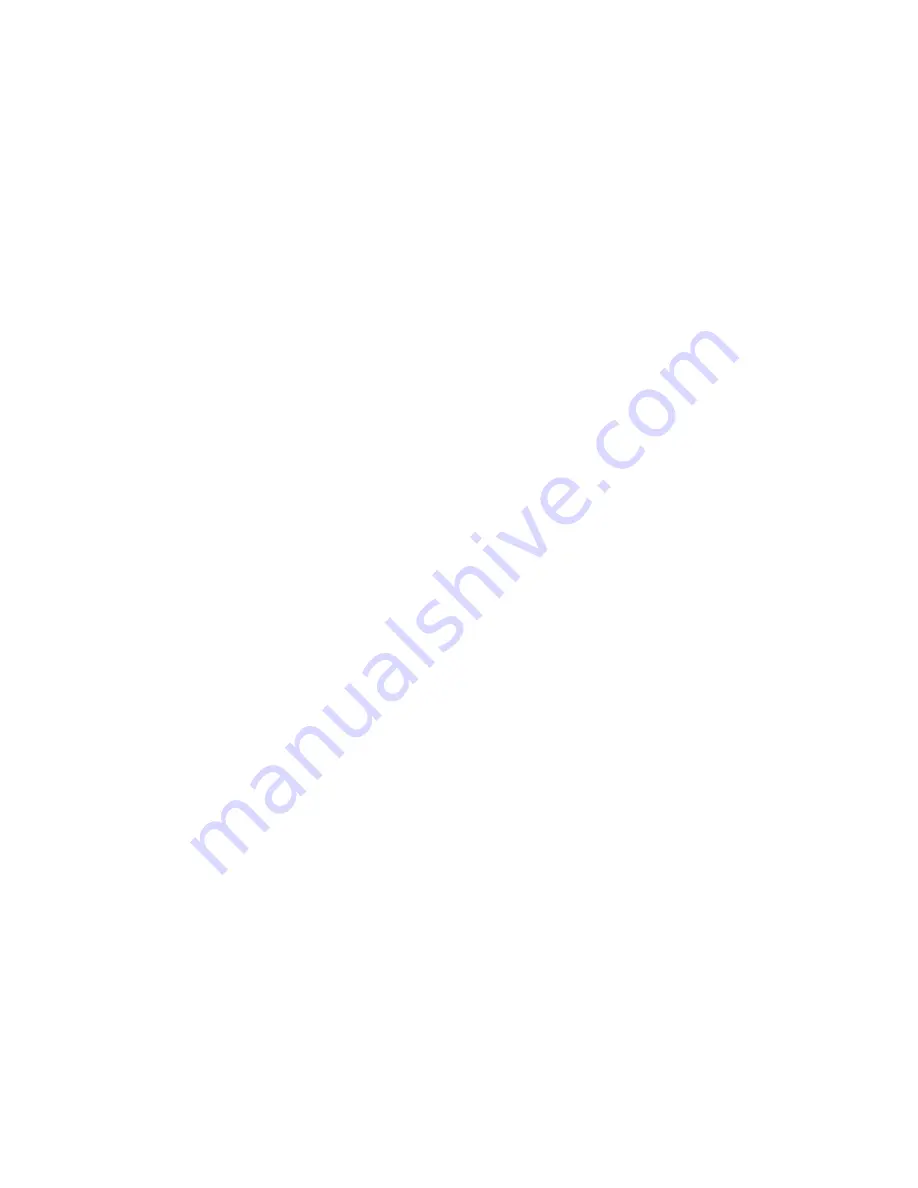
16
Installing software
There are two software programs that work with the printer:
1.
CatalystEX, installed on your workstation, processes the STL files for printing and communicates
with the printer from your workstation.
2.
System software, the operating software installed on the printer, controls printer functions.
Installing CatalystEX:
1.
Locate the CatalystEX CD from startup kit and insert into workstation (PC).
2.
Click the
Install
CatalystEX:
button.
3.
Follow prompts to finish loading CatalystEX on the workstation.
Installing System Software to the workstation:
1.
Insert the
System Software CD into the CD drive of your workstation.
2.
Click the
Install
button to load system software to your workstation. You will be asked to load
this software to your printer later.
3.
Follow prompts to finish installing system software on the workstation.
4.
Install system software to the printer, see
“Installing System Software on printer” on page 19
Establishing network communication with the printer
You will need to establish network communication between your workstation and printer before
you can send files to be built. How you establish this communication with an IP address is
dependent upon how your network and workstation are configured. If your network is configured
for DHCP (Dynamic Host Configuration Protocol), your DHCP server will automatically assign a
Dynamic IP address to your printer. This is the default setting for your printer and commonly used in
large networks. In some situations you may need to manually enter a Static IP address for your
printer and record the IP address in the CatalystEX software. Static IP addresses are frequently
used for smaller networks or for direct connection between your workstation and printer. Follow the
instructions below to configure your workstation and network.
Establishing communication on a dynamic network:
If you are on a dynamic network (or not sure of your network type) follow these steps to allow
CatalystEX to find your printer and establish communication.
1.
Connect a network cable between the printer and a network hub.
2.
Make sure the printer is ON and determine the Unique Device Name (UDN) for your printer.
a.
From
Idle
(or
Ready to Build
), press
Maintenance
on the display
panel. The display will show
Maintenance
and the software version.
b.
From the display panel press
System
.
c.
From the display panel press
Set Network
. The top window will
display:
Network Admin - Dynamic IP Address; UDN
.
d.
The Unique Device Name (UDN) for your printer is listed here. This
is preset at the factory and cannot be changed.
3.
From your workstation, start CatalystEX.
4.
From the
General
tab, click the
Manage 3D Printers
button.
5.
Click the
Add from Network
button in the lower right corner of the window.