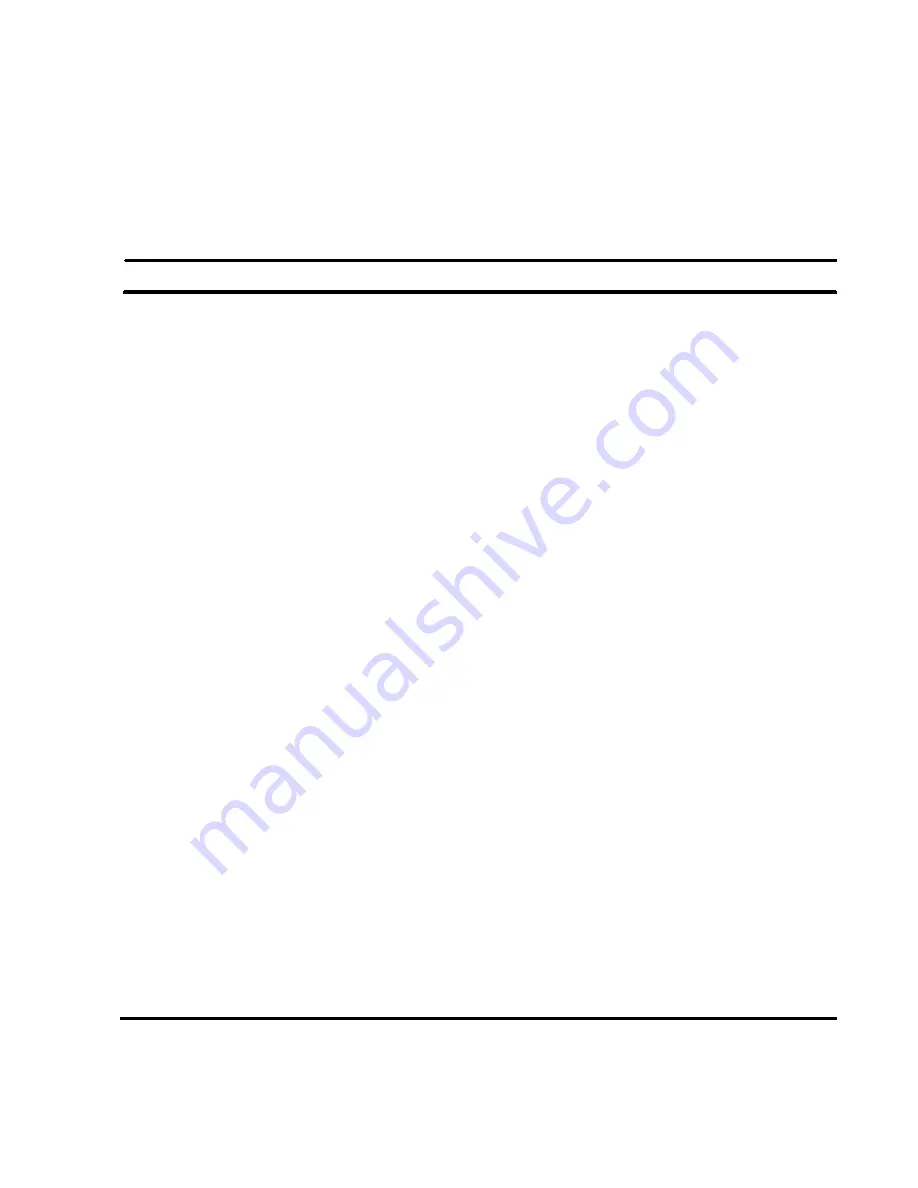
Section 5
OPERATION
17
5.1 GENERAL
While Sullair has built into this compressor a com-
prehensive array of controls and indicators to as-
sure you that it is operating properly, you will want
to recognize and interpret the reading which will call
for service or indicate the beginning of a malfunc-
tion. Before starting your Sullair compressor, read
this section thoroughly and familiarize yourself with
the controls and indicators -- their purpose, location
and use.
5.2 PURPOSE OF CONTROLS
CONTROL OR INDICATOR
PURPOSE
START PUSHBUTTON
Depress to turn the compressor ON.
