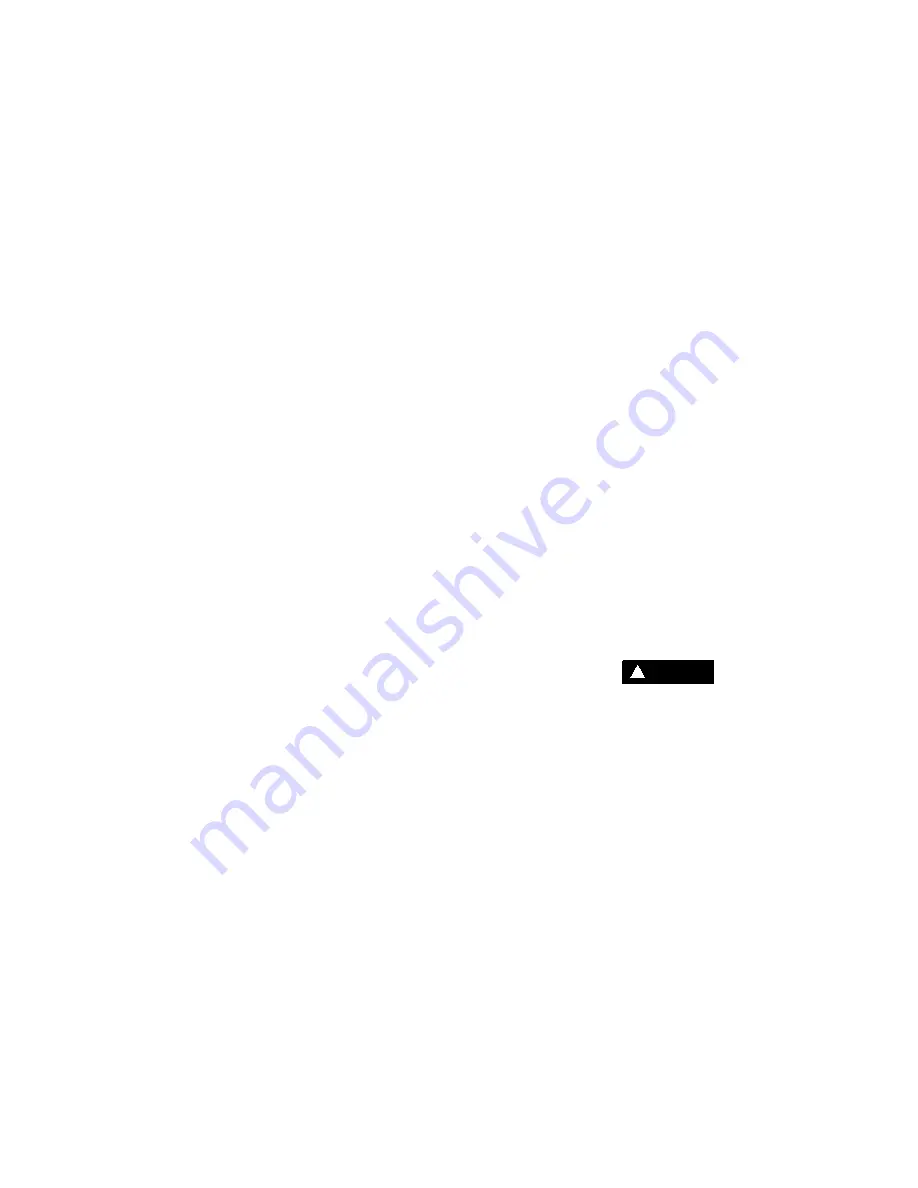
Section 1
SAFETY
2
on any external surfaces of the air compressor or on
internal surfaces of the enclosure. Wipe down using
an aqueous industrial cleaner or steam clean as re-
quired. If necessary, remove acoustical material,
clean all surfaces and then replace acoustical mate-
rial. Any acoustical material with a protective cover-
ing that has been torn or punctured should be re-
placed immediately to prevent accumulation of liq-
uids or fluid film within the material
. DO NOT
use
flammable solvents for cleaning purposes.
D.
Disconnect and lock out all power at source prior
to attempting any repairs or cleaning of the com-
pressor or of the inside of the enclosure, if any.
E.
Keep electrical wiring, including all terminals and
pressure connectors in good condition. Replace any
wiring that has cracked, cut abraded or otherwise
degraded insulation, or terminals that are worn, dis-
colored or corroded. Keep all terminals and pres-
sure connectors clean and tight.
F.
Keep grounded and/or conductive objects such
as tools away from exposed live electrical parts
such as terminals to avoid arcing which might serve
as a source of ignition.
G.
Remove any acoustical material or other material
that may be damaged by heat or that may support
combustion and is in close proximity, prior to at-
tempting weld repairs.
H.
Keep suitable fully charged Class BC or ABC fire
extinguisher or extinguishers nearby when servicing
and operating the compressor.
I.
Keep oily rags, trash, leaves, litter or other com-
bustibles out of and away from the compressor.
