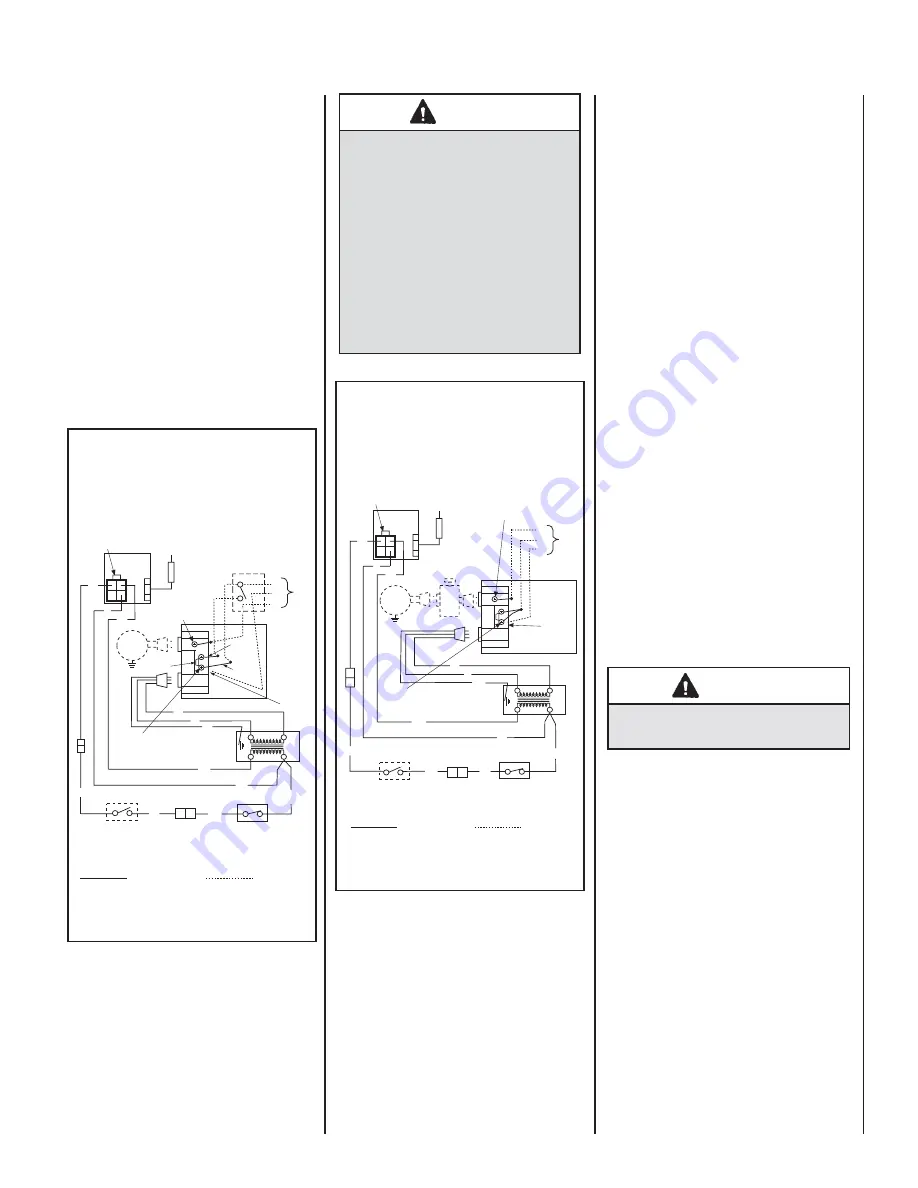
1. If any of the original wire as supplied must be replaced,
1.
it must be replaced with
Type AWM 105
°
C – 18 GA. wire.
2. 120V, 60Hz – Less than 3 amps.
BK
Junction Box
Transf.
120 V.
24 V
Factory Wired
Field Wired
BL
Electronic Wiring Diagram (Honeywell)
Showing the Blower Wiring for the Optional
FBK-100 and FBK-200 Kits
R
W
BL
OPT
BLOWER
G
W
*OPTIONAL
ACCESSORY
SWITCH
120
VAC.
BK
W
Gas Valve
B
R
IGNITER
PILOT
ASSEMBLY
Break Off
Tab
BK
G
*Blower speed control switch is provided in FBK200 blower kit.
Outlet Box
Green Ground
Screw
Hot side of Outlet
Schematic Representation Only
**ON/OFF Switch (Integral
with Gas Valve)
**Leave the ON/OFF switch, which is integral
with the gas valve, in the ON position.
Red
pigtail
Black
pigtail
White Wire
to Opposite
Side
G
LIMIT SWITCH
OPTIONAL WALL SWITCH
OR OPTIONAL THERMOSTAT OR
OPTIONAL REMOTE RECEIVER
BK
BK
1. If any of the original wire as supplied must be replaced,
1.
it must be replaced with
Type AWM 105
°
C – 18 GA. wire.
