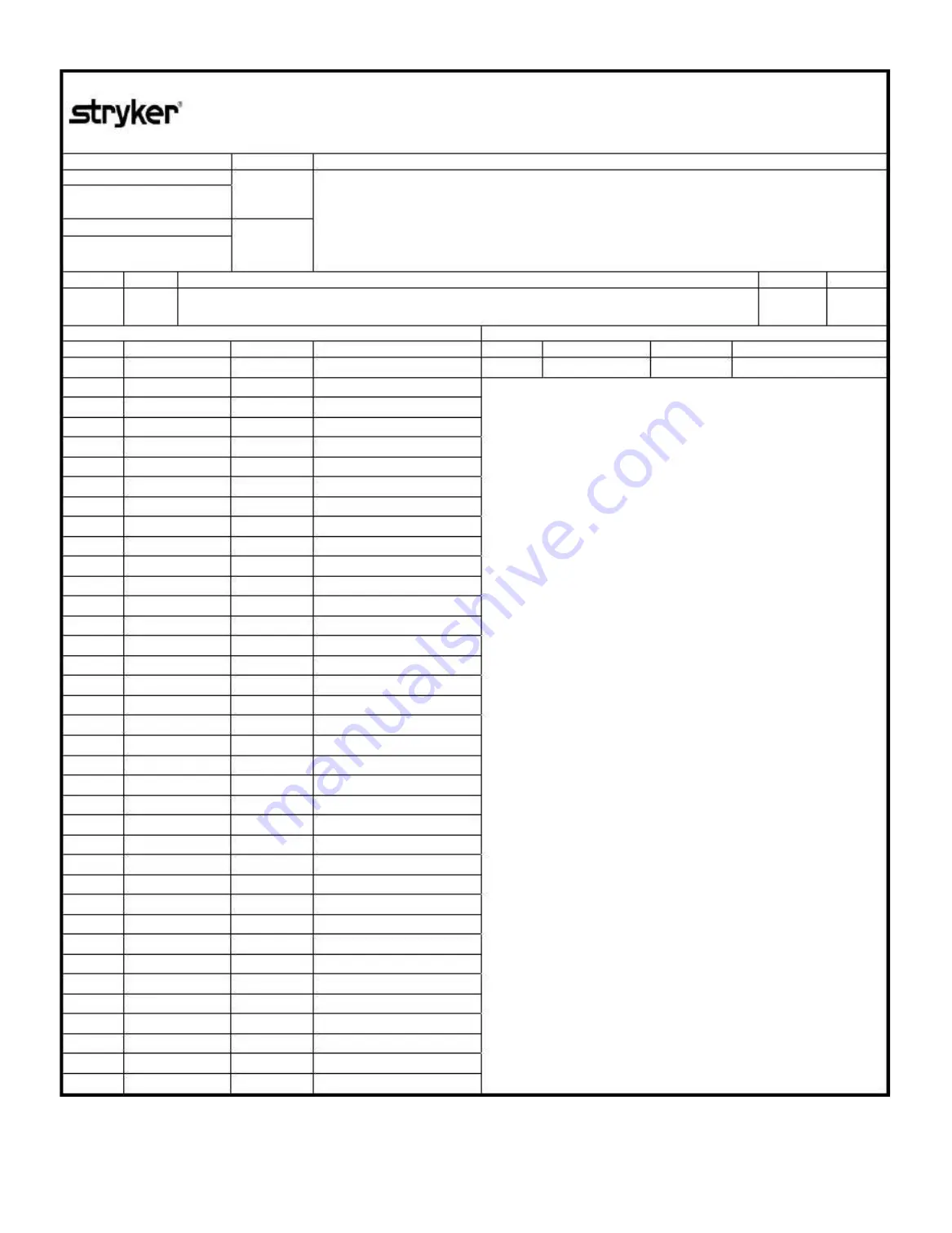
Stryker Endoscopy
Stryker Endoscopy
5900 Optical Court, San Jose, CA 95138
5900 Optical Court, San Jose, CA 95138
APPROVALS
APPROVALS
DATE
DATE
TITLE
TITLE
DRAWN BY:
DRAWN BY:
A. Infanger
A. Infanger
02/28/07
02/28/07
ORIGINATOR
ORIGINATOR
A. Infanger
A. Infanger
02/28/07
02/28/07
X8000 Light Source
X8000 Light Source
Service Guide
Service Guide
SIZE
SIZE
REV.
REV.
DOCUMENT
DOCUMENT NO.
NO.
SHEET
SHEET
OF
OF
A
A
A
A
1000-400-933
1000-400-933
1
1
71
71
REVISIONS
REVISIONS
REVISIONS
REVISIONS
LTR
ECN
LTR
ECN NO.
NO.
DATE
DATE
APPROVED
APPROVED
LTR
ECN
LTR
ECN NO.
NO.
DATE
DATE
APPROVED
APPROVED
A
A
ECO 104650
ECO 104650
02/28/07
02/28/07
A. Infanger
A. Infanger
B
B
C
C
D
D
E
E
F
F
G
G
H
H
J
J
K
K
L
L
M
M
N
N
P
P
R
R
T
T
U
U
V
V
W
W
Y
Y
Printing Instructions:
Printing Instructions:
1.
8.5
1.
8.5
!
!
11” portrait
11” portrait
2.
2.
Front
Front and
and back
back
3.
3.
Color
Color printing
printing
4.
4.
Select
Select binding
binding and
and paper
paper weight
weight based
based on
on cost
cost
Global Source:
Global Source:
Archive this doc
Archive this document as a s
ument as a service/repair guide
ervice/repair guide..
Summary of Contents for 220-200-000
Page 4: ......
Page 10: ...8 Bottom Chassis Assembly ...
Page 11: ...9 ...
Page 20: ...18 Control Board Diagrams ...
Page 70: ...68 ...
Page 71: ......