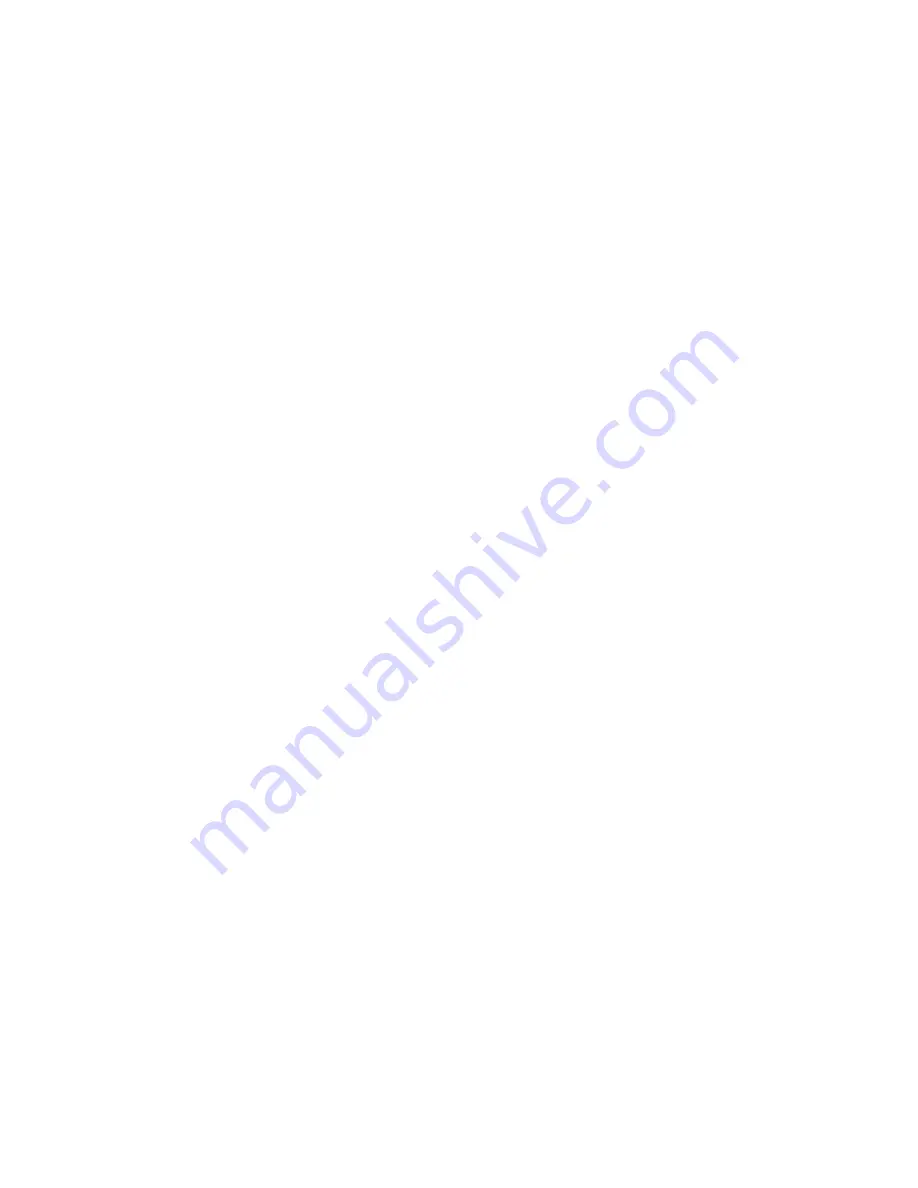
Section 1
SAFETY
3
G.
If air line anti--icer system antifreeze compound
enters the eyes or if fumes irritate the eyes, they
should be washed with large quantities of clean wa-
ter for 15 minutes. A physician, preferably an eye
specialist, should be contacted immediately.
H. DO NOT
store air line anti--icer system antifreeze
compound in confined areas.
I.
The antifreeze compound used in air line anti-
freeze systems contains methanol and is toxic,
harmful, or fatal if swallowed. Avoid contact with the
skin or eyes and avoid breathing the fumes. If swal-
lowed, induce vomiting by administering a table-
spoon of salt, in each glass of clean, warm water un-
til vomit is clear, then administer two teaspoons of
baking soda in a glass of clean water. Have patient
lay down and cover eyes to exclude light. Call a phy-
sician immediately.
1.8 ELECTRICAL SHOCK
A.
This compressor should be installed and main-
tained in full compliance with all applicable Federal,
State and Local codes, standards and regulations,
including those of the National Electrical Code, and
also including those relative to equipment grounding
conductors, and only by personnel that are trained,
qualified and delegated to do so.
B.
Keep all parts of the body and any hand--held
tools or other conductive objects away from ex-
posed live parts of electrical system. Maintain dry
footing, stand on insulating surfaces and
DO NOT
contact any other portion of the compressor when
making adjustments or repairs to exposed live parts
of the electrical system. Make all such adjustments
or repairs with one hand only, so as to minimize the
possibility of creating a current path through the
heart.
