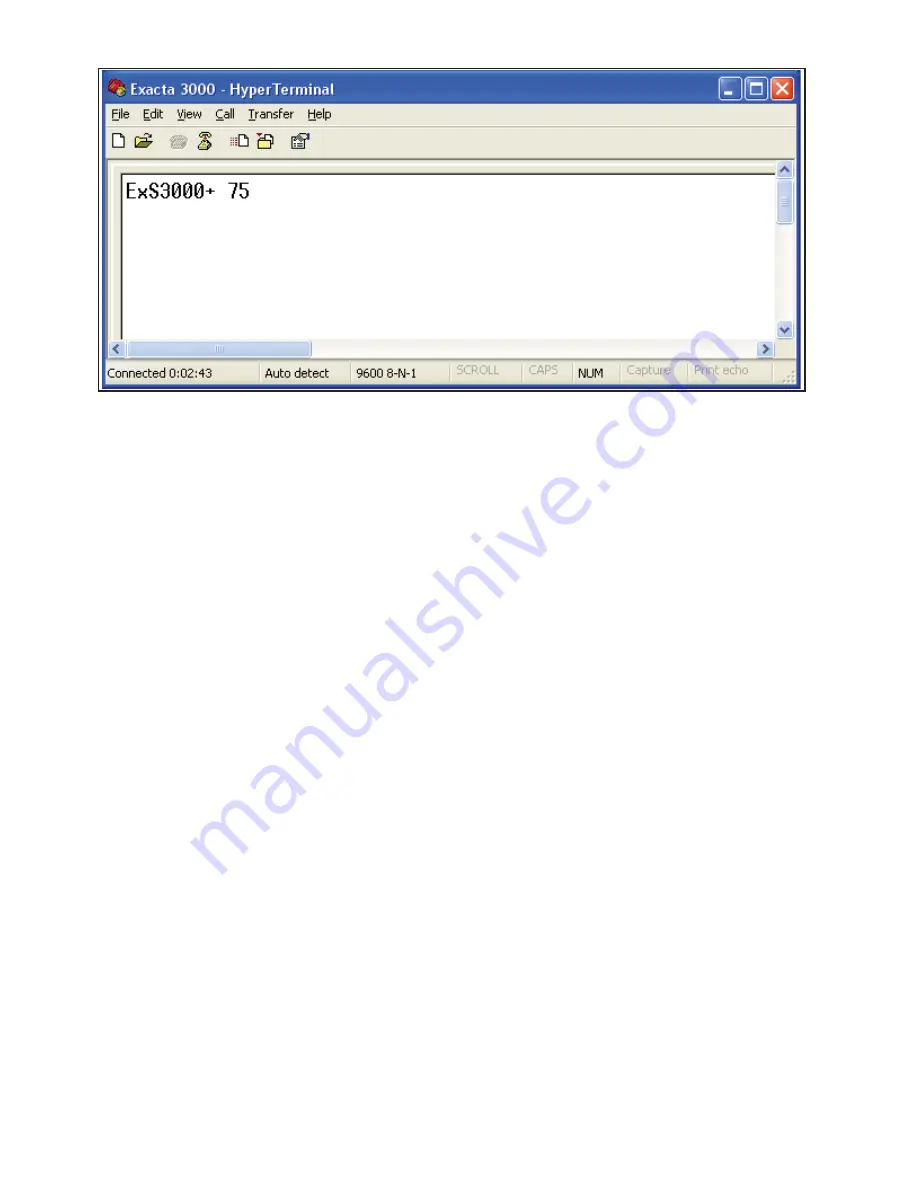
Sturtevant Richmont
- P/N 857285 - Issue Date 100407 - Page 9 of 14
5. Set the communication protocols within Hyperterminal to the following settings:
Baud Rate = 9600 baud (tool default baud rate at startup)
Data bits = 8
Stop bit = 1
Parity = None
Flow Control = none
6. Ensure that there is no torque load on the tool. Enable power to the tool and allow it to complete the
starting processes. Communication with the computer will be established and the tool will send the
fi rmware version and model information to the computer. In Hyperterminal, the information will appear
approximately as it does in the next image.
7. Type the diagnostic “D” Command into the terminal and press <enter>. The Terminal display will dis-
play “DiaOn”. You are now in diagnostic mode.
8. Type the M <enter>. The capacity of the tool should be seen on the display.
9. To enter the Calibration process, press the ‘Select‘ button on the tool keypad.
Calibration Procedure Keypad Functions
•
Clear button – Restarts calibration process at Cal point CW 0.
•
Up Arrow – Selects calibration point to calibrate. Note: If pressed and held, the percent cal point will be
displayed. Upon release the tool will display:
- If under 1% of tool capacity the target torque value the cal point will be displayed.
- If over 1% of the tool capacity, the current torque value will be displayed.
•
Down arrow – Saves the new cal point and recalculates the current torque value.
•
Select button – Not used during this process