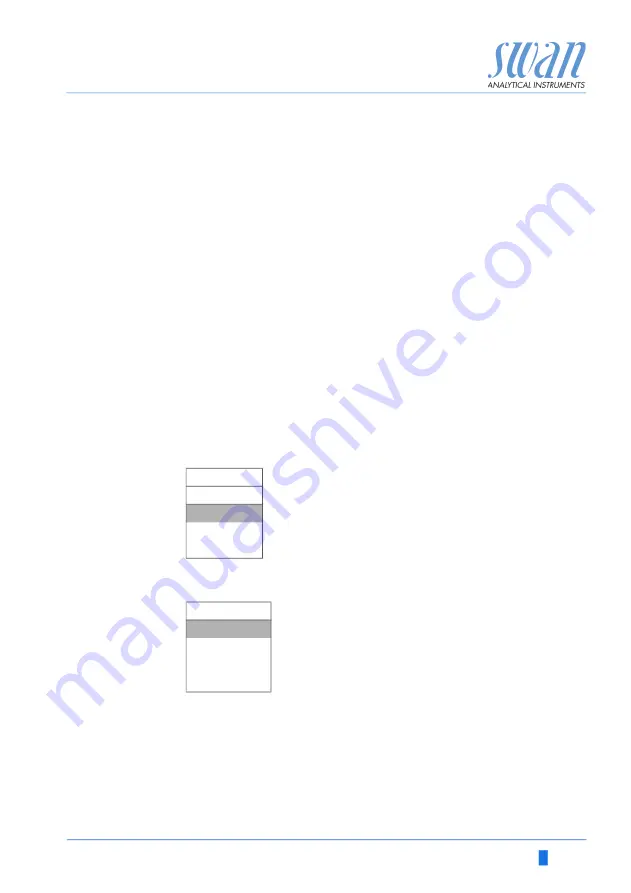
AMI Turbitrace
Program List and Explanations
A-96.250.131 / 050220
69
5.3.4.3
Output/Control:
(relay or signal output):
5.3.4.4
Fault:
5.3.4.5
Delay:
Time which the instrument waits, after the input is deactivat
-
ed, before returning to normal operation.
Range: 0–6‘000 Sec
5.4 Miscellaneous
5.4.1
Language:
Set the desired language.
5.4.2
Set defaults:
Reset the instrument to factory default values in three
different ways:
Calibration
: Sets calibration values back to default. All other
values are kept in memory.
In parts
: Communication parameters are kept in memory. All
other values are set back to default values.
Completely
: Sets back all values including communication
parameters.
Continuous:
Controller continues normally.
Hold:
Controller continues based on the last valid value.
Off:
Controller is switched off.
No:
No message is issued in pending error list and the
alarm relay does not close when input is active.
Message E024 is stored in the message list.
Yes:
Message E024 is issued and stored in the mes
-
sage list. The Alarm relay closes when input is
active.
Language
German
English
French
Spanish
Set defaults
no
Calibration
In parts
Completely