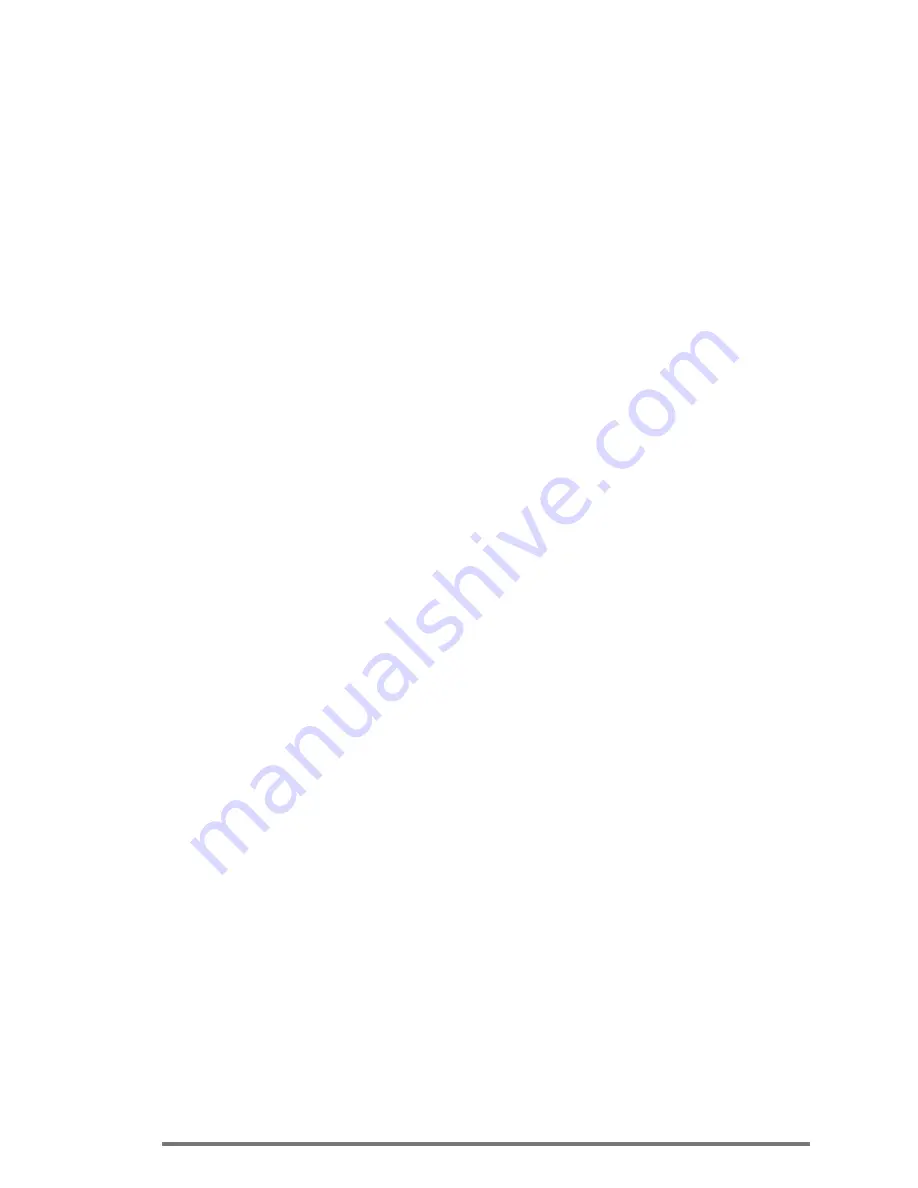
4. Test Area Requirements
4.1.
General requirements ................................................................................ 5
4.2.
Room ......................................................................................................... 5
4.2.1.
Room size .................................................................................................... 5
4.2.2.
Room positioning .......................................................................................... 6
4.2.3.
Room layout ................................................................................................. 6
4.3.
Safety and environmental issues ............................................................... 7
4.3.1.
Safety ........................................................................................................... 7
4.3.2.
Environmental ............................................................................................... 7
4.4.1.
Problem statement ....................................................................................... 8
4.4.2.
Air supply ..................................................................................................... 8
4.4.3.
Vehicle cooling .............................................................................................. 9
4.4.4.
Exhaust extraction ...................................................................................... 10
4.4.6.
Compressed air supply ............................................................................... 11
4.4.7.
Electrical power .......................................................................................... 11
4.4.8.
cell controls and monitoring ........................................................................ 11
4.4.9.
Convenience issues .................................................................................... 11
4.5.
Further reading ........................................................................................ 12
4.6.
Sample testcell calculations .................................................................... 13
4.7.
Installation drawings ................................................................................ 13
Summary of Contents for AutoDyn
Page 4: ...AutoDyn Operators Manual Section 1 Page 4 AutoDyn Cover fm...
Page 5: ...1 General Information...
Page 10: ...S Y S T E M O V E R V I E W Section 2 Page 1 2 System Overview...
Page 24: ...P A C K A G I N G A N D H A N D L I N G Section 3 page 1 Packaging and Handling 3...
Page 29: ...T E S T A R E A R E Q U I R E M E N T S Section 4 page 1 4 Test Area Requirements...
Page 40: ...I N S T A L L A T I O N Section 5 Page 1 5 Installation...
Page 55: ...6 System Operation...
Page 60: ......
Page 78: ...H A N D H E L D C O N T R O L L E R Section 7 Page 1 7 Handheld Controller...
Page 104: ...8 Theory Of Testing...
Page 123: ...9 Description of the Configuration File...
Page 172: ...20 Service and Calibration...
Page 178: ...S E R V I C E A N D C A L I B R A T I O N Section 20 page 7 20 2 Maintenance record...
Page 193: ...A General Testing Information Appendix...
Page 205: ...B Fundamental Concepts to Obtaining Superior Repeatability Appendix...