to a system, replacing refrigerant seep-
age through system connections or fittings. If the system has been maintained
regularly (every three to six months), adding a small amount of refrigerant may
result in normal system function. However, the best procedure is to check all
connections and look for, find and repair any leaks before adding refrigerant.
When your leak detector indicates the presence of a leak, you can
·
t tell how
long the system has been leaking. Finding one leak doesn
·
t mean there are not
others. Until you have some AC system work experience, it will be hard to guess
how much refrigerant may have leaked. If you have to top a system off with a half
pound of refrigerant or more, adding refrigerant is not the answer.
Find the leak. Recover all of the refrigerant and repair the system. The mois-
ture absorbing capacity of any desiccant material is limited and cannot be mea-
sured. For that reason, replace the receiver-drier or accumulator. Then evacuate
the system for an hour and recharge with refrigerant.
When a compressor shaft seal has leaked oil and the refrigerant charge is a little
low, the shaft seal may have leaked because the air conditioner was not used. The
seal can get a little out of round from the weight of the crankshaft and leak above
the shaft. Running the compressor may cause the seal to swell and close up the
leak. The shaft rotation exerts force all around the seal and puts life back into it.
To prevent this from happening, manufacturers recommend regular AC system
operation a minimum of every couple of weeks even in cool weather.
Keep in mind that the compressor can cause a vacuum inside the system if there
is a restriction in the system. That means it can suck air and moisture inside under
some conditions. It will pull these contaminants in through the same space where
refrigerant and refrigerant oil has leaked out.
Conclusion
What could the air conditioning problem and it
·
s cause have been at the beginning of
this chapter? The operator was in a hurry, but you were able to start your troubleshoot-
ing with the answers he gave you. Problems your inspection may have turned up are
a very low refrigerant charge, a contaminated system or defective compressor. Those
are not quick fix jobs.
On the other hand, you might have found enough debris on the condenser fin sur-
face to boost high side pressures to an abnormal level during the hottest part of the day.
So the Trinary™ or high pressure switch would cut out from high pressure—but reset
itself. You cleaned the condenser, added a half pound of refrigerant and AC system
pressures and function returned to normal. Service and repair took a half hour. But
there was no way to tell without using your knowledge and experience. By now you
are pretty familiar with AC system problems, the reasons for some of them, trouble-
shooting and repair. In
Chapter 9
we will describe complete system purging, evacua-
tion, flushing and recharging.
Conclusion
Summary of Contents for TL150
Page 1: ...TL150 Track Loader BOOK No CT7E901 WORKSHOP MANUAL Serial No 21500004...
Page 4: ...0 4...
Page 5: ...I 1 I GENERAL...
Page 18: ...I 14 GENERAL...
Page 19: ...II 1 II SPECIFICATIONS...
Page 44: ...III 1 III MACHINE CONFIGURATION...
Page 94: ...III 51 MACHINE CONFIGURATION ELECTRICAL SYSTEM ELECTRICAL SYSTEM ELECTRICAL WIRING DIAGRAM...
Page 122: ...III 79...
Page 146: ...MACHINE CONFIGURATION III 103...
Page 147: ...IV 1 IV HYDRAULIC UNITS...
Page 152: ...IV 6 HYDRAULIC UNITS HST PUMP 1 Plug 2 Plug 3 Plug 4 Screw 5 Seal Nut 6 Plug Pump Assembly 4 4...
Page 189: ...IV 43 HYDRAULIC UNITS GEAR PUMP INSPECTION AND ADJUSTMENT IV 36 38 TROUBLESHOOTING IV 39...
Page 230: ...IV 84 HYDRAULIC UNITS PILOT VALVE INSPECTION AND ADJUSTMENT IV 79 TROUBLESHOOTING IV 80...
Page 261: ...IV 115 HYDRAULIC UNITS TRAVEL MOTOR DISASSEMBLY AND ASSEMBLY Special tools...
Page 263: ...IV 117 HYDRAULIC UNITS TRAVEL MOTOR...
Page 282: ...IV 136 HYDRAULIC UNITS TRAVEL MOTOR...
Page 283: ...V 1 V TROUBLESHOOTING...