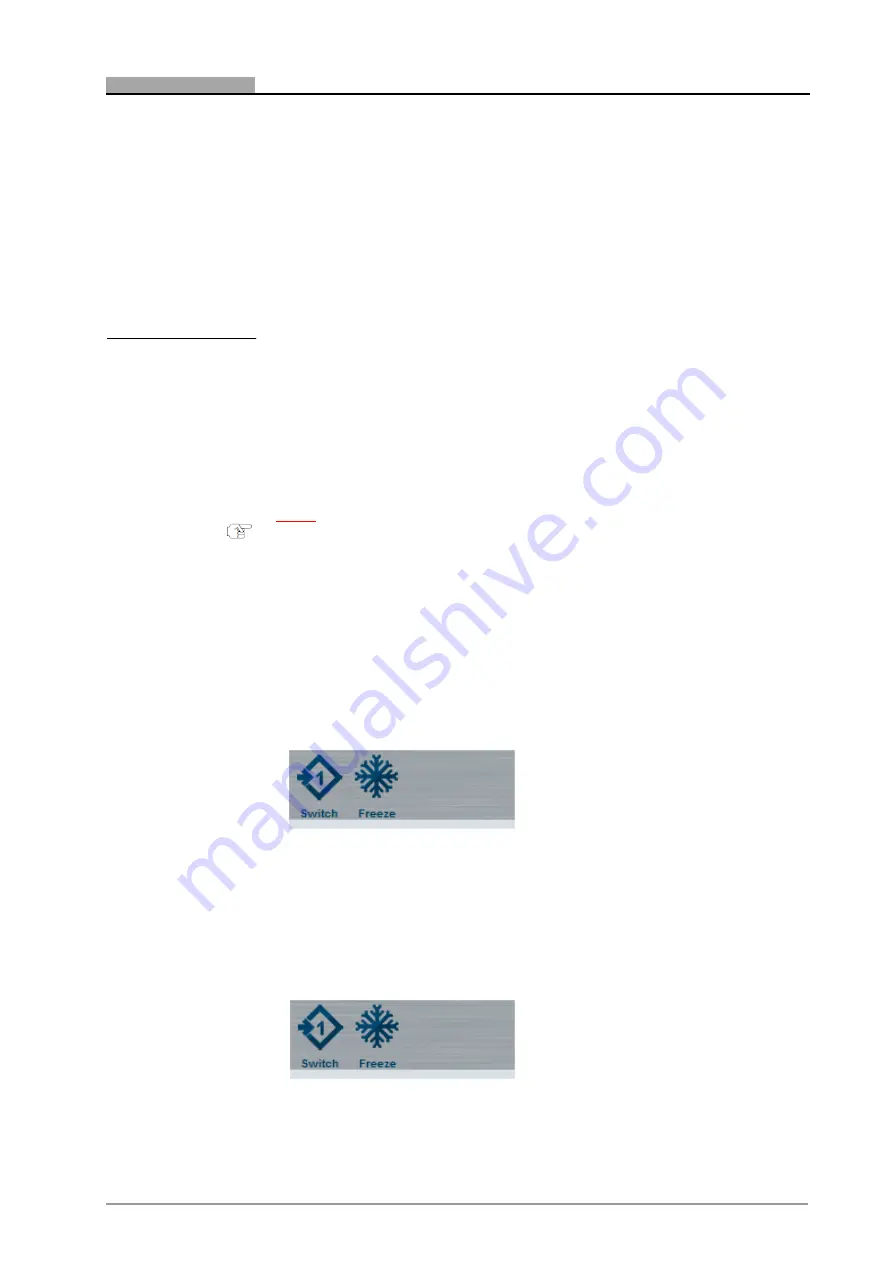
After the test data for Limit Set 2 has been stored the
“Toggle Limit
Sets” button will show that Limit Set 1 has been automatically
reselected and the indicator bands will change accordingly. A figure
“2” will appear in the toolbar, confirming that data is stored in data
buffer 2.
The data stored in the data buffers can be reviewed, printed or deleted
via the
8.6 Storing Data in the Data Buffers
Current test readings to which a Limit Set has been applied may be
temporarily stored in one of the two data buffers. This temporary storage
allows the second Limit Set to be applied without the loss of the initial
test results. Data to which Limit Set 1 is applied will be stored in buffer 1
and data to which Limit Set 2 is applied will be stored in buffer 2.
Note:
The following description assumes that the Free Measurement
Procedure is performed as outlined in
(i.e. the data to which Limit Set 1 has been applied is to be
stored before Limit Set 2 is applied). Although this will be the usual
procedure, it should be noted that it is possible to apply Limit Set 2
before Limit Set 1 or to apply either Limit Set independently.
To store data in data buffer 1:
•
Apply Limit Set 1 using the
“Toggle Limit Set” button .
Figure 8-7
Apply Limit Set 1
•
Take the Limit Set 1 gas measurements as outlined in
•
Press the “Freeze” toolbar button.
Figure 8-8
Freeze Limit Set 1 Readings
48
S
TORING
D
ATA IN THE
D
ATA
B
UFFERS
Summary of Contents for DGA 5000
Page 1: ...EMISSIONS DIAGNOSTIC PLATFORM Operator s Manual HIGH TECH SECURES YOUR FUTURE...
Page 2: ......
Page 5: ......
Page 9: ...vi...
Page 13: ...4 C H A P T E R 1...
Page 15: ...6 C H A P T E R 2...
Page 24: ...15 C H A P T E R 4...
Page 46: ...37 C H A P T E R 7...
Page 81: ...C H A P T E R 10 MAINTENANCE 72...
Page 84: ......