HOURMETER
Records the cumulative hours of compressor opera-
tion; useful for planning and logging service sched-
ules.
LINE PRESSURE GAUGE
Continually monitors service line air pressure. Located
on dry side of receiver downstream from check valve.
SUMP PRESSURE GAUGE
Continually monitors receiver/sump pressure at vari-
ous load and/or unloaded conditions.
DISCHARGE TEMPERATURE GAUGE
Monitors temperature of the air leaving the compres-
sor unit. The normal reading should be approximately
230
_
F (110
_
C ).
BEARING FILTER MAINTENANCE
Indicates when a bearing filter element change is
INDICATOR
required. Shows red when the pressure drop
through the filter is excessive.
SEPARATOR MAINTENANCE INDICATOR
Indicates when separator element change is required.
Shows red when the pressure drop through the filter is
excessive. The separator must be replaced.
DO NOT
CLEAN.
FLUID LEVEL SIGHT GLASS
Monitors fluid level in the sump. Proper level is to fill the
sight glass.
FLUID RETURN LINE SIGHT GLASS
Used to indicate fluid flow in the return line. When the
compressor is running at full load, fluid flow should be
visible in this sight glass. There may be little or no flow
when the compressor is running unloaded, but a slug-
gish flow at full load indicates a need to clean the return
line strainer.
FLUID STOP VALVE
Cuts off flow of fluid to compressor unit at compressor
shutdown, and allows flow of fluid to unit on start--up.
DISCHARGE CHECK VALVE
Cuts off the reverse flow of air/fluid mixture through
compressor discharge system at compressor shut-
down.
THERMAL VALVE
Regulates flow of fluid to and around the cooler. De-
signed to maintain a maximum operating compressor
discharge temperature of 230
_
F (110
_
C ). Used for
fast warmup on start--up.
HIGH PRESSURE SHUTDOWN SWITCH
Designed to shut down the compressor when the pres-
sure becomes too high. This switch is set for 365 PSIG
(2515kPa).
Summary of Contents for 20/12 500 CFM
Page 12: ...Section 2 DESCRIPTION 8 Figure 2 3 Piping and Instrumentation...
Page 14: ...Section 2 DESCRIPTION 10 Figure 2 5 Capacity Control System Typical...
Page 18: ...14 NOTES...
Page 20: ...16 NOTES...
Page 24: ...20 NOTES...
Page 38: ...34 NOTES...
Page 40: ...Section 7 ILLUSTRATIONS AND PARTS LIST 36 7 3 MOTOR FRAME COMPRESSOR AND PARTS...
Page 42: ...Section 7 ILLUSTRATIONS AND PARTS LIST 38 7 4 AIR INLET SYSTEM...
Page 44: ...Section 7 ILLUSTRATIONS AND PARTS LIST 40 7 5 COOLING AND LUBRICATION SYSTEM...
Page 46: ...Section 7 ILLUSTRATIONS AND PARTS LIST 42 7 6 COOLER ASSEMBLY...
Page 48: ...Section 7 ILLUSTRATIONS AND PARTS LIST 44 7 7 DISCHARGE SYSTEM...
Page 50: ...Section 7 ILLUSTRATIONS AND PARTS LIST 46 7 7 DISCHARGE SYSTEM...
Page 52: ...Section 7 ILLUSTRATIONS AND PARTS LIST 48 7 8 INSTRUMENT PANEL AND PARTS...
Page 54: ...Section 7 ILLUSTRATIONS AND PARTS LIST 50 7 9 CONTROL SYSTEM...
Page 56: ...Section 7 ILLUSTRATIONS AND PARTS LIST 52 7 9 CONTROL SYSTEM...
Page 58: ...Section 7 ILLUSTRATIONS AND PARTS LIST 54 7 10 ELECTRIC CONTROL BOX...
Page 60: ...Section 7 ILLUSTRATIONS AND PARTS LIST 56 7 11 UNIT TUBING...
Page 62: ...Section 7 ILLUSTRATIONS AND PARTS LIST 58 7 11 UNIT TUBING...
Page 64: ...Section 7 ILLUSTRATIONS AND PARTS LIST 60 7 12 DECAL GROUP...