J. DO NOT
operate the compressor without proper
flow of cooling air or water or with inadequate flow of
lubricant or with degraded lubricant.
K. DO NOT
attempt to operate the compressor in
any classification of hazardous environment unless
the compressor has been specially designed and
manufactured for that duty.
1.5 MOVING PARTS
A.
Keep hands, arms and other parts of the body
and also clothing away from couplings, fans and oth-
er moving parts.
B. DO NOT
attempt to operate the compressor with
the fan, coupling or other guards removed.
C.
Wear snug fitting clothing and confine long hair
when working around this compressor, especially
when exposed to hot or moving parts.
D.
Keep access doors, if any, closed except when
making repairs or adjustments.
E.
Make sure all personnel are out of and/or clear of
the compressor prior to attempting to start or oper-
ate it.
F.
Disconnect and lock out all power at source and
verify at the compressor that all circuits are de--en-
ergized to minimize the possibility of accidental
start--up or operation, prior to attempting repairs or
adjustments. This is especially important when
compressors are remotely controlled.
G.
Keep hands, feet, floors, controls and walking
surfaces clean and free of fluid, water, or other liq-
uids to minimize the possibility of slips and falls.
1.6 HOT SURFACES, SHARP EDGES AND SHARP
CORNERS
A.
Avoid bodily contact with hot fluid, hot coolant,
hot surfaces and sharp edges and corners.
B.
Keep all parts of the body away from all points of
air discharge.
C.
Wear personal protective equipment including
gloves and head covering when working in, on or
around the compressor.
D.
Keep a first aid kit handy. Seek medical assis-
tance promptly in case of injury.
DO NOT
ignore
small cuts and burns as they may lead to infection.
1.7 TOXIC AND IRRITATING SUBSTANCES
A. DO NOT
use air from this compressor for respira-
tion (breathing) except in full compliance with OSHA
Standards 29 CFR 1910 and any other Federal,
State or Local Codes or regulations.
DANGER
!
Death or serious injury can result from inhaling
compressed air without using proper safety
equipment. See OSHA standards on safety equip-
ment.
B. DO NOT
use air line anti--icer systems in air lines
supplying respirators or other breathing air utiliza-
tion equipment and
DO NOT
discharge air from
these systems in unventilated or other confined
areas.
C.
Operate the compressor only in open or ade-
quately ventilated areas.
D.
Locate the compressor or provide a remote inlet
so that it is not likely to ingest exhaust fumes or other
toxic, noxious or corrosive fumes or substances.
E.
Coolants and lubricants used in this compressor
are typical of the industry. Care should be taken to
avoid accidental ingestion and/or skin contact. In
the event of ingestion, seek medical treatment
promptly. Wash with soap and water in the event of
skin contact.
F.
Wear goggles or a full face shield when adding an-
tifreeze compound to air line anti--icer systems.
Summary of Contents for 20/12 500 CFM
Page 12: ...Section 2 DESCRIPTION 8 Figure 2 3 Piping and Instrumentation...
Page 14: ...Section 2 DESCRIPTION 10 Figure 2 5 Capacity Control System Typical...
Page 18: ...14 NOTES...
Page 20: ...16 NOTES...
Page 24: ...20 NOTES...
Page 38: ...34 NOTES...
Page 40: ...Section 7 ILLUSTRATIONS AND PARTS LIST 36 7 3 MOTOR FRAME COMPRESSOR AND PARTS...
Page 42: ...Section 7 ILLUSTRATIONS AND PARTS LIST 38 7 4 AIR INLET SYSTEM...
Page 44: ...Section 7 ILLUSTRATIONS AND PARTS LIST 40 7 5 COOLING AND LUBRICATION SYSTEM...
Page 46: ...Section 7 ILLUSTRATIONS AND PARTS LIST 42 7 6 COOLER ASSEMBLY...
Page 48: ...Section 7 ILLUSTRATIONS AND PARTS LIST 44 7 7 DISCHARGE SYSTEM...
Page 50: ...Section 7 ILLUSTRATIONS AND PARTS LIST 46 7 7 DISCHARGE SYSTEM...
Page 52: ...Section 7 ILLUSTRATIONS AND PARTS LIST 48 7 8 INSTRUMENT PANEL AND PARTS...
Page 54: ...Section 7 ILLUSTRATIONS AND PARTS LIST 50 7 9 CONTROL SYSTEM...
Page 56: ...Section 7 ILLUSTRATIONS AND PARTS LIST 52 7 9 CONTROL SYSTEM...
Page 58: ...Section 7 ILLUSTRATIONS AND PARTS LIST 54 7 10 ELECTRIC CONTROL BOX...
Page 60: ...Section 7 ILLUSTRATIONS AND PARTS LIST 56 7 11 UNIT TUBING...
Page 62: ...Section 7 ILLUSTRATIONS AND PARTS LIST 58 7 11 UNIT TUBING...
Page 64: ...Section 7 ILLUSTRATIONS AND PARTS LIST 60 7 12 DECAL GROUP...