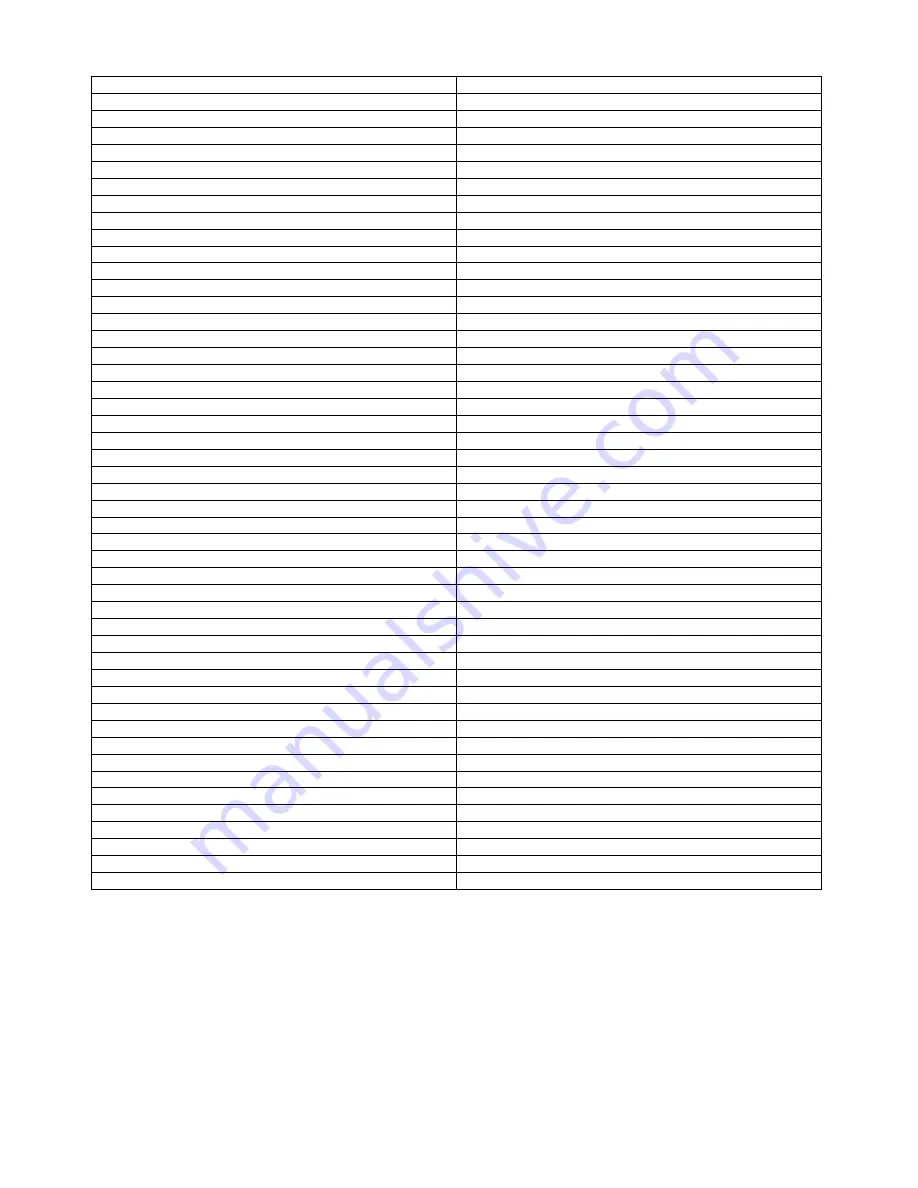
Deutsch
English
Wärmeerzeugung AUS
Heating OFF
AUSWAHL
SELECTION
INFORMATIONEN
INFORMATION
ENDE
END
Regelprogramm
Control program
Winterbetrieb
Winter operation
Höchstwert
Highest value
Betriebsstunden
Operating hours
Bereitschaft
Standby
keine Störung
no malfunction
EINSTELLUNGEN
SETTINGS
SOMMERBETRIEB
SUMMER OPERATION
AGGREGATETEST
AGGREGATE TEST
Kesselsollwert
Boiler set value
Servicecode mit
Service code with
Test
Test
Sonde
Probe
Testende
End of test
Primärpumpe
Primary pump
Rücklaufventil
Return valve
Ventilator
Fan
Türöffner
Door opener
Primärmotor
Primary motor
Sekundärmotor
Secondary motor
Ladeventil
Charging valve
Heizkreispumpe
Heating circuit pump
Ladepumpe
Charging pump
Umschaltkontakt
Switchover contact
Beleuchtung
Lighting
LED Wärmeerz.
LED Heating ON
LED Nachlegen
LED Add fuel
LED Störung
LED Malfunction
CODE Eingabe
CODE input
Sprache
Language
Kesseltyp
Boiler type
System Nr.
System no.
Sind Sie sicher?
Are you sure?
NEIN
NO
JA
YES
Speicherfühler
Storage tank sensor
Länge in m
Length in m
Speichermax.
Storage tank max.
Speichermin.
Storage tank min.
Kesselmin.
Boiler min.
Abgastemp. min.
Exhaust fume temp. min.
Anzeige nur bei System 1
Display only for system 1
Anzeige nur bei System 1 und 2
Display only for systems 1 and 2
Summary of Contents for 40S-70
Page 27: ...23 Commissioning Circuit diagram ...
Page 29: ...24 Commissioning Short operating instructions ...
Page 31: ......
Page 35: ...28 Notes ...
Page 38: ......