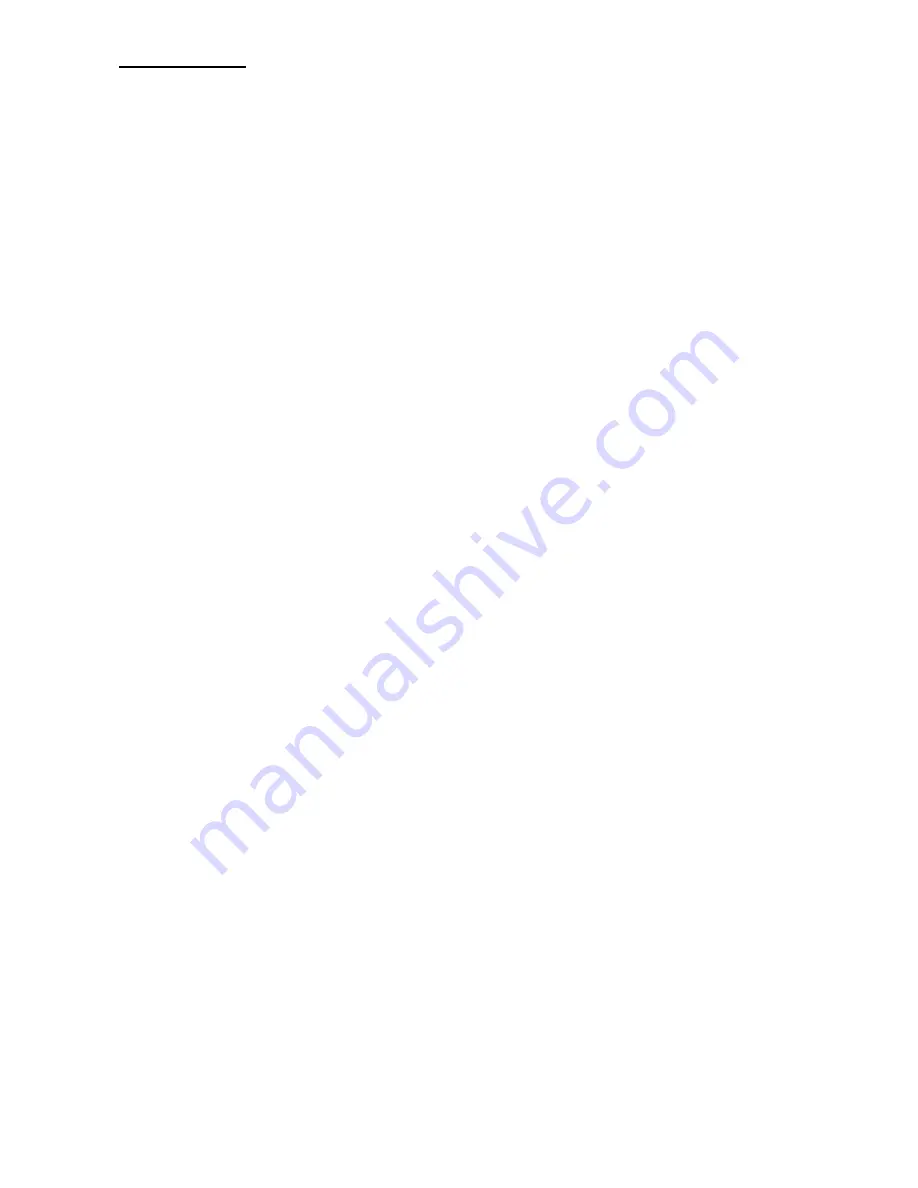
Page 8 of 51
4. INTRODUCTION
Warning
:
For trouble free operation of the boiler, and to be assured of the full guarantee, the following
items are required:
A.
An automatic air and dirt separator must be installed in the installation and a strainer in
the return also devices as shown on pages 5 or 6.
B.
Minimum static water pressure should be more than 0.5 bar.
C.
The system is flushed, water tested and additive utilised if required.
D.
Boiler auto air vent cap must be open and all system air vents open.
E.
Low and high water cut out pressure switches ( usually in the fill unit) connected in the
Boiler volt free control circuit in series with other controls on terminals 13 - 14 or by 0 volt
when using external 0 to 10 volt control by others.
F.
Control of Boiler on/off must never be by interruption of the mains supply.
G. When using a common flue the inbuilt cascade control must be used.
These instructions are written for the installer of Strebel products and contain all necessary information on
the installation and adjustment of S-CB boilers. We suggest that you read the instructions before installation
to ensure that all work is done correctly. We suggest that you keep these instructions near the boiler.
4.1 Operation of the S-CB Boiler
The heating boilers from the Strebel S-CB series are central heating boilers with maximum high efficiency.
Such performance is reached by, among other things, using a special heat exchanger made of stainless steel.
The heat exchanger allows flue gases to cool down below condensation point, condensing the flue gases and
releasing extra heat. This has an immediate positive impact on the efficiency, exceeding 100%net calorific.
•
S-CB flue gases have a low temperature (below 85°C), the boiler needs to have a high efficiency
approved stainless steel or plastic flue system .Aluminium flue systems are not allowed to be
connected to these boilers. Adequate drain points must be added to the flue system with a u trap.
4.2 Controls
The Strebel S-CB Boiler adjusts to the demand for heat by using flame modulation and external controls.
That is on the basis of
1)
0 to 10 volt control.
2)
Strebel optimiser control
3)
Built in weather compensation
with an outside detector.
4)
RC or E-BUS .For RC or E-Bus system, see separate booklet.
The boiler control is equipped with:
Control for a DHW Cylinder with a diverter valve or a pump (pump via a relay both not supplied)
Connection for a Heating pump via a relay (pump and relay not supplied)
Connection for a room thermostat, on/off control, optimiser or 0 to 10 volt control (see 4.4.1).
4.3 Frost protection
Frost protection does not protect the system or system pumps. It protects the boiler.
Frost protect the system by fitting devices to link out any time controls. In a frost condition (at 7° Boiler
temperature) the Boiler internal pump starts. When the boiler water temperature falls down to 3°C, the burner
is also ignited. This operation will cease as soon as the boiler temperature has reached 10°C.
4.4 Cascade control
Using the integrated cascade control, a maximum of 8 boilers can be controlled in a cascade configuration.
The Cascade has in-built full logic step control. The Boiler will require a Flow temperature sensor and 2
wires to each boiler in a daisy chain.
When using a common flue the cascade control must be used
4.4.1 0-10 VDC connection available
The boiler is equipped to take a 0-10 VDC signal from a controller by others (set at time of commissioning)
with which up to 8 boilers can be controlled in cascade
, utilising the built in cascade manager. (0 Volt is
no heat demand.) The Boiler will require a Flow temperature sensor at extra cost.