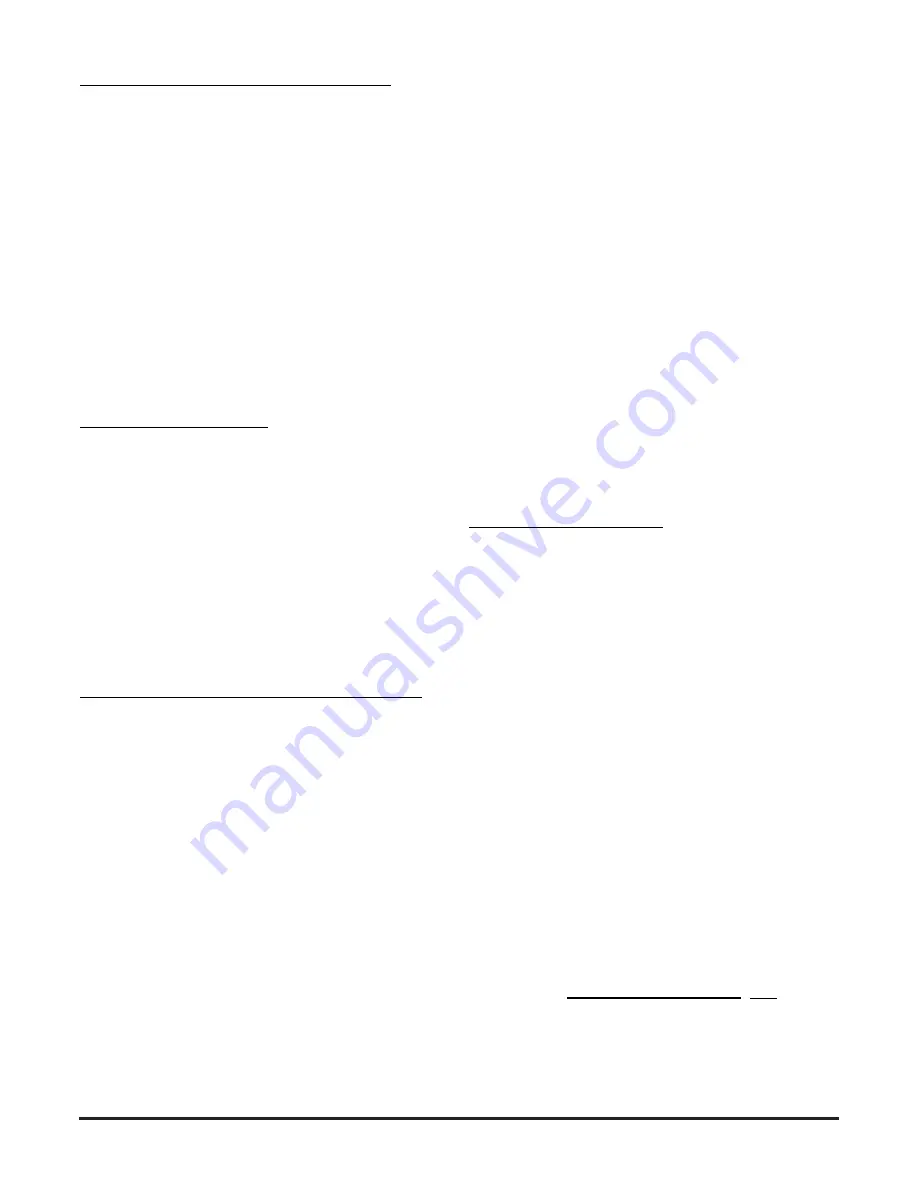
D200-100-00
3
I56-3888-005
Preparing to Configure or Monitor a FAAST LT Device
To connect and communicate with a FAAST LT device via the
PC USB port, PipeIQ™ must be running a project (.mdf file) that
matches the type of FAAST LT device being used . If no project
exists on the PC, one will have to be created prior to connecting
(See
Creating a Project
section) .
To communicate with a FAAST LT Device.
Ensure that the FAAST LT unit is in
Maintenance
mode, PipeIQ™
is running on the PC, and a USB cable is connected from the
internal socket to the PC .
In PipeIQ™, open the project file associated with the FAAST LT
device to be monitored . The
Left
pane in PipeIQ™ will show the
aspirating system tree (loading the file may take a little while).
Click on the
FAAST LT Device
to highlight it .
Select
Connect Device
from the
Tool
menu .
Follow the on-screen instructions to make the connection.
The device is connected when a
Green Tick
is indicated by the
device . A
Red Cross
indicates that the device is not connected .
Select the
Monitoring
/
Configuration
tab as required .
Monitoring a FAAST LT Device
Once connected to a FAAST LT device, PipeIQ™ can be used to
monitor the device; it is possible to check the status (read device
information), review event logs, activate relays, test the fan speed
and reset the device .
Open a relevant project, highlight the FAAST LT device, Select
Connect Device
from the
Tools
menu and make the connection .
Double click the FAAST LT device to open the large pane on the
right side of the screen . View the device status features by clicking
on the
Monitoring
tab . An additional tab at the top of the pane
provides access to further features .
Ensuring that the FAAST LT device is highlighted in the left pane,
Select
Device information
from the
Tools
menu to view further
info .
For more information on using the
Monitoring
options, see the
PipeIQ™
Help
Menu .
IMPORTANT NOTES ON ALTERING FAAST LT SETTINGS
FAAST LT devices are shipped with factory default parameters that
should be adequate for many aspirating applications; a list of these
parameters is shown in
Appendix A
. If these factory default parameters
are altered, the validity of the new settings must be confirmed.
The FAAST LT device is approved to EN54-20 classes A, B and
C (CPR 305/2011). To ensure adherence to this standard, the
class of any pipe/hole configuration and detector sensitivity
must be determined using the design feature of the PipeIQ™
software (version 2 and higher).
Air Flow Settings
The FAAST LT operating settings can only be changed using the
PipeIQ™ application. Pipe layouts should be verified for EN54:20
compliance by running a PipeIQ™ simulation project (via the
Pipe
Design
tab) and evaluating the results against the strict approval
criteria in the program. Sensitivities, air flow rates and limits etc are
adjusted and optimised within PipeIQ™; the FAAST LT parameter
values are created in the pipe design project and stored in an
associated configuration file. The resulting air flow rate should
be set as the reference flow into the configuration by pressing
the
Apply to Configuration
button in the PipeIQ™
Pipe Design
mode, which will automatically set the new airflow limits.
Modifying the reference flow arbitrarily from within the
Configuration
screen is not recommended . Changing the fan speed using the
manual mode from within the
Configuration
screen should be
avoided . These change options are available primarily for test
purposes only . Manually setting the fan speed to change the air
flow will not alter the associated hi/lo flow limit settings in the
FAAST LT unit . Therefore this option should not be used to set
or change air flow values in an EN54 compliant pipe system; the
PipeIQ™
Pipe Design
facility should always be used .
Delay Settings
The default values for flow fault delay, general fault delay, pre-
alarm and alarm delay, and remote output alarm time that are
pre-set into the FAAST LT unit are critical for compliance to the
EN54:20 standard.
Within the
Configuration
options it is possible to increase delay
times for these actions, but any changes should be made with
extreme caution . Increasing any of these delays should not be
done without a clear understanding of the consequences to the
requirements of the EN54:20 standard.
An increase/decrease in flow above/below the Flow High / Flow
Low limits will result in a Flow Fault after a factory default delay of
60 seconds. Once the flow is returned to a normal level, the fault
condition will be cleared immediately .
In environments where the sampled airflow may be affected by
sudden temperature/pressure changes due to air handling units,
doors opening/closing etc . or there is a risk of physical interference
with the sampling point, it may be necessary to increase the delay
between the flow going out of limits and signalling a Flow Fault
condition. Delay values of up to 240 seconds before signalling a
fault are available when setting up the detector . This is to allow
time for the air pressures to stabilise after the temporary event .
Configuring a FAAST LT Device
The PipeIQ™ configuration interface provides a method for
viewing and editing the device configurations. Once connected to
a FAAST LT device, PipeIQ™ can be used to configure the device;
it is possible to set up relay actions, fan speed, critical times and
dates, event log requirements and other operational parameters .
For the Stand Alone versions it is also possible to configure the
alarm thresholds .
With the
Configuration
options selected, the
General
tab displays
in the right pane, with further options available using the
Advanced
button (details such as passwords, time-outs and external input
information) . If a new project was created, the initial screen display
will show the factory default settings for the device type selected .
Select the
Alarms
and
Relays
tab to show details such as relay
latching, alarm mode settings and delays .
Select the
Channels and Sensors
tab to show details such as fan
speed settings and sensor or channel disablement .
Note:
There are some differences between the graphic screens
for the FAAST LT stand alone and loop based units, owing to the
variation in control and operation between the two .
For more information on using the
Configuration
options, see the
PipeIQ™
Help
Menu .
Follow the steps below to configure a FAAST LT device.
1) Open a relevant project, highlight the FAAST LT device, Select
Connect Device
from the
Tools
menu and make the connection .
Double click the FAAST LT device to open the large pane on
the right side of the screen . View the device settings by clicking
on the
Configuration
tab . At this point, the screen will show the
configuration
from the current project file
,
NOT
the actual
device configuration.
2) Ensuring that the FAAST LT device is highlighted in the left
pane, Select
Get Configuration
from the
Tools
menu; the
FAAST LT current configuration parameters will be uploaded
from the device and shown on the PC screen . Note that this
uploaded data from the device will overwrite the configuration
file values in the current project.