C.
Attempt repairs in clean, dry and well lighted and
ventilated areas only.
D. DO NOT
leave the compressor unattended with
open electrical enclosures. If necessary to do so,
then disconnect, lock out and tag all power at source
so others will not inadvertently restore power.
E.
Disconnect, lock out, and tag all power at source
prior to attempting repairs or adjustments to rotating
machinery and prior to handling any ungrounded
conductors.
1.9 LIFTING
A.
If the compressor is provided with a lifting bail,
then lift by the bail provided. If no bail is provided,
then lift by sling. Compressors to be air lifted by heli-
copter must not be supported by the lifting bail but by
slings instead. In any event, lift and/or handle only in
full compliance with OSHA standards 29 CFR 1910
subpart N.
B.
Inspect points of attachment for cracked welds
and for cracked, bent, corroded or otherwise de-
graded members and for loose bolts or nuts prior to
lifting.
C.
Make sure entire lifting, rigging and supporting
structure has been inspected, is in good conditions
and has a rated capacity of at least the weight of the
compressor. If you are unsure of the weight, then
weigh compressor before lifting.
D.
Make sure lifting hook has a functional safety
latch or equivalent, and is fully engaged and latched
on the bail or slings.
E.
Use guide ropes or equivalent to prevent twisting
or swinging of the compressor once it has been lifted
clear of the ground.
F. DO NOT
attempt to lift in high winds.
G.
Keep all personnel out from under and away from
the compressor whenever it is suspended.
H.
Lift compressor no higher than necessary.
I.
Keep lift operator in constant attendance whenev-
er compressor is suspended.
J.
Set compressor down only on level surfaces ca-
pable of safely supporting at least its weight and its
loading unit.
K.
When moving compressors by forklift truck, uti-
lize fork pockets if provided. Otherwise, utilize pallet
if provided. If neither fork pockets or pallet are pro-
vided, then make sure compressor is secure and
well balanced on forks before attempting to raise or
transport it any significant distance.
L.
Make sure forklift truck forks are full engaged and
tipped back prior to lifting or transporting the com-
pressor.
M.
Forklift no higher than necessary to clear ob-
stacles at floor level and transport and corner at
minimum practical speeds.
N.
Make sure pallet mounted compressors are firm-
ly bolted or otherwise secured to the pallet prior to
attempting to forklift or transport them.
NEVER
at-
tempt to forklift a compressor that is not secured to
its pallet, as uneven floors or sudden stops may
cause the compressor to tumble off, possibly caus-
ing serious injury or property damage in the process.
Summary of Contents for 20/12 500 CFM
Page 12: ...Section 2 DESCRIPTION 8 Figure 2 3 Piping and Instrumentation...
Page 14: ...Section 2 DESCRIPTION 10 Figure 2 5 Capacity Control System Typical...
Page 18: ...14 NOTES...
Page 20: ...16 NOTES...
Page 24: ...20 NOTES...
Page 38: ...34 NOTES...
Page 40: ...Section 7 ILLUSTRATIONS AND PARTS LIST 36 7 3 MOTOR FRAME COMPRESSOR AND PARTS...
Page 42: ...Section 7 ILLUSTRATIONS AND PARTS LIST 38 7 4 AIR INLET SYSTEM...
Page 44: ...Section 7 ILLUSTRATIONS AND PARTS LIST 40 7 5 COOLING AND LUBRICATION SYSTEM...
Page 46: ...Section 7 ILLUSTRATIONS AND PARTS LIST 42 7 6 COOLER ASSEMBLY...
Page 48: ...Section 7 ILLUSTRATIONS AND PARTS LIST 44 7 7 DISCHARGE SYSTEM...
Page 50: ...Section 7 ILLUSTRATIONS AND PARTS LIST 46 7 7 DISCHARGE SYSTEM...
Page 52: ...Section 7 ILLUSTRATIONS AND PARTS LIST 48 7 8 INSTRUMENT PANEL AND PARTS...
Page 54: ...Section 7 ILLUSTRATIONS AND PARTS LIST 50 7 9 CONTROL SYSTEM...
Page 56: ...Section 7 ILLUSTRATIONS AND PARTS LIST 52 7 9 CONTROL SYSTEM...
Page 58: ...Section 7 ILLUSTRATIONS AND PARTS LIST 54 7 10 ELECTRIC CONTROL BOX...
Page 60: ...Section 7 ILLUSTRATIONS AND PARTS LIST 56 7 11 UNIT TUBING...
Page 62: ...Section 7 ILLUSTRATIONS AND PARTS LIST 58 7 11 UNIT TUBING...
Page 64: ...Section 7 ILLUSTRATIONS AND PARTS LIST 60 7 12 DECAL GROUP...