2. 120V, 60Hz – Less than 3 amps.
BK
Junction Box
Transf.
120 V.
24 V
Factory Wired
Field Wired
BL
Electronic Wiring Diagram (Honeywell)
Showing the Blower Wiring for the Optional
FBK-250 Kits
R
BL
OPT
BLOWER
G
W
120
VAC.
BK
W
Gas Valve
B
R
IGNITER
PILOT
ASSEMBLY
BK
Outlet Box Green
Ground Screw
Hot side of Outlet
Schematic Representation Only
*ON/OFF Switch (Integral
with Gas Valve)
White Wire
To Opposite
Side
Optional FBK-250
Module
*Leave the ON/OFF switch, which is integral
with the gas valve, in the ON position.
OPTIONAL ON/OFF SWITCH,
WALL SWITCH, THERMOSTAT
OR REMOTE CONTROL RECEIVER
G
W
LIMIT SWITCH
BK
BK
Step 6. WIRING -
OPTIONAL FORCED AIR BLOWER KIT
FBK-100, FBK-200 and FBK250 Kits
(See Figure 17 for FBK-100, FBK-200 and
Figure 18
for FBK-250 wiring)
-
An electrical outlet box (receptacle) is factory
-provided for the installation of the
FBK-100
,
FBK-200 and FBK-250
forced air blower kits.
(An optional fi eld-provided outletbox/J-Box
may also be used. Electrical power must be
connected to either of these receptacles in order
to operate these blowers. Install the blower
kits according to the installation instructions
provided with the kits.
Note: The tab connecting the receptacles of
the outlet box must be broken in FBK-100
and FBK-200 blower kit applications.
NOTE: DIAGRAMS & ILLUSTRATIONS NOT TO SCALE.
11
CAUTION
Ground supply lead must be con-
nected to the wire attached to the
green ground screw located on the
outlet box. See
Figures 17 & 18
. Fail-
ure to do so will result in a potential
safety hazard. The appliance must be
electrically grounded in accordance
with local codes or, in the absence of
local codes, the National Electrical
Code, ANSI/NFPA 70-latest edition.
(In Canada, the current CSA C22-1
Canadian Electrical Code).
Make gas line connections. All codes require a
shut-off valve mounted in the supply line.
Figure
19
illustrates two methods for connecting the
gas supply. The fl ex-line method is acceptable
in the U.S., however, Canadian requirements
vary depending on locality. Installation must
be in compliance with local codes.
These appliances are equipped with a gas fl ex
line for use (where permitted) in connecting
the appliance to the gas line. A gas fl ex line
is provided to aid in attaching the direct vent
appliance to the gas supply. The gas fl ex line
can only be used where local codes permit. See
Figure 19
for fl ex line description. The fl ex line
is rated for both natural gas and propane gas.
A manual shut off valve is also provided with
the fl ex line.
The incoming gas line should be piped into
the valve compartment and connected (see
Figures 19 & 20
). The millivolt control
valve has a 3/8" (10 mm) NPT thread
inlet port. The electronic control valve
has a 1/2" (13 mm) NPT thread inlet port
and is fi tted with a 1/2" x 3/8" (13 mm x
10 mm) NPT fi tting.
Secure all joints tightly using appropriate
tools and sealing compounds (ensure propane
resistant compounds are used in propane
applications).
Optional: Seal around the gas line to prevent
cold air leakage.
Step 7. CONNECTING GAS LINE
Figure 18
Turn on gas supply and test for gas leaks using a
gas leak test solution (also referred to as bubble
leak solution).
Note:
Using a soapy water solution
(50% dish soap, 50% water) is an effective leak
test solution but it is not recommended, because
the soap residue that is left on the pipes/fi ttings
can result in corrosion over time.
A. Light the appliance (refer to the lighting
instructions label in control compartment or
homeowner's manual).
B. Brush all joints and connections with the gas
leak test solution to check for leaks. If bubbles
are formed, or gas odor is detected, turn the
gas control knob (off/pilot/on) to the “OFF”
position. Either tighten or refasten the leaking
connection, then retest as described above.
C. When the gas lines are tested and leak free be
sure to rinse off the leak testing solution,
D. Turn on burner then observe the individual
tongues of fl ame on the burner. Make sure
all ports are open and producing fl ame evenly
across the burner. If any ports are blocked, or
partially blocked, clean out the ports.
WARNING
Never use an open fl ame to check
for leaks.
Figure 17
TEST ALL CONNECTIONS FOR GAS LEAKS
(FACTORY AND FIELD):
f i r e - p a r t s . c o m