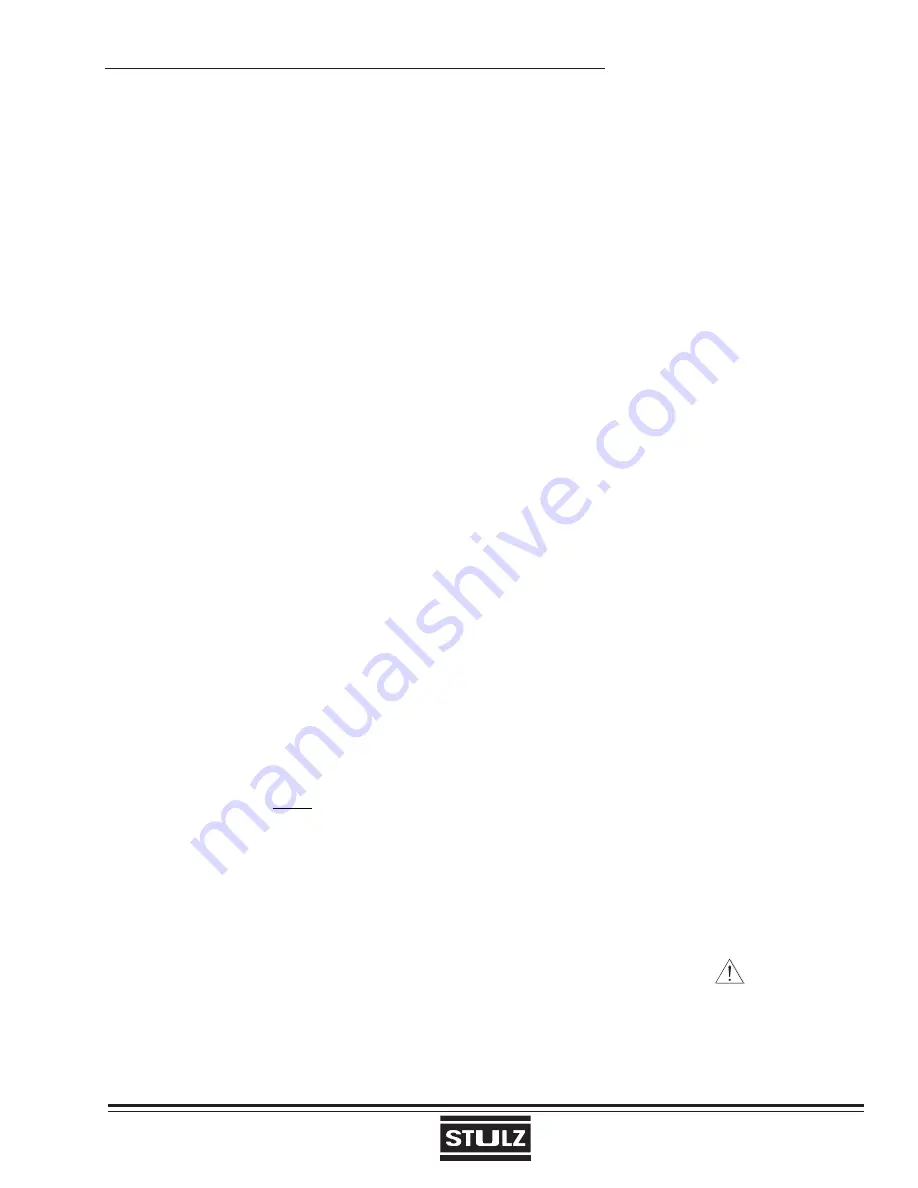
FLAiR Series Installation, Operation & Maintenance Manual
(©Aug, 2007)
Air Technology Systems, Inc.
2-16
refrigeration circuit to back up liquid refrigerant into the
condenser coil. The head pressure control valve is a 3-
way modulating valve controlled by the discharge
pressure.
When the A/C unit begins to operate, the discharge
pressure rises to 275 psig and the condenser fan is
cycled on as described in Section 2.8.4.1.1. When
ambient temperature drops, the discharge pressure
drops also. When the discharge pressure drops to
approximately 180 psig, the head pressure control
valve diverts discharge gas away from the condenser
to the receiver. Liquid flow from the condenser is
restricted, causing liquid to back up in the condenser.
Flooding the condenser reduces the area available for
condensing. The desired result is to increase the
pressure into the condenser, maintaining a minimum
discharge pressure during low ambient operation thus
ensuring proper condensing temperature. The head
pressure control valve requires no adjustment.
This method of controlling head pressure allows the
condenser fan to run continuously. While the fan is
running, the flooded head pressure control valve
modulates the amount of discharge gas entering the
receiver. As the pressure increases, the valve diverts
more discharge gas to the condenser, allowing more
liquid to flow from the condenser to the receiver.
When using this method of head pressure regulation
there must be enough refrigerant in the system to
ensure adequate charge at the lowest expected
ambient temperature in which the system will be
operating. A receiver is used to store the extra refriger-
ant when the condenser is not using it.
NOTE
Systems utilizing air cooled condensers, (AR mod-
els), must not have a refrigerant line pressure drop
over 14 psig across the condenser and the intercon-
necting piping to the condenser sections.
2.8.4.2
Water/Glycol-Cooled Systems
2.8.4.2.1 Head Pressure Regulating Valve
In a water/glycol condenser, condensing temperature
is maintained by the liquid flowing through a regulating
valve and then into a tube-in-tube or brazed plate
liquid-cooled condenser. The regulating valve opens to
increase water flow as the refrigerant pressure rises (or
closes as the refrigerant pressure falls). The regulating
valve is factory set for the correct condensing tempera-
ture, however, it can be adjusted to increase or
decrease the condensing temperature as follows:
Head pressure regulating valves are available in 2-way
or 3-way configurations. The location and method for
adjusting the valves for condensing pressure differs
with the valve types which can be differentiated by the
maximum water pressure rating of the valve, (150, 350,
or 450 psig).
2.8.4.2.1.1
150 psig Pressure Valves
Adjustment is made by turning the slotted square
stem on top of the valve clockwise to increase the
condensing temperature or decrease water/glycol flow
and counterclockwise to decrease the condensing
temperature or increase the water/glycol flow. A
directional arrow is stamped on the metal housing of
the valve stem.
2.8.4.2.1.2
350 psig and 450 psig
High Pressure Valves
Adjustment is made by turning the round-holed knob,
located inside the valve's metal housing counterclock-
wise to increase condensing pressure or decrease
water/glycol flow and clockwise to decrease the
condensing temperature or increase the water/glycol
flow. A directional arrow is stamped on the metal
housing of the valve stem.
2.8.5
Humidifier Adjustment
The humidifier has an adjustable capacity potentiom-
eter on the humidifier control circuit board. The
potentiometer may need to be field adjusted if the
humidifier is not supplying enough capacity for the
current room conditions.
It is recommended that if the humidifier capacity
potentiometer requires adjustment, the adjustment is
made in small increments and verified. Refer to the
humidifier manual sent with your unit for the capacity
potentiometer location.
CAUTION
Adjusting the capacity potentiometer too high
may result in the formation of condensate within
the system.
Summary of Contents for FLAIR series
Page 1: ...FLAiR Series Installation Operation Maintenance Manual Aug 2007 Air Technology Systems Inc ...
Page 42: ... Aug 2007 FLAiR Series Installation Operation Maintenance Manual Air Technology Systems Inc ...
Page 44: ... Aug 2007 FLAiR Series Installation Operation Maintenance Manual Air Technology Systems Inc ...
Page 46: ... Aug 2007 FLAiR Series Installation Operation Maintenance Manual Air Technology Systems Inc ...
Page 48: ... Aug 2007 FLAiR Series Installation Operation Maintenance Manual Air Technology Systems Inc ...