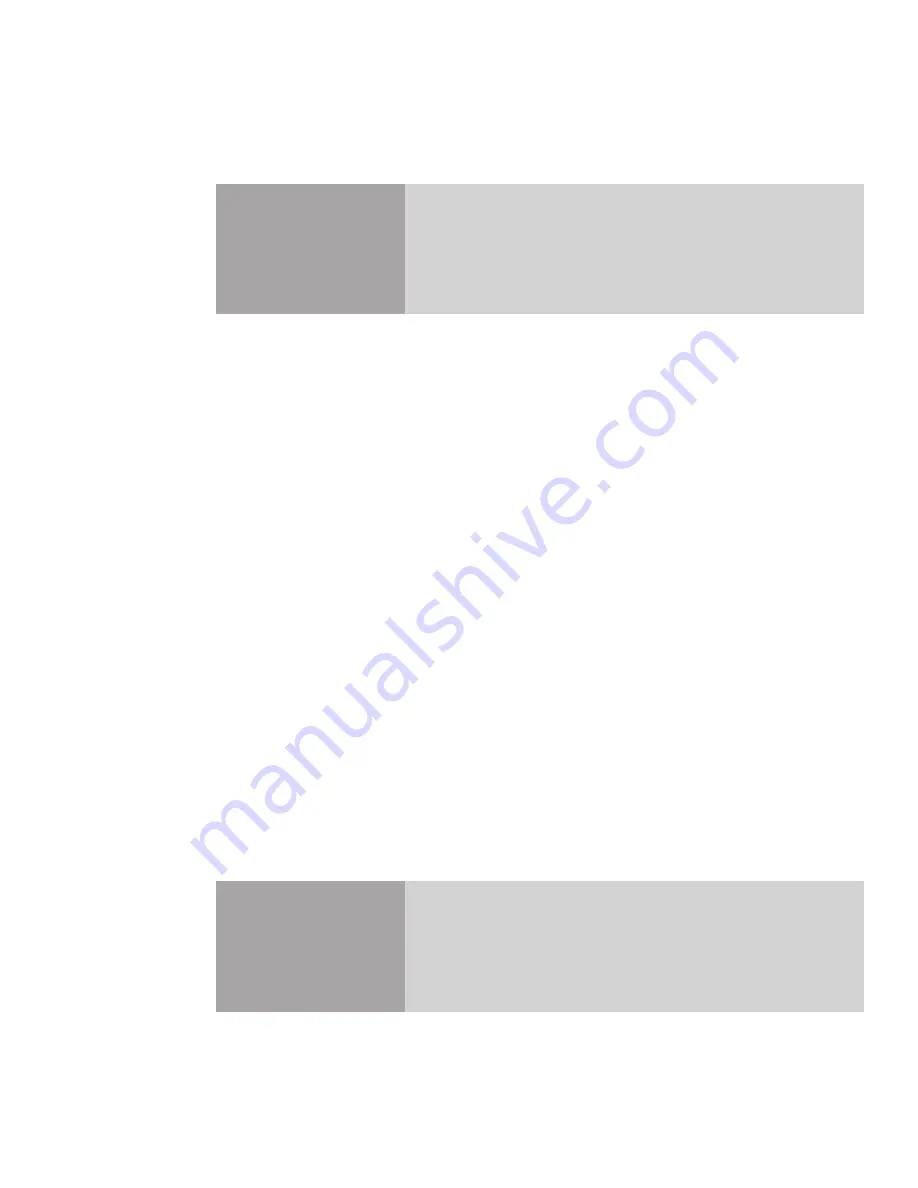
operation
2
7
Synrad
Pulstar p100
operator’s manual
Caution
possible
equipment
damage
Do not flow coolant through the laser for an extended period of time
when the laser is shutdown. This causes condensation to form inside
the laser which may result in catastrophic damage to internal optics
and electronic circuits.
Start-up and pulsed operation
5
Shut off the chiller or otherwise stop coolant flow through the laser.
6
Shut off gas purge flow to the laser. In dirty or dusty environments; however, it may be necessary to
purge the laser continuously to prevent contamination of internal optics.
If your Pulstar OEM p100 laser fails to lase, refer to
Troubleshooting
in the Maintenance/Troubleshooting
chapter for troubleshooting information.
Pulsed operation from PWM signal
source
Follow these basic steps to operate the OEM p100 as a pulsed laser. Although a tickle signal is not re-
quired, you will need to provide PWM Command signal pulses as well as
Remote Interlock
and
Shutter
Open Request
input signals to the p100’s
User I/O
connector. Refer to
User I/O connections
in the Techni-
cal Reference chapter for interface details and refer to
Controlling laser power
in the Technical Reference
chapter for PWM Command signal descriptions.
Starting auxiliary equipment
1
Ensure that all personnel in the area are wearing protective eyewear.
2
Remove the red self-adhesive aperture seal covering the laser aperture.
3
Use an appropriate beam block to prevent the beam from traveling beyond the work area.
4
Connect your PWM pulse signal source so that the output is connected to
PWM Input
(Pin 9) on
the
User I/O
connector and connect the ground or return of the source to
PWM Return
(Pin 1).
Caution
possible
equipment
damage
Inlet cooling water temperature must always be maintained above the
dew point to prevent condensation and water damage to your Pulstar
laser.
5
Turn on the chiller and set a temperature setpoint between 18 °C–22 °C. Verify that the chiller is
delivering a flow rate of 5.7–7.6 lpm (1.5–2.0 GPM) at less than 414 kPa (60 PSI) of pressure.
Summary of Contents for Pulstar P100 Series
Page 2: ......
Page 4: ......
Page 12: ...x Synrad Pulstar p100 operator s manual This page intentionally left blank...
Page 48: ...operation 210 Synrad Pulstar p100 operator s manual This page intentionally left blank...
Page 110: ...index i8 Synrad Pulstar p100 operator s manual This page intentionally